Field Service Management vs CMMS Whats the Difference
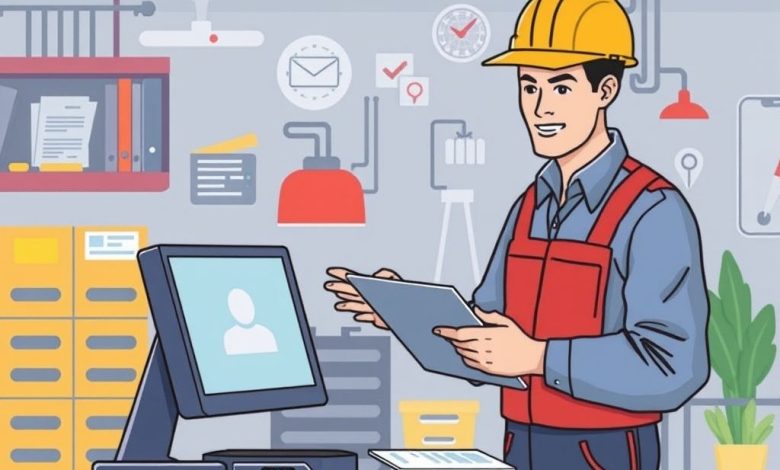
What’s the Difference? using markdown headings:
Field Service Management vs CMMS: What’s the Difference?
Introduction
Field Service Management (FSM) and Computerized Maintenance Management Systems (CMMS) are two distinct yet interconnected software solutions used by organizations to manage their maintenance and service operations. While both systems aim to improve efficiency and productivity, they serve different purposes and cater to specific needs within the field service industry.
This article will explore the key differences between Field Service Management and CMMS, highlighting their unique features, benefits, and use cases. By understanding these distinctions, organizations can make informed decisions about which system best suits their operational requirements.
Field Service Management (FSM)
Definition and Purpose
Field Service Management is a comprehensive software solution designed to streamline and optimize field service operations. It encompasses various aspects of service delivery, including scheduling, dispatching, resource allocation, and customer management.
The primary purpose of FSM is to enhance the efficiency and effectiveness of field service teams by providing real-time visibility into service operations, automating routine tasks, and enabling data-driven decision-making.
Key Features of FSM
- Scheduling and Dispatching: Advanced algorithms for optimal job assignment and route optimization
- Resource Allocation: Efficient distribution of technicians and equipment across multiple locations
- Mobile Workforce Management: Real-time tracking and monitoring of field personnel
- Customer Management: Centralized database for customer information and history
- Inventory Management: Tracking of spare parts and equipment
- Reporting and Analytics: Insights into service performance and operational metrics
Benefits of Implementing FSM
- Improved Operational Efficiency: Automated processes reduce manual errors and increase productivity
- Enhanced Customer Satisfaction: Faster response times and more accurate estimates
- Cost Reduction: Optimized resource allocation and reduced travel time
- Data-Driven Decision Making: Access to real-time insights for strategic planning
- Scalability: Ability to handle growing service volumes without compromising performance
Computerized Maintenance Management System (CMMS)
Definition and Purpose
A Computerized Maintenance Management System is a specialized software solution focused on managing preventive and corrective maintenance activities. Its primary goal is to ensure that equipment and assets are properly maintained to minimize downtime and extend their lifespan.
CMMS is particularly useful for organizations with large inventories of equipment or those operating in industries where equipment failure can have significant consequences.
Key Features of CMMS
- Equipment Tracking: Detailed inventory of all assets and their maintenance histories
- Preventive Maintenance Scheduling: Automated reminders for scheduled maintenance tasks
- Work Order Management: Creation, assignment, and tracking of maintenance requests
- Parts Inventory Management: Tracking of spare parts and consumables
- Reporting and Analytics: Insights into equipment performance and maintenance trends
- Integration Capabilities: Seamless integration with other enterprise systems
Benefits of Implementing CMMS
- Extended Equipment Lifespan: Proactive maintenance reduces unexpected failures
- Reduced Downtime: Timely completion of maintenance tasks minimizes production interruptions
- Improved Regulatory Compliance: Ensures adherence to industry-specific maintenance standards
- Cost Savings: Predictive maintenance reduces unnecessary repairs and replacements
- Better Asset Utilization: Optimal scheduling of maintenance activities based on usage patterns
Comparison of FSM and CMMS
While both FSM and CMMS are essential tools for efficient operations, they serve different purposes and cater to distinct needs:
- Scope of Operations:
- FSM: Focuses on field service operations, including scheduling, dispatching, and customer management
- CMMS: Concentrates on equipment maintenance, tracking, and scheduling
2. User Base:
- FSM: Primarily used by field service technicians and dispatchers
- CMMS: Utilized by maintenance staff, supervisors, and facilities managers
3. Integration:
- FSM: Often integrates with CRM systems and ERP platforms
- CMMS: Typically integrated with inventory management systems and enterprise asset management (EAM) solutions
4. Data Collection:
- FSM: Collects data on service requests, job completion times, and customer feedback
- CMMS: Focuses on equipment performance metrics, maintenance histories, and parts usage
Conclusion
Field Service Management and Computerized Maintenance Management Systems are both powerful tools in the field service industry, but they serve different purposes. Organizations should carefully evaluate their specific needs and operational requirements when deciding whether to implement FSM, CMMS, or both.
By leveraging these systems effectively, organizations can significantly improve their operational efficiency, reduce costs, and enhance customer satisfaction. As technology continues to evolve, we can expect these systems to become even more integrated and sophisticated, further transforming the way field service operations are managed.