Field Service Management with Equipment Lifecycle Tracking
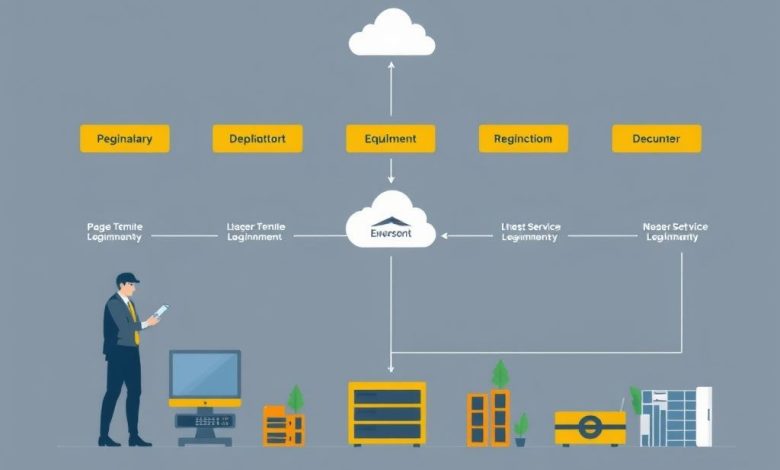
Field Service Management with Equipment Lifecycle Tracking
Introduction
Field service management (FSM) refers to the processes and systems used to manage and coordinate work performed outside of a traditional office environment. This includes tasks such as equipment maintenance, repairs, installations, and other services delivered directly to customers’ locations. In recent years, FSM has evolved to incorporate advanced technologies like equipment lifecycle tracking, which provides real-time visibility into the status and condition of assets throughout their entire life cycle.
Equipment lifecycle tracking involves monitoring the performance, usage, and condition of equipment over time. This data is collected through various methods, including sensors, software applications, and manual inputs. By leveraging this information, organizations can optimize their FSM operations, improve efficiency, reduce costs, and enhance customer satisfaction.
This article will explore the concept of field service management with equipment lifecycle tracking, its benefits, challenges, and best practices for implementation. We will examine how this technology is transforming the way businesses approach asset management and customer service delivery.
Benefits of Field Service Management with Equipment Lifecycle Tracking
Improved Efficiency
One of the primary advantages of implementing FSM with equipment lifecycle tracking is increased operational efficiency. By having real-time insights into equipment status and performance, technicians can:
- Prioritize jobs based on urgency and criticality
- Optimize travel routes to minimize downtime
- Reduce unnecessary site visits due to inaccurate or outdated information
For example, a manufacturing company might use equipment lifecycle tracking to identify which machines require immediate attention before they break down, allowing them to schedule preventive maintenance proactively.
Enhanced Customer Experience
FSM with equipment lifecycle tracking enables companies to provide more responsive and personalized service to their customers. Some ways this improves customer experience include:
- Faster response times to equipment failures
- More accurate estimates and scheduling
- Proactive communication about potential issues or upcoming maintenance
A utility company could leverage this technology to notify customers when their equipment is approaching the end of its useful life, allowing them to plan for replacements or upgrades.
Cost Savings
Implementing FSM with equipment lifecycle tracking can lead to significant cost reductions for organizations. Some key areas where savings can be achieved include:
- Reduced emergency callouts due to proactive maintenance
- Lower fuel consumption through optimized routing
- Extended equipment lifespan through better utilization and care
An HVAC company might use this technology to predict when air conditioning units need replacement, allowing them to budget accordingly and avoid unexpected breakdowns during peak seasons.
Data-Driven Decision Making
FSM with equipment lifecycle tracking generates vast amounts of data that can be analyzed to inform strategic decisions. This data can reveal patterns and trends such as:
- Most common equipment failures
- Peak usage periods
- Geographic hotspots for service requests
By leveraging this information, businesses can refine their service offerings, adjust staffing levels, and optimize resource allocation. For instance, a construction equipment rental company might use this data to determine which types of machinery are in highest demand and adjust their inventory accordingly.
Challenges in Implementing Field Service Management with Equipment Lifecycle Tracking
While the benefits of FSM with equipment lifecycle tracking are substantial, there are several challenges that organizations may face when implementing this technology:
Integration Complexity
Integrating equipment lifecycle tracking systems with existing FSM platforms can be challenging, especially for companies with legacy systems. This integration requires careful planning and often necessitates updates to both hardware and software infrastructure.
Data Privacy Concerns
Collecting and storing detailed equipment data raises concerns about privacy and security. Organizations must ensure that sensitive information is protected and comply with relevant regulations such as GDPR.
Initial Investment Costs
Implementing FSM with equipment lifecycle tracking typically requires a significant upfront investment in hardware, software, and training. This can be a barrier for smaller organizations or those with limited budgets.
Technological Dependence
Overreliance on technology can sometimes lead to decreased human skills and judgment. It’s crucial to strike a balance between leveraging technology and maintaining human expertise in field service management.
Best Practices for Implementing Field Service Management with Equipment Lifecycle Tracking
To ensure successful implementation and maximize benefits, consider the following best practices:
Start Small
Begin by implementing equipment lifecycle tracking for a limited number of high-value or critical assets before expanding to the entire fleet. This allows organizations to refine their processes and address any challenges without overwhelming their systems.
Invest in Training
Provide comprehensive training to field technicians on how to use new equipment tracking devices and interpret data from the system. This ensures they can make informed decisions based on real-time information.
Regular Maintenance
Implement regular maintenance schedules for both the equipment being tracked and the tracking systems themselves. This helps maintain accuracy and prevent downtime due to faulty sensors or software glitches.
Continuous Monitoring and Improvement
Regularly review and analyze data from the equipment lifecycle tracking system to identify areas for improvement. Use this feedback to refine processes and optimize operations continuously.
Conclusion
Field service management with equipment lifecycle tracking represents a significant advancement in the way businesses approach asset management and customer service delivery. By leveraging advanced technologies to monitor equipment performance and status in real-time, organizations can improve efficiency, enhance customer experience, reduce costs, and make data-driven decisions.
While implementation may present challenges such as integration complexity and initial investment costs, the long-term benefits far outweigh these obstacles for many companies. As technology continues to evolve, FSM with equipment lifecycle tracking will likely play an increasingly important role in shaping the future of field service operations.
For field service managers looking to stay competitive in today’s fast-paced business environment, embracing this technology could be the key to unlocking operational excellence and driving sustainable growth.