Field Service Management with Part Delivery Coordination
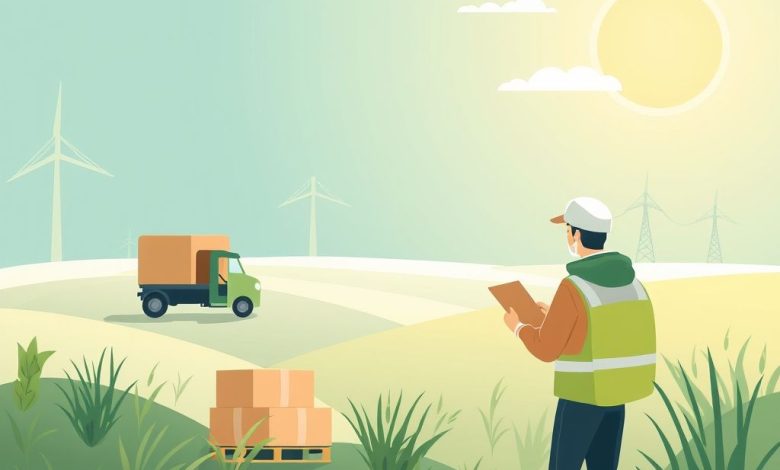
Introduction
Field Service Management (FSM) is a critical component of modern business operations, particularly in industries such as manufacturing, healthcare, and telecommunications. As companies strive to provide efficient and effective customer service, FSM has evolved to incorporate advanced technologies and strategies. One key aspect of this evolution is the integration of part delivery coordination into the overall FSM process.
Part delivery coordination refers to the systematic approach of ensuring that necessary parts and equipment are delivered to the right place at the right time to support field technicians. This practice enhances operational efficiency, reduces downtime, and improves overall customer satisfaction.
In this article, we will explore the importance of integrating part delivery coordination into field service management systems. We’ll examine how this approach benefits both businesses and customers, discuss the challenges associated with implementation, and highlight best practices for successful adoption.
The Importance of Part Delivery Coordination in FSM
Effective part delivery coordination is crucial for several reasons:
- Reduced Downtime: When technicians have immediate access to required parts, they can complete repairs more quickly, minimizing downtime for customers and reducing lost revenue for businesses.
- Improved Customer Satisfaction: Prompt resolution of issues leads to higher customer satisfaction scores, which is essential for building long-term relationships and generating positive word-of-mouth marketing.
- Increased Operational Efficiency: By streamlining the parts ordering and delivery process, businesses can optimize their resource allocation and reduce unnecessary delays.
- Cost Savings: Efficient part delivery coordination can help reduce inventory costs by avoiding overstocking and minimizing waste.
- Enhanced Technician Productivity: With readily available parts, technicians can focus on completing jobs rather than searching for missing components.
Challenges in Implementing Part Delivery Coordination
While the benefits of part delivery coordination are clear, implementing this system presents several challenges:
- Integration Complexity: Incorporating part delivery coordination into existing FSM systems often requires significant IT infrastructure changes and may necessitate updates to software applications.
- Inventory Management: Accurately tracking and managing inventory levels across multiple locations can be challenging, especially when dealing with high-volume, fast-moving parts.
- Real-time Tracking: Ensuring real-time visibility of part location and status throughout the delivery process can be technically demanding.
- Scalability: As businesses grow, maintaining an efficient part delivery system becomes increasingly complex, requiring robust scalability solutions.
- Security Concerns: Managing sensitive customer data and proprietary information during part deliveries requires robust security measures.
Best Practices for Implementing Part Delivery Coordination
To overcome the challenges associated with part delivery coordination, consider the following best practices:
- Invest in Advanced Technology: Utilize cloud-based FSM software that includes built-in part ordering and tracking features. This ensures real-time visibility and automated workflows.
- Implement RFID Technology: Radio Frequency Identification tags can provide precise location tracking of parts throughout the supply chain.
- Develop Standardized Processes: Create clear procedures for part ordering, inventory management, and delivery tracking to ensure consistency across teams.
- Conduct Regular Audits: Periodically review part inventory levels and delivery processes to identify areas for improvement.
- Provide Training: Ensure all staff members involved in the part delivery process receive comprehensive training on new systems and procedures.
Case Study: Implementing Part Delivery Coordination at XYZ Corporation
XYZ Corporation, a leading manufacturer of medical equipment, faced significant challenges with their field service operations. Technicians often reported delays due to missing parts, resulting in extended downtime for customers and lost revenue for the company.
To address this issue, XYZ implemented a comprehensive FSM system with integrated part delivery coordination. The solution included:
- A cloud-based FSM platform with automated part ordering functionality
- RFID tags on all critical components
- Real-time tracking of part location and status
- Standardized processes for part requisition and delivery management
Results after implementation:
- Reduced average repair time by 35%
- Improved first-time fix rate from 70% to 85%
- Decreased customer complaints related to delayed repairs by 50%
- Achieved a 15% reduction in overall operational costs
Conclusion
Field Service Management with integrated part delivery coordination has become essential for businesses seeking to provide efficient and effective customer service. By implementing advanced technology solutions, developing standardized processes, and investing in best practices, companies can overcome the challenges associated with part delivery coordination.
As the field service industry continues to evolve, it’s clear that part delivery coordination will play an increasingly important role in determining operational efficiency and customer satisfaction. Businesses that prioritize this aspect of FSM will be well-positioned to thrive in today’s competitive market.
By leveraging cutting-edge technologies and adopting proven strategies, field service managers can optimize their operations, reduce costs, and deliver exceptional value to both their organizations and their customers.