Field Service Management for Connected Field Monitoring Pods
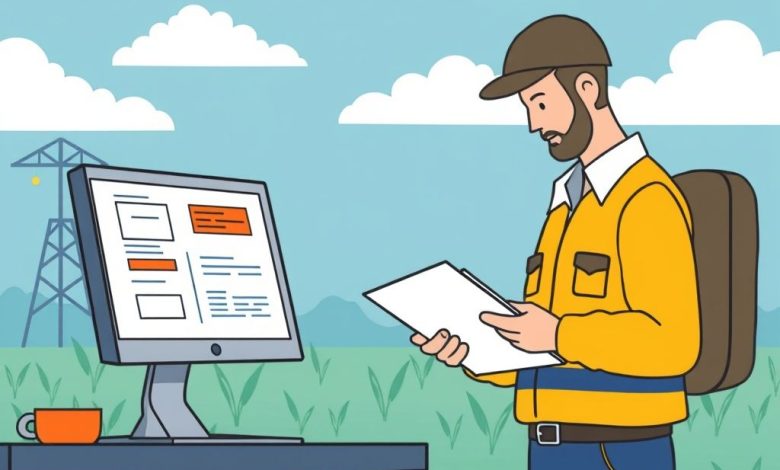
Introduction
In today’s fast-paced world of technology-driven industries, field service management has become increasingly crucial for businesses operating in various sectors. The integration of connected monitoring pods has revolutionized how companies manage their field operations, enhancing efficiency, reducing costs, and improving customer satisfaction. This article will explore the concept of Field Service Management (FSM) for Connected Field Monitoring Pods, its benefits, challenges, and best practices.
What is Field Service Management?
Field Service Management refers to the process of managing and coordinating tasks related to sending technicians or workers to customers’ locations to provide services or support. It involves planning, scheduling, dispatching, and tracking work orders to ensure efficient delivery of services while maximizing resource utilization.
Evolution of Field Service Management
Historically, FSM was primarily based on manual processes and paper-based systems. However, with the advent of digital technologies and the Internet of Things (IoT), FSM has undergone significant transformations. Modern FSM solutions now incorporate advanced features such as real-time data collection, predictive maintenance, and automated scheduling.
Connected Field Monitoring Pods
Connected field monitoring pods are intelligent devices equipped with sensors and communication capabilities that allow them to collect and transmit data from remote locations. These pods can monitor various parameters such as temperature, pressure, vibration, and other environmental factors specific to the industry they serve.
Benefits of Connected Field Monitoring Pods in FSM
- Real-time Data Collection
Connected monitoring pods enable real-time data collection from remote locations. This allows field service managers to make informed decisions quickly, respond to issues promptly, and optimize their operations. - Predictive Maintenance
By continuously monitoring equipment performance, connected pods can predict potential failures before they occur. This proactive approach reduces downtime, extends equipment lifespan, and minimizes unexpected repairs. - Improved Efficiency
With real-time data at their fingertips, field service managers can streamline their operations. They can prioritize jobs based on urgency, allocate resources more effectively, and optimize travel routes. - Enhanced Customer Experience
Connected monitoring pods allow for faster response times and more accurate diagnoses. This leads to improved customer satisfaction and increased loyalty. - Cost Reduction
By identifying and addressing issues proactively, connected monitoring pods help reduce unnecessary site visits, extend equipment life, and minimize repair costs.
Challenges in Implementing Connected Field Monitoring Pods
While the benefits of connected monitoring pods are numerous, there are several challenges that organizations may face when implementing such systems:
- Integration Complexity
Connecting disparate systems and ensuring seamless data flow between the monitoring pods and existing FSM software can be challenging. - Security Concerns
As with any connected device, there are security risks associated with collecting and transmitting sensitive data. Ensuring the integrity and confidentiality of this data is crucial. - Initial Investment Costs
While long-term benefits are substantial, the initial investment in connected monitoring pods and the necessary infrastructure can be significant. - Training and Adoption
Employees may need training to effectively use and interpret data from the monitoring pods, which can be time-consuming and costly. - Connectivity Issues
Remote locations may have limited connectivity, potentially affecting the reliability of data transmission and reception.
Best Practices for Implementing Connected Field Monitoring Pods
To overcome the challenges and maximize the benefits of connected monitoring pods, consider the following best practices:
- Conduct Thorough Needs Assessment
Before implementing connected monitoring pods, conduct a comprehensive assessment of your organization’s specific needs and requirements. - Choose the Right Technology Partners
Select FSM software and hardware providers who offer robust integration capabilities and ongoing support. - Develop Clear Policies and Procedures
Establish clear guidelines for data collection, analysis, and decision-making processes based on real-time data from monitoring pods. - Invest in Employee Training
Provide comprehensive training to ensure employees understand how to interpret data from connected monitoring pods and incorporate this information into their work processes. - Regularly Review and Update Systems
Stay updated with the latest advancements in FSM technology and regularly review and update your systems to ensure they remain effective and efficient.
Conclusion
Field Service Management for Connected Field Monitoring Pods represents a significant leap forward in operational efficiency and customer satisfaction. By leveraging real-time data collection, predictive maintenance, and automated scheduling, organizations can optimize their field operations while reducing costs and improving service quality.
As technology continues to evolve, we can expect even more sophisticated solutions to emerge. However, it’s crucial for businesses to stay informed about the latest developments and adapt their strategies accordingly. By embracing connected field monitoring pods and implementing best practices, field service managers can position their organizations at the forefront of innovation in the industry.
Remember, the key to success lies not just in adopting new technologies, but in understanding how to effectively integrate them into existing workflows and leverage their full potential to drive business growth and improvement.