Field Service Management with Smart Asset Tagging Enhancing Efficiency and Accuracy in Equipment Tracking
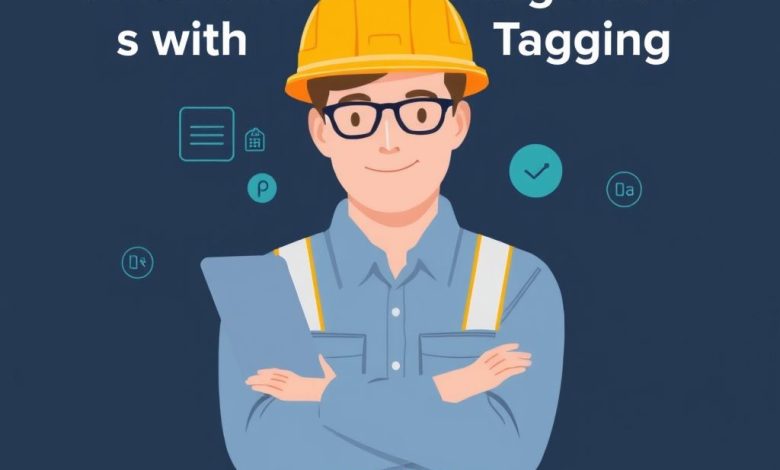
Introduction
Field Service Management (FSM) is a critical component of many industries, including manufacturing, healthcare, and telecommunications. It involves managing and coordinating the activities of technicians and other personnel who provide services outside of a traditional office environment. With the advent of smart asset tagging and Internet of Things (IoT) technology, FSM has evolved significantly, offering more efficient and effective solutions for businesses.
The Evolution of Field Service Management
Traditionally, FSM relied heavily on manual processes and paper-based systems. Technicians would receive work orders through phone calls or emails, travel to customer locations, perform the required tasks, and then return to the office to update records manually. This approach was time-consuming, prone to errors, and lacked real-time visibility into operations.
The introduction of computerized maintenance management systems (CMMS) brought significant improvements. These systems allowed for better scheduling, inventory management, and reporting. However, they still had limitations when it came to real-time tracking and monitoring of assets in the field.
Smart Asset Tagging and IoT Technology
Smart asset tagging refers to the use of RFID (Radio-Frequency Identification), GPS, or other wireless technologies to track and monitor physical assets. When combined with IoT technology, this allows for real-time data collection and analysis from the field.
Benefits of Smart Asset Tagging
- Real-time Tracking: Smart tags enable real-time location tracking of assets, improving response times and reducing travel costs.
- Condition Monitoring: Sensors embedded in smart tags can monitor the condition of equipment, predicting potential failures before they occur.
- Automated Reporting: Data collected by smart tags can be automatically fed into CMMS systems, reducing manual data entry and increasing accuracy.
- Improved Inventory Management: Smart tags help maintain accurate inventory levels and prevent stockouts or overstocking.
- Enhanced Customer Experience: Real-time updates allow for more precise appointment scheduling and improved communication with customers.
Implementation of Smart Asset Tagging in Field Service Management
Implementing smart asset tagging in FSM involves several steps:
- Asset Identification: Identify all assets that require tracking or monitoring.
- Tag Selection: Choose appropriate tags based on the type of asset and required functionality.
- Data Integration: Integrate data from smart tags with existing FSM systems and processes.
- Training: Provide technicians with necessary training on using and maintaining smart tags.
- Continuous Monitoring: Regularly review and optimize the system based on performance metrics.
Case Studies
Several companies have successfully implemented smart asset tagging in their FSM systems:
Example 1: Utility Company
A large utility company implemented smart meters with built-in GPS and temperature sensors. This allowed them to:
- Track meter installations in real-time
- Monitor energy consumption patterns
- Identify potential issues before they became major problems
As a result, the company reduced response times by 30% and improved overall efficiency by 25%.
Example 2: Manufacturing Equipment
A manufacturing plant equipped its production equipment with smart tags containing vibration sensors. This enabled:
- Predictive maintenance scheduling
- Reduced downtime by 40%
- Extended equipment lifespan by 20%
Challenges and Limitations
While smart asset tagging offers numerous benefits, it also comes with challenges:
- Initial Investment: Implementing a comprehensive FSM system with smart asset tagging requires significant upfront investment in hardware and software.
- Data Security: The increased amount of data collected by smart tags raises concerns about data privacy and security.
- Interoperability: Ensuring seamless integration between different systems and technologies can be complex.
- Battery Life: For wireless tags, battery life remains a concern, especially for assets that require long-term monitoring.
Conclusion
Field Service Management with Smart Asset Tagging represents a significant leap forward in operational efficiency and effectiveness. By leveraging IoT technology and real-time data collection, businesses can optimize their field service operations, improve customer satisfaction, and reduce costs.
As technology continues to evolve, we can expect even more sophisticated solutions for FSM. However, it’s crucial for businesses to carefully consider their specific needs and resources when implementing such systems. With proper planning and execution, smart asset tagging can be a game-changer for field service management, enabling companies to respond faster, work smarter, and deliver better results.