Integrating Field Service Management with Inventory Management A Guide for Small Businesses
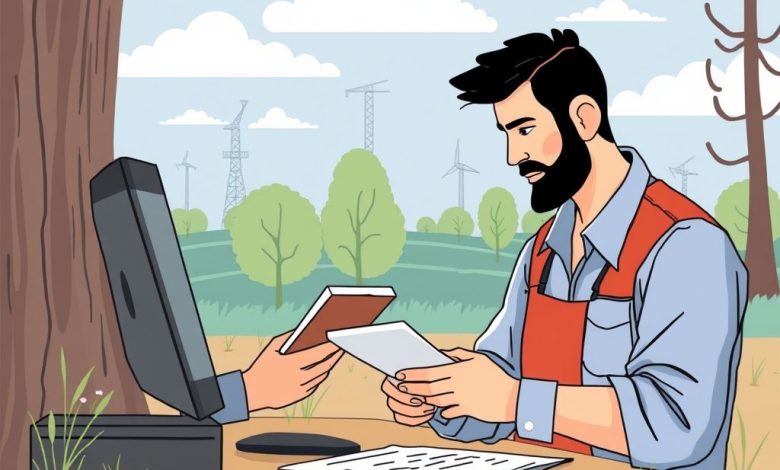
Introduction
Field Service Management (FSM) and inventory management are two critical components of modern business operations. While they have traditionally been managed separately, integrating them can lead to significant improvements in efficiency, cost reduction, and customer satisfaction. This article explores the benefits and challenges of integrating FSM with inventory management, providing insights for field service managers looking to optimize their operations.
The Importance of FSM and Inventory Management
Field Service Management refers to the processes and systems used to manage and coordinate work orders, schedules, and resources for field-based services. It encompasses various aspects such as scheduling, dispatching, resource allocation, and job execution. On the other hand, inventory management involves the tracking and control of goods and materials within a supply chain.
Both FSM and inventory management play crucial roles in maintaining operational efficiency and ensuring customer satisfaction. However, they often operate independently, which can lead to inefficiencies and potential conflicts. For instance, FSM might schedule jobs without considering available inventory, while inventory management might not account for real-time field requirements.
Benefits of Integrating FSM with Inventory Management
Integrating FSM with inventory management offers numerous advantages:
- Improved Resource Allocation
By linking FSM and inventory management systems, businesses can ensure that the right resources are allocated to the right jobs at the right time. This leads to better utilization of equipment, vehicles, and personnel. - Enhanced Visibility and Real-Time Tracking
An integrated system provides a unified view of both FSM and inventory data. This allows for real-time tracking of inventory levels, job status, and resource availability, enabling more informed decision-making. - Optimized Scheduling
With accurate inventory information, FSM systems can generate more realistic and efficient schedules. This reduces the likelihood of last-minute cancellations due to missing parts or equipment. - Cost Reduction
Integrated systems help minimize unnecessary trips, reduce stockouts, and prevent overstocking. These savings can be substantial when applied across large fleets and extensive networks. - Improved Customer Satisfaction
By ensuring that all necessary parts and equipment are available when needed, integrated FSM and inventory management contribute to faster job completion times and higher quality service delivery. - Data-Driven Decision Making
Access to combined FSM and inventory data enables businesses to make more informed decisions regarding inventory levels, pricing strategies, and resource allocation. - Streamlined Processes
An integrated system eliminates the need for manual data entry and reduces errors associated with separate systems. This leads to increased productivity and reduced administrative burdens.
Challenges in Implementing FSM-Inventory Integration
While the benefits of integration are clear, implementing such a system presents several challenges:
- System Compatibility
Ensuring that existing FSM and inventory management systems are compatible with each other can be a significant hurdle. Some legacy systems may require major upgrades or replacements. - Data Standardization
Different systems may use varying data formats and structures. Standardizing this data to create a seamless interface between FSM and inventory management requires careful planning and implementation. - Change Management
Integrating new systems often requires changes in workflows and processes. This can be challenging, especially in larger organizations with established procedures. - Training and Adoption
Employees need to be trained to effectively utilize the new integrated system. Resistance to change can sometimes hinder the adoption process. - Security and Privacy Concerns
Combining sensitive data from both FSM and inventory management systems raises security and privacy considerations. Ensuring the integrity and confidentiality of this data is crucial.
Implementation Strategies
To overcome the challenges and successfully integrate FSM with inventory management, consider the following strategies:
- Start Small
Begin with a pilot project involving a limited number of users or locations. This allows for testing and refinement before full-scale implementation. - Choose Compatible Solutions
When selecting new systems, prioritize compatibility with existing infrastructure where possible. Consider cloud-based solutions that offer better scalability and easier integration. - Invest in Proper Training
Provide comprehensive training programs for all stakeholders involved in the new system. This includes both technical staff responsible for implementation and end-users who will interact with the system daily. - Leverage Existing Data
Utilize existing data from both FSM and inventory management systems to populate the new integrated platform. This ensures continuity and minimizes data loss during transition. - Monitor and Adjust
Implement a robust monitoring system to track key performance indicators (KPIs) before and after integration. Use this data to identify areas for improvement and make necessary adjustments.
Case Study: XYZ Corporation
XYZ Corporation, a leading provider of HVAC services, implemented an integrated FSM-inventory management solution. Prior to integration, their FSM system was prone to scheduling conflicts due to inaccurate inventory information. After implementing the new system, they noticed:
- A 25% reduction in scheduling conflicts
- A 15% decrease in average job duration
- A 10% increase in first-time fix rates
- A 12% reduction in overall operational costs
These results demonstrate the tangible benefits of FSM-inventory integration and serve as a compelling case study for similar implementations.
Conclusion
Integrating Field Service Management with inventory management is a powerful strategy for optimizing business operations. By combining the strengths of both systems, organizations can achieve improved resource allocation, enhanced visibility, optimized scheduling, and ultimately, better customer satisfaction.
As field service managers navigate the complexities of modern service delivery, embracing integrated FSM-inventory management solutions can provide a competitive edge. While challenges exist, the benefits far outweigh the costs of implementation. As technology continues to evolve, we can expect even more sophisticated solutions to emerge, further streamlining operations and driving innovation in the field service industry.
By investing in FSM-inventory integration, businesses position themselves for long-term success in an increasingly competitive market where operational efficiency and customer satisfaction are paramount.