Field Service Management with Real-Time Inventory Stockout Alerts Enhancing Operational Efficiency and Customer Satisfaction
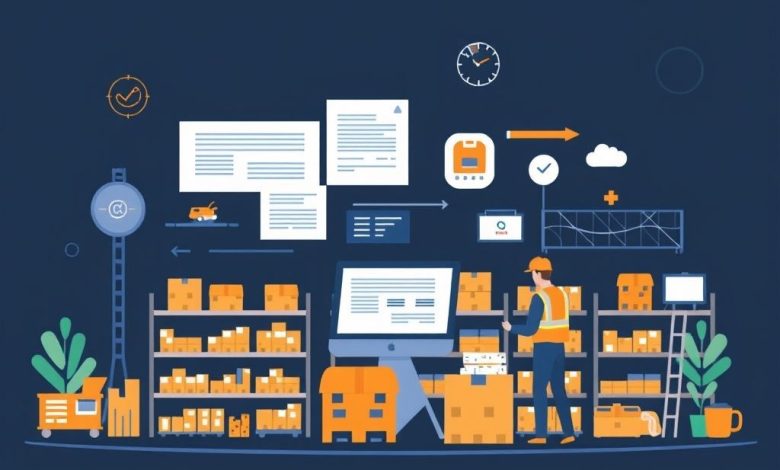
Introduction
Field Service Management (FSM) is a critical component of modern business operations, particularly in industries such as HVAC, electrical work, plumbing, and home maintenance. As companies strive to provide efficient and effective services to customers, FSM systems have evolved to incorporate advanced technologies like real-time inventory tracking and stockout alerts. This article explores the concept of FSM with a focus on real-time inventory management and its impact on preventing stockouts.
The Evolution of Field Service Management
Field Service Management has come a long way since its inception. From paper-based scheduling systems to sophisticated software solutions, the industry has witnessed significant advancements in technology and data analytics. Modern FSM platforms offer features such as:
- Scheduling optimization
- Resource allocation
- Customer relationship management
- Work order management
- Mobile workforce management
These features enable businesses to streamline their operations, improve efficiency, and enhance customer satisfaction.
Challenges in Traditional FSM Systems
Despite the progress made in FSM, traditional systems often face challenges related to inventory management:
- Manual tracking: Many FSM systems rely on manual entry of inventory levels, which can lead to errors and discrepancies.
- Lack of real-time updates: Inventory levels may not be updated in real-time, leading to inaccurate stock assessments.
- Inefficient alert systems: Traditional methods of detecting stockouts often rely on periodic checks rather than continuous monitoring.
- Limited visibility: Supervisors and dispatchers may lack real-time insights into inventory levels across multiple locations.
Real-Time Inventory Management in FSM
Real-time inventory management is a game-changer in the field service industry. It enables businesses to monitor inventory levels in real-time, receive instant notifications when stock levels drop below a certain threshold, and make informed decisions quickly.
Benefits of Real-Time Inventory Management
- Improved accuracy: Eliminates human error in inventory tracking.
- Enhanced decision-making: Allows for quick identification of low-stock items and prompt ordering.
- Increased efficiency: Enables better resource allocation and scheduling based on actual inventory availability.
- Reduced stockouts: Minimizes the risk of running out of essential materials during jobs.
- Better customer experience: Ensures that technicians have the necessary tools and parts to complete jobs efficiently.
Implementing Real-Time Inventory Stockout Alerts
Implementing real-time inventory stockout alerts requires a robust FSM system with integrated inventory management capabilities. Here’s how it typically works:
- Integration with point-of-sale systems: Connects FSM with POS systems to track inventory usage in real-time.
- Automated alerts: Sets up automated notifications when inventory levels fall below predetermined thresholds.
- Mobile app integration: Employs mobile apps used by technicians to update inventory levels instantly.
- Data visualization: Provides clear visual representations of inventory levels and stockout trends.
- Customizable thresholds: Allows administrators to set specific alert triggers based on business needs.
Case Study: XYZ Plumbing Services
XYZ Plumbing Services, a medium-sized plumbing company, implemented a real-time inventory management system with stockout alerts. They experienced significant improvements in their operations:
- Reduced stockouts from 15% to less than 5%
- Decreased average job completion time by 30 minutes
- Improved first-time fix rate from 70% to 85%
- Reduced inventory costs by 20%
Best Practices for Effective Implementation
To ensure successful implementation of real-time inventory stockout alerts, consider the following best practices:
- Conduct thorough training: Ensure all staff members understand the new system and their roles in maintaining accurate inventory records.
- Regular audits: Perform regular audits to verify the accuracy of inventory levels and identify any discrepancies.
- Continuous improvement: Regularly review and refine the alert thresholds and notification protocols based on performance data.
- Integrate with existing systems: Ensure seamless integration with other FSM components and external systems.
- Provide clear communication channels: Establish clear procedures for addressing stockout alerts and resolving issues promptly.
Conclusion
Field Service Management with real-time inventory stockout alerts represents a significant advancement in operational efficiency and customer satisfaction. By leveraging cutting-edge technology, businesses can minimize stockouts, optimize resource allocation, and deliver superior service quality. As the field service industry continues to evolve, embracing real-time inventory management will become increasingly crucial for success in today’s competitive landscape.
By implementing these innovative solutions, field service managers can transform their operations, ensuring that their teams are always equipped with the right tools and materials to deliver exceptional results while minimizing unnecessary delays and disruptions.