Field Service Management Leveraging AI for Intelligent Spare Part Matching
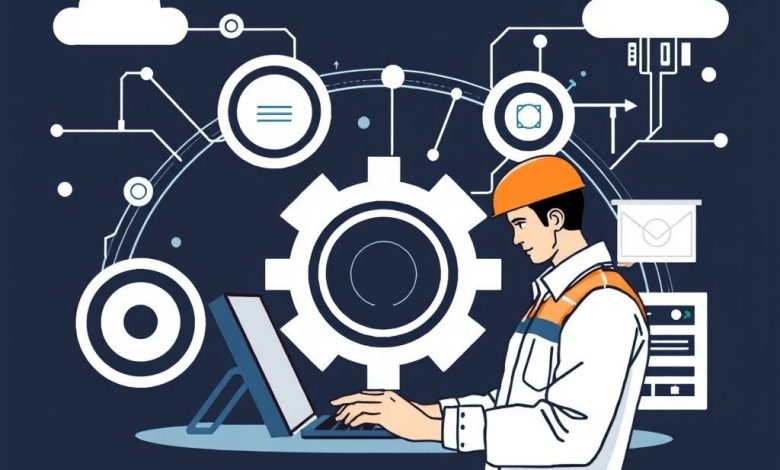
Field Service Management for AI-Powered Spare Part Matching
Introduction
Field service management (FSM) is a critical component of modern business operations, particularly in industries such as manufacturing, construction, and utilities. The traditional approach to FSM relied heavily on manual processes and human expertise, but advancements in artificial intelligence (AI) have revolutionized this field. One significant area where AI is making a substantial impact is in spare part matching for field service operations.
This article will explore the concept of AI-powered spare part matching within the context of field service management. We’ll examine how AI technologies are being integrated into existing FSM systems to improve efficiency, reduce costs, and enhance customer satisfaction.
The Challenge of Spare Part Matching
Spare part matching is one of the most crucial aspects of field service operations. It involves identifying the correct replacement parts needed to repair equipment or machinery in the field. This process can be challenging due to several factors:
- Complexity of equipment: Modern industrial equipment often consists of numerous interconnected components, making it difficult to determine which specific part is faulty.
- Rapid technological advancements: New equipment models and designs emerge frequently, requiring constant updates to spare parts inventory and matching systems.
- Limited visibility: Field technicians often lack real-time access to detailed information about the equipment they’re working on.
- Time constraints: In many cases, field service engineers need to make quick decisions about replacement parts without the luxury of extensive research or consultation with experts.
AI-Powered Spare Part Matching Solutions
AI-powered solutions are addressing these challenges by providing intelligent support to field service operations. These systems leverage machine learning algorithms and natural language processing to analyze vast amounts of data related to equipment, spare parts, and field service activities.
- Predictive Maintenance:
AI-powered predictive maintenance systems can forecast equipment failures based on historical data, usage patterns, and environmental factors. This allows field service managers to proactively order spare parts and schedule maintenance visits. - Automated Part Identification:
Advanced computer vision techniques enable AI systems to identify faulty components using images captured during field inspections. This eliminates the need for human expertise in part identification and reduces errors associated with manual diagnosis. - Real-time Inventory Management:
AI-driven inventory management systems continuously monitor stock levels and optimize reordering processes. They can predict demand based on seasonal trends, weather patterns, and other external factors. - Intelligent Routing and Scheduling:
AI algorithms optimize route planning and scheduling for field service technicians. By considering factors such as traffic patterns, technician availability, and customer priority, these systems ensure efficient allocation of resources.
Implementation Strategies
Implementing AI-powered spare part matching solutions requires careful consideration of several factors:
- Data Integration:
Ensure seamless integration of existing FSM systems with AI platforms. This may involve migrating legacy data to cloud-based storage solutions compatible with AI applications. - Training and Adoption:
Provide comprehensive training to field service staff on new AI tools and workflows. Address concerns about job displacement and emphasize how AI enhances rather than replaces human expertise. - Change Management:
Implement a phased rollout approach to minimize disruption to ongoing operations. Start with pilot projects in specific regions or departments before scaling up across the organization. - Continuous Monitoring and Evaluation:
Establish key performance indicators (KPIs) to measure the impact of AI implementation. Regularly assess improvements in response times, accuracy of part matching, and overall operational efficiency.
Case Studies and Success Stories
Several companies have successfully implemented AI-powered spare part matching solutions, resulting in significant improvements to their field service operations:
- Siemens: The German industrial conglomerate reported a 30% reduction in repair times and a 25% decrease in spare parts inventory costs after implementing an AI-driven FSM system.
- Schneider Electric: The energy management company saw a 40% increase in first-time fix rates and a 15% improvement in technician productivity following the introduction of AI-powered diagnostic tools.
- Caterpillar Inc.: The heavy machinery manufacturer reduced its average repair time by 20% and improved part utilization by 12% after integrating AI-driven inventory optimization into its FSM platform.
Challenges and Limitations
While AI-powered spare part matching offers numerous benefits, there are some challenges and limitations to consider:
- Data Quality Issues:
AI systems require high-quality, consistent data to produce accurate results. Poor data quality can lead to suboptimal decision-making and reduced system effectiveness. - Privacy Concerns:
The collection and analysis of large amounts of field service data raise privacy concerns. Organizations must implement robust security measures to protect sensitive information. - Technical Complexity:
Integrating AI solutions into existing FSM systems can be complex and time-consuming. It may require significant investment in IT infrastructure and personnel training. - Human-AI Collaboration:
There’s still a need for human expertise in interpreting AI-generated recommendations and making final decisions. Ensuring effective collaboration between humans and AI systems remains a challenge.
Conclusion
Field Service Management for AI-Powered Spare Part Matching represents a significant leap forward in operational efficiency and customer satisfaction. As AI technologies continue to evolve, we can expect even more sophisticated solutions to emerge, further transforming the landscape of field service operations.
For field service managers, embracing AI-powered spare part matching is not just a matter of keeping pace with technological advancements—it’s a necessity for remaining competitive in today’s fast-paced business environment. By leveraging AI capabilities, organizations can streamline their operations, reduce costs, and deliver superior service to their customers.
However, successful implementation requires careful planning, change management strategies, and a commitment to continuous learning and adaptation. As AI continues to reshape the field service industry, those who embrace these innovations will be well-positioned to thrive in an increasingly digitalized world.