Field Service Management with Hazard Reporting Enhancing Safety Through Efficient Incident Documentation
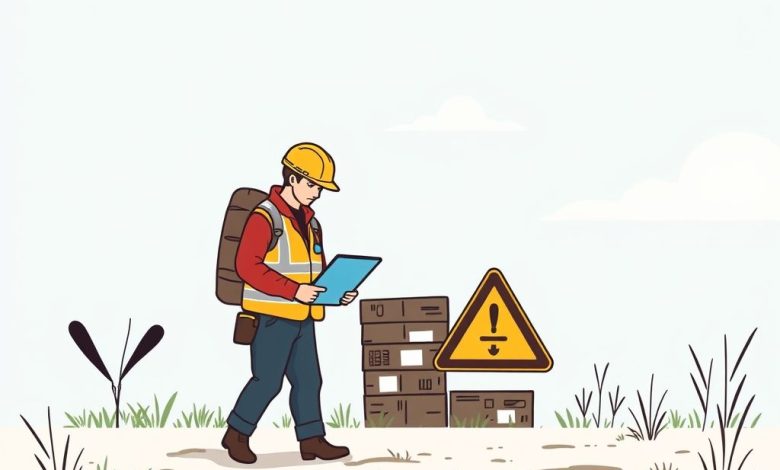
Introduction
Field Service Management (FSM) is a critical component of many industries, particularly in sectors such as construction, utilities, and manufacturing. It involves managing and coordinating the activities of workers who perform tasks outside of a traditional office environment. With the increasing complexity of operations and the need for efficient resource allocation, FSM has become more sophisticated over time.
One crucial aspect of effective FSM is hazard reporting. Hazards in the field can range from physical obstacles to environmental factors, and identifying and addressing them promptly is essential for ensuring worker safety and preventing accidents. This article will explore the intersection of Field Service Management and Hazard Reporting, discussing how these two concepts work together to create a safer and more efficient work environment.
The Importance of Hazard Reporting in Field Service Management
Hazard reporting is a vital component of any successful FSM system. By identifying potential risks before they materialize, organizations can take proactive steps to mitigate hazards and prevent accidents. This approach not only protects workers but also helps maintain productivity and reduce downtime caused by injuries or equipment damage.
Types of Hazards in Field Service Operations
Field service environments often present unique challenges that can pose significant risks to workers. Some common types of hazards include:
- Physical hazards: These may include uneven terrain, heavy lifting, and exposure to extreme temperatures.
- Environmental hazards: Examples might include inclement weather conditions, toxic substances, or confined spaces.
- Equipment-related hazards: Improperly maintained tools or machinery can cause injuries or accidents.
- Chemical hazards: Exposure to harmful chemicals during maintenance or repair work can be dangerous.
Understanding these various types of hazards is crucial for developing effective hazard reporting systems in FSM.
Implementing Hazard Reporting Systems
To effectively manage hazards in field service operations, organizations must implement robust hazard reporting systems. These systems typically involve several key components:
- Identification: Workers must be trained to recognize potential hazards in their work environment.
- Documentation: A clear process for recording and categorizing identified hazards is necessary.
- Communication: Information about hazards should be quickly disseminated throughout the organization.
- Action planning: Procedures for addressing reported hazards should be established and followed.
- Regular review: Periodic assessments of existing hazards and newly identified ones are essential.
Technology Solutions for Hazard Reporting
In today’s digital age, technology plays a significant role in improving hazard reporting processes. Various software solutions have been developed specifically for this purpose:
- Mobile apps: These allow workers to report hazards directly from the field, providing real-time updates.
- Wearable devices: Some companies use smartwatches or other wearables to monitor worker safety and detect potential hazards.
- Integrated FSM platforms: Many modern FSM systems incorporate hazard reporting features alongside scheduling and dispatch functions.
These technological advancements have significantly streamlined the hazard reporting process, making it easier for workers to identify and document potential risks.
Best Practices for Effective Hazard Reporting
While implementing a hazard reporting system is crucial, its effectiveness depends on several best practices:
- Worker training: Employees must understand what constitutes a hazard and how to properly report it.
- Confidentiality: Ensure that workers feel comfortable reporting hazards without fear of retaliation.
- Timely response: Set clear expectations for how quickly reported hazards will be addressed.
- Follow-up: Conduct regular audits to ensure that reported hazards have been adequately addressed.
- Continuous improvement: Use data from hazard reports to identify recurring issues and develop preventive measures.
By adhering to these best practices, organizations can maximize the impact of their hazard reporting systems.
Challenges in Implementing Hazard Reporting Systems
Despite the importance of hazard reporting, organizations may face several challenges when implementing such systems:
- Resistance to change: Some workers might be hesitant to adopt new reporting procedures.
- Lack of resources: Smaller companies might struggle to allocate sufficient time and money to hazard reporting initiatives.
- Complexity of some hazards: Certain risks may require specialized knowledge to identify and address effectively.
- Balancing safety and productivity: There’s often a delicate balance between ensuring worker safety and maintaining operational efficiency.
Addressing these challenges requires careful planning and commitment from management.
Case Study: Implementing Hazard Reporting in a Construction Company
To illustrate the practical application of hazard reporting in FSM, let’s consider a case study from a construction company:
XYZ Construction, a medium-sized firm specializing in commercial building projects, decided to implement a comprehensive hazard reporting system as part of their FSM strategy. They chose to use a mobile app integrated with their existing FSM platform.
The implementation process involved:
- Training sessions for all field staff on identifying and reporting hazards.
- Setting up clear categories for different types of hazards (e.g., physical, environmental, equipment-related).
- Establishing a quick-response protocol for addressing reported hazards within 24 hours.
- Regular audits to review reported hazards and assess the effectiveness of mitigation measures.
Results after six months showed a significant reduction in workplace accidents and near-misses. Workers reported feeling more secure knowing they could quickly report potential hazards. The company also noticed improved overall job satisfaction among its field staff.
Conclusion
Field Service Management with Hazard Reporting is a powerful combination that can significantly enhance workplace safety while improving operational efficiency. By implementing robust hazard reporting systems and adhering to best practices, organizations can create safer work environments and reduce the risk of accidents.
As technology continues to advance, we can expect even more sophisticated solutions for hazard reporting in FSM. However, it’s crucial to remember that effective hazard reporting relies not just on tools, but on a culture of safety awareness and proactive risk management.
For field service managers, embracing this approach means not only protecting valuable employees but also contributing to the long-term sustainability and success of their organization. As the industry evolves, staying ahead of safety trends and continuously refining hazard reporting processes will remain essential for any company operating in the dynamic world of Field Service Management.