Field Service Management with Parts Return Workflow Optimizing Repair Processes and Customer Satisfaction
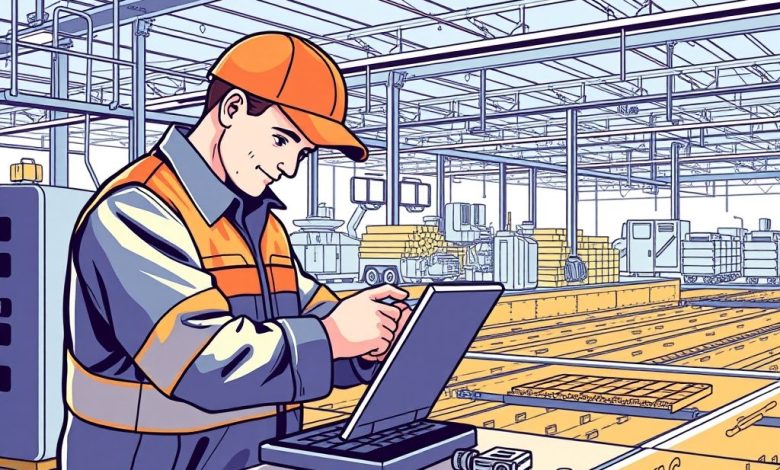
Introduction
Field Service Management (FSM) is a critical component of many businesses, particularly in industries such as HVAC, electrical work, plumbing, and home appliances. It involves managing and coordinating the activities of technicians who provide services directly to customers at their locations. One essential aspect of FSM is the Parts Return Workflow, which plays a crucial role in maintaining efficient operations and customer satisfaction.
The Importance of Field Service Management
Field Service Management encompasses various aspects of service delivery, including scheduling, dispatching, resource allocation, and performance tracking. Effective FSM ensures that:
- Customers receive timely and quality service
- Technicians have the necessary tools and information to complete jobs efficiently
- Business operations run smoothly and profitably
In today’s competitive market, companies must leverage technology to streamline their FSM processes and gain a competitive edge.
Understanding Parts Return Workflow
Parts Return Workflow refers to the process of returning used or defective parts from the field back to the warehouse or distribution center. This workflow is integral to:
- Maintaining inventory accuracy
- Ensuring proper disposal of hazardous materials
- Recovering valuable components for reuse or recycling
- Reducing waste and environmental impact
A well-designed Parts Return Workflow helps organizations optimize their supply chain management and reduce costs associated with part replacement and disposal.
Implementing an Efficient Parts Return Workflow
To establish an effective Parts Return Workflow, consider the following steps:
- Develop clear policies and procedures for part returns
- Assign designated collection points for returned parts
- Establish a system for categorizing and processing returned items
- Create protocols for handling hazardous materials
- Set up a tracking system for returned parts
- Regularly audit and review the return process
By implementing these measures, organizations can ensure smooth operation of their Parts Return Workflow and minimize potential disruptions to their FSM processes.
Technology Integration in Field Service Management
Modern FSM systems often incorporate advanced technologies to enhance efficiency and effectiveness. Some key features include:
- Mobile apps for technicians to access job details and update status
- Real-time scheduling and dispatching capabilities
- GPS tracking for vehicle location monitoring
- Automated reporting and analytics tools
- Integration with CRM systems for improved customer relationship management
These technological advancements enable faster response times, improved resource allocation, and better decision-making throughout the FSM process.
Challenges in Field Service Management
Despite its importance, FSM faces several challenges that can impact its success:
- Scheduling conflicts and last-minute cancellations
- Technicians' availability and skillset mismatches
- Customer communication breakdowns
- Inventory management issues
- Delays in parts procurement or delivery
Addressing these challenges requires proactive planning, robust systems, and continuous improvement efforts.
Best Practices for Field Service Management
To maintain high-quality service delivery and efficient operations, consider the following best practices:
- Invest in employee training and development programs
- Implement a robust quality control process
- Foster strong relationships with suppliers and vendors
- Utilize data analytics to drive informed decision-making
- Regularly assess and improve FSM processes
- Ensure compliance with industry regulations and safety standards
By adhering to these best practices, organizations can consistently deliver exceptional service while optimizing their FSM processes.
Conclusion
Field Service Management with an integrated Parts Return Workflow is crucial for businesses operating in the service sector. By implementing efficient processes, leveraging technology, and addressing common challenges, organizations can significantly improve their operational efficiency and customer satisfaction levels.
As the service industry continues to evolve, it’s essential for businesses to stay ahead of the curve by adopting innovative solutions and continuously refining their FSM strategies. By doing so, they can not only meet but exceed customer expectations, ultimately driving growth and profitability in their respective markets.
Remember, effective Field Service Management is not just about completing tasks; it’s about delivering value to customers through seamless, efficient, and personalized service experiences.