Field Service Management with Subcontractor Management Optimizing Operations and Enhancing Efficiency
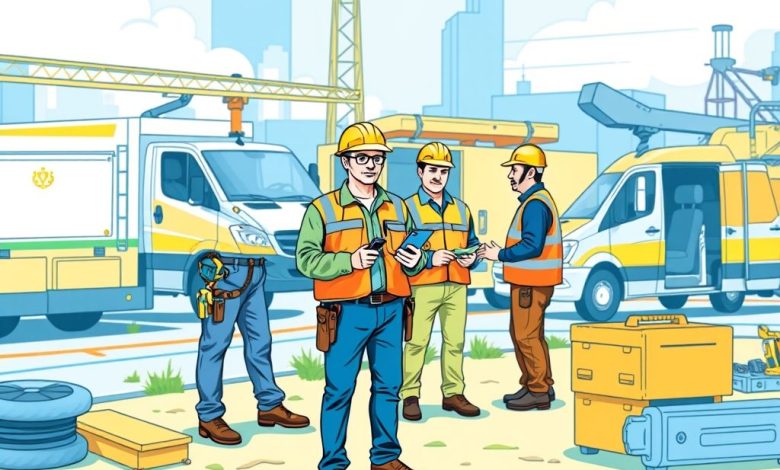
Introduction
Field Service Management (FSM) is a critical component of many businesses, particularly in industries such as HVAC, electrical work, plumbing, and home maintenance. As companies grow and expand their operations, managing a large workforce becomes increasingly challenging. This is where subcontractor management comes into play – allowing businesses to leverage external resources when needed while maintaining control over their operations.
In this article, we’ll explore the intricacies of Field Service Management with Subcontractor Management, focusing on how these two concepts intersect and complement each other. We’ll delve into the benefits, challenges, and best practices associated with implementing such a system.
- The Evolution of Field Service Management
- The Role of Subcontractor Management
- Integrating Field Service Management and Subcontractor Management
- Benefits of Combining Field Service Management and Subcontractor Management
- Challenges in Implementing Field Service Management with Subcontractor Management
- Best Practices for Implementing Field Service Management with Subcontractor Management
- Conclusion
The Evolution of Field Service Management
Field Service Management has come a long way since its inception. From paper-based scheduling systems to modern cloud-based solutions, technology has revolutionized how businesses manage their field operations. Today, FSM software offers a wide range of features designed to streamline processes, improve efficiency, and enhance customer satisfaction.
Key components of modern FSM systems include:
- Real-time job scheduling and dispatching
- Mobile apps for technicians to access work orders and track progress
- Customer relationship management (CRM) integration
- Inventory management
- Reporting and analytics tools
These advancements have significantly improved the overall effectiveness of field service operations, enabling businesses to respond quickly to customer needs and maintain high levels of productivity.
The Role of Subcontractor Management
Subcontractor management is an essential aspect of Field Service Management, especially for larger organizations or those experiencing rapid growth. By leveraging external resources, businesses can:
- Scale their operations more efficiently
- Access specialized skills when needed
- Reduce overhead costs associated with full-time employees
- Maintain flexibility in response to changing market demands
Effective subcontractor management involves several key elements:
- Vendor selection and qualification
- Job assignment and scheduling
- Performance monitoring and feedback
- Payment processing and invoicing
- Compliance with labor laws and regulations
Integrating Field Service Management and Subcontractor Management
The intersection of Field Service Management and Subcontractor Management creates a powerful synergy that can significantly boost operational efficiency. Here are some ways these two concepts work together:
- Unified Platform: Many FSM systems now incorporate subcontractor management features, providing a single platform for both internal and external workforce management.
- Automated Scheduling: Advanced FSM software can automatically assign jobs to either internal staff or qualified subcontractors based on factors like skill level, location, and availability.
- Real-time Communication: Mobile apps allow for seamless communication between dispatchers, technicians, and subcontractors, ensuring everyone is informed about job status and any changes.
- Quality Control: FSM systems often include performance tracking mechanisms, which can be applied to both internal staff and subcontractors, helping to maintain consistent quality standards.
- Cost Allocation: Accurate tracking of time and materials spent on jobs allows for better cost allocation between internal resources and external contractors.
Benefits of Combining Field Service Management and Subcontractor Management
The integration of FSM and subcontractor management offers numerous advantages:
- Improved Efficiency: By automating many administrative tasks and streamlining workflows, businesses can reduce operational costs and increase productivity.
- Enhanced Flexibility: The ability to quickly scale operations by bringing in subcontractors during peak periods or for specific projects allows for better adaptability to market conditions.
- Specialized Skills: Companies can access specialized expertise through subcontractors without the long-term commitment of hiring permanent staff.
- Risk Mitigation: By spreading workload across various resources, businesses can mitigate risks associated with relying solely on internal staff.
- Competitive Advantage: Organizations that effectively manage both internal and external resources tend to offer faster response times and higher-quality services to customers.
Challenges in Implementing Field Service Management with Subcontractor Management
While the benefits are clear, implementing a comprehensive FSM system that includes subcontractor management comes with its own set of challenges:
- Technology Adoption: Some subcontractors may resist adopting new technology or may lack the necessary digital literacy to effectively use FSM software.
- Data Security: Ensuring the security of sensitive business information when working with external parties is crucial.
- Compliance Issues: Managing multiple workforce types across different jurisdictions can lead to compliance headaches if not properly addressed.
- Performance Monitoring: Maintaining consistent quality standards across both internal staff and subcontractors can be challenging.
- Integration Complexity: Combining FSM software with existing systems and processes may require significant IT resources and time investment.
Best Practices for Implementing Field Service Management with Subcontractor Management
To overcome the challenges and maximize the benefits of combining FSM and subcontractor management, consider the following best practices:
- Thorough Vendor Qualification: Develop a rigorous vetting process for subcontractors to ensure they meet quality standards.
- Standardized Work Orders: Create clear, consistent work order templates that all technicians and subcontractors can easily follow.
- Regular Training: Provide ongoing training for both internal staff and subcontractors on FSM software and best practices.
- Performance Metrics: Establish clear performance metrics that apply equally to all workforce types to maintain consistency.
- Regular Audits: Conduct periodic audits to ensure compliance with labor laws and company policies.
- Open Communication Channels: Foster open communication between dispatchers, technicians, and subcontractors to address any issues promptly.
- Continuous Improvement: Regularly review and refine processes based on feedback from all stakeholders.
Conclusion
Field Service Management and Subcontractor Management are powerful tools when combined effectively. By leveraging technology to streamline operations and integrate internal and external resources, businesses can significantly improve their ability to deliver high-quality services efficiently.
As the field service industry continues to evolve, the importance of robust FSM systems that incorporate subcontractor management will only grow. Companies that embrace these technologies will be better positioned to compete in today’s fast-paced market while maintaining flexibility and scalability.
By understanding the intricacies of FSM and subcontractor management, field service managers can make informed decisions about how to structure their operations for maximum efficiency and effectiveness. As technology continues to advance, it’s exciting to consider what innovations may emerge in the future to further enhance these critical business processes.