Field Service Management for Food Equipment Maintenance
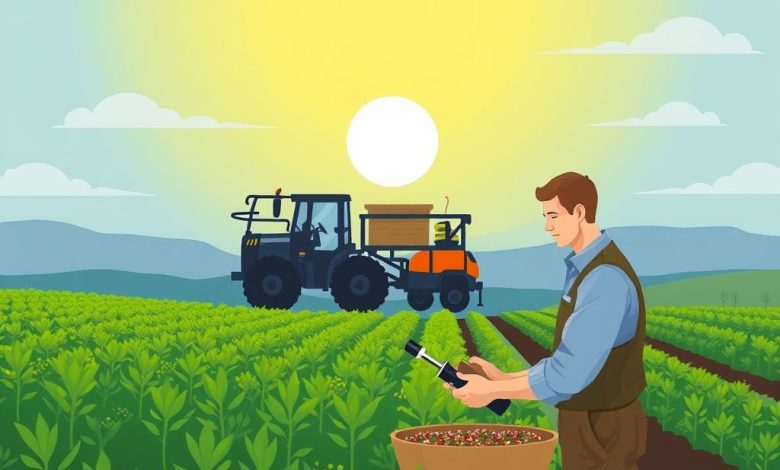
Field Service Management for Food Equipment Maintenance
- Introduction
- Key Components of Field Service Management Software
- Work Order Management
- Inventory Management
- Scheduling and Dispatch
- Customer Relationship Management (CRM)
- Best Practices for Implementing FSM in Food Equipment Maintenance
- Standardize Work Orders
- Invest in Proper Training
- Implement a Tiered Support System
- Utilize Mobile Technology
- Regularly Review and Update Procedures
- Challenges in FSM for Food Equipment Maintenance
- Conclusion
Introduction
Field service management (FSM) plays a crucial role in maintaining food equipment across various industries. From restaurants to hospitals, efficient FSM ensures that commercial kitchen appliances remain operational, reducing downtime and improving overall efficiency. This article explores the importance of FSM in food equipment maintenance, highlighting key strategies and best practices for field service managers.
The Importance of FSM in Food Equipment Maintenance
Food equipment maintenance requires specialized knowledge and attention to detail. Commercial kitchen appliances are subject to harsh conditions, including high temperatures, humidity, and frequent use. Without proper maintenance, these machines can break down, leading to costly repairs and potential safety hazards.
Effective FSM helps mitigate these risks by:
- Scheduling regular preventive maintenance visits
- Conducting thorough inspections of equipment
- Identifying and addressing issues before they become major problems
- Providing prompt repairs and replacements when necessary
By implementing robust FSM practices, businesses can extend the lifespan of their equipment, reduce maintenance costs, and ensure compliance with health and safety regulations.
Key Components of Field Service Management Software
Modern FSM software has evolved significantly, offering a range of features that streamline maintenance processes. Some essential components include:
Work Order Management
Work order management is at the heart of any FSM system. It allows technicians to receive, prioritize, and manage service requests efficiently. Key features typically include:
- Automated assignment of work orders based on technician availability and location
- Real-time updates on work order status
- Integration with GPS tracking for accurate location-based services
Inventory Management
Proper inventory management is critical for effective FSM. It ensures that technicians have the necessary parts and tools to complete jobs efficiently. Essential features often include:
- Centralized inventory database
- Automatic stock alerts when levels drop below a certain threshold
- Barcode scanning for quick part identification
Scheduling and Dispatch
Scheduling and dispatch functionality allows businesses to optimize resource allocation. Features may include:
- Drag-and-drop scheduling interface
- Multi-resource scheduling capabilities
- Route optimization algorithms for efficient travel planning
Customer Relationship Management (CRM)
A robust CRM system helps maintain strong relationships with clients. Common features include:
- Customer history and preferences storage
- Automated reminders for scheduled maintenance
- Customizable communication channels (email, SMS, phone)
Best Practices for Implementing FSM in Food Equipment Maintenance
To maximize the benefits of FSM software, consider the following best practices:
Standardize Work Orders
Develop standardized work orders that cover all common maintenance tasks. This ensures consistency across all service visits and makes it easier to track historical data.
Invest in Proper Training
Ensure that all technicians receive comprehensive training on the FSM software and the specific food equipment being maintained. This includes understanding manufacturer specifications, troubleshooting techniques, and safety protocols.
Implement a Tiered Support System
Create a tiered support structure where less experienced technicians assist more senior team members. This allows for knowledge transfer and skill development while ensuring quality control.
Utilize Mobile Technology
Leverage mobile apps to streamline the service process. These apps can provide real-time updates, allow for electronic signatures, and enable instant communication between technicians and dispatchers.
Regularly Review and Update Procedures
Periodically review and update maintenance procedures based on industry trends, new equipment models, and customer feedback. This ensures that the FSM system remains current and effective.
Challenges in FSM for Food Equipment Maintenance
Despite its numerous benefits, implementing FSM for food equipment maintenance comes with several challenges:
Technological Limitations
Some older food equipment may not be compatible with modern FSM systems, requiring manual workarounds or custom integrations.
Regulatory Compliance
Different regions have varying health and safety regulations. Ensuring compliance with local laws while maintaining efficient FSM processes can be challenging.
Seasonal Fluctuations
In some industries, such as hospitality, there may be significant seasonal fluctuations in demand for maintenance services. FSM systems must be flexible enough to accommodate these changes.
Remote Access Issues
For some types of equipment, remote diagnostics and troubleshooting may not be feasible due to security concerns or physical limitations.
Conclusion
Field service management is a critical component of food equipment maintenance, offering numerous benefits for businesses operating in the food service industry. By leveraging advanced FSM software and implementing best practices, organizations can improve efficiency, reduce costs, and ensure the longevity of their equipment.
As technology continues to evolve, FSM solutions will likely incorporate even more sophisticated features, such as artificial intelligence for predictive maintenance and augmented reality for remote assistance. However, regardless of future advancements, the core principles of effective FSM – standardization, training, and continuous improvement – will remain essential for success in this field.
By investing in robust FSM systems and adhering to best practices, field service managers can play a vital role in maintaining the smooth operation of food equipment, contributing to the success of their clients and the overall efficiency of the food service industry.