Field Service Management for Calibration Tracking Optimizing Equipment Precision and Operational Efficiency
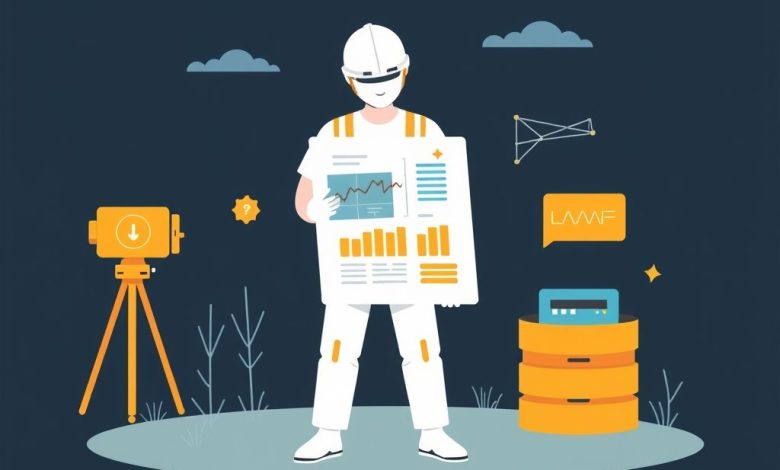
Introduction
Field Service Management (FSM) is a critical component of modern business operations, particularly in industries where equipment maintenance and calibration are essential. In this article, we’ll explore the importance of FSM in calibration tracking, its benefits, challenges, and best practices for implementation.
What is Field Service Management?
Field Service Management refers to the processes and systems used to manage and coordinate work activities performed outside of a traditional office environment. It encompasses various aspects of service delivery, including scheduling, dispatching, resource allocation, and customer communication.
Key Components of FSM
- Scheduling and Dispatching
- Efficiently allocating technicians to jobs based on location, skillset, and availability
- Optimizing routes to minimize travel time and reduce costs
2. Resource Allocation
- Managing inventory of spare parts and tools
- Assigning appropriate equipment to each job
3. Work Order Management
- Creating, assigning, and tracking work orders electronically
- Ensuring all necessary information is captured and accessible
4. Customer Communication
- Providing timely updates on job status and estimated completion times
- Handling customer inquiries and feedback
5. Performance Monitoring
- Tracking key performance indicators such as first-time fix rates and response times
- Identifying areas for improvement in service delivery
The Importance of Calibration Tracking in Field Service Management
Calibration tracking is a crucial aspect of many industries, including manufacturing, healthcare, and scientific research. Proper calibration ensures that equipment operates within specified tolerances, maintaining accuracy and safety standards.
Benefits of Effective Calibration Tracking
- Improved Accuracy
- Regular calibration helps maintain precise measurements and results
- Reduces errors in data collection and decision-making
2. Enhanced Safety
- Prevents accidents caused by malfunctioning equipment
- Complies with regulatory requirements and industry standards
3. Increased Efficiency
- Minimizes downtime due to equipment failures
- Extends the lifespan of calibrated instruments
4. Cost Savings
- Reduces the need for frequent equipment replacement
- Decreases liability associated with inaccurate measurements
Challenges in Implementing Calibration Tracking in Field Service Management
Despite its importance, implementing effective calibration tracking in FSM presents several challenges:
- Data Management
- Storing and organizing calibration records for numerous pieces of equipment
- Ensuring accessibility and security of sensitive data
2. Standardization
- Establishing consistent calibration procedures across different types of equipment
- Adapting to changes in measurement standards over time
3. Technician Training
- Educating field technicians on proper calibration techniques
- Keeping them updated on latest calibration methods and technologies
4. Scheduling Conflicts
- Coordinating calibration checks with ongoing service activities
- Balancing immediate service needs with preventive maintenance schedules
Best Practices for Implementing Calibration Tracking in Field Service Management
To overcome the challenges and maximize the benefits of calibration tracking in FSM, consider the following best practices:
- Invest in a Comprehensive FSM Software
- Choose a system that integrates scheduling, work order management, and calibration tracking
- Ensure real-time access to calibration records from the field
2. Develop Standard Operating Procedures (SOPs)
- Create detailed SOPs for calibration procedures specific to each type of equipment
- Regularly review and update SOPs to reflect changes in technology and regulations
3. Implement a Robust Quality Control System
- Conduct regular audits to ensure compliance with calibration standards
- Track and analyze calibration data to identify trends and potential issues
4. Provide Ongoing Training and Support
- Offer continuous training for field technicians on calibration techniques and best practices
- Maintain a knowledge base of common calibration issues and solutions
5. Integrate Calibration Tracking with Asset Management
- Link calibration records to individual assets for easy traceability
- Set reminders for upcoming calibrations based on asset usage patterns
6. Leverage IoT Technologies
- Utilize smart sensors and connected devices to monitor equipment performance in real-time
- Automate calibration alerts based on predefined thresholds and usage patterns
7. Foster Collaboration Between Field Technicians and Calibration Experts
- Encourage open communication between field staff and calibration specialists
- Cross-train technicians on basic calibration principles to improve troubleshooting capabilities
8. Implement a Closed-Loop Feedback System
- Collect feedback from customers and internal stakeholders on calibration services
- Use this feedback to continuously improve calibration processes and outcomes
Conclusion
Field Service Management plays a vital role in ensuring the effectiveness of calibration tracking. By implementing robust FSM systems, developing standardized procedures, and fostering a culture of quality control, organizations can significantly enhance their ability to maintain accurate and reliable equipment.
As technology continues to evolve, it’s crucial for businesses to stay ahead of the curve in FSM and calibration tracking. By leveraging innovative solutions like IoT devices and AI-powered predictive maintenance, companies can anticipate and address calibration needs before they become critical issues.
In the ever-changing landscape of industrial operations, embracing Field Service Management for Calibration Tracking is not just a best practice – it’s a necessity for maintaining competitive advantage and ensuring operational excellence.