Harnessing the Power of Field Service Management Efficient Wind Energy Maintenance Strategies
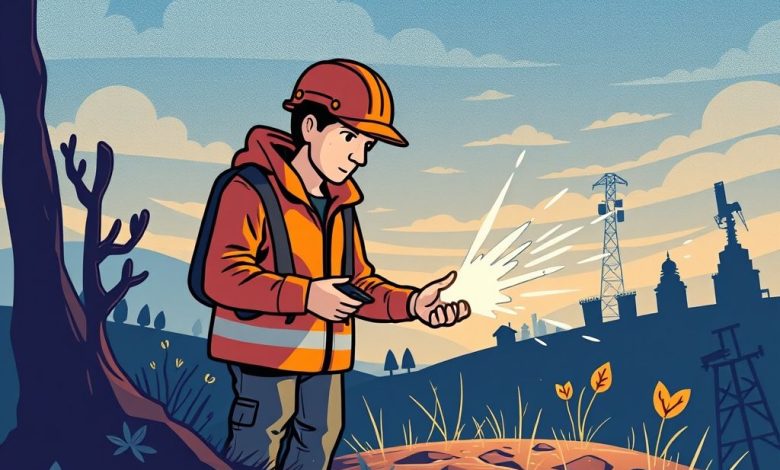
Introduction
Wind energy maintenance is crucial for ensuring the efficiency and longevity of wind farms. As the renewable energy sector continues to grow, the demand for skilled technicians and effective field service management strategies has increased significantly. This article explores the importance of field service management in wind energy maintenance, highlighting its key components, challenges, and best practices.
- The Role of Field Service Management in Wind Energy Maintenance
- Challenges in Field Service Management for Wind Energy Maintenance
- Best Practices for Effective Field Service Management in Wind Energy Maintenance
- Invest in Cloud-Based FSM Software
- Implement Predictive Maintenance Strategies
- Foster a Culture of Continuous Improvement
- Develop Comprehensive Training Programs
- Conclusion
The Role of Field Service Management in Wind Energy Maintenance
Field service management (FSM) refers to the processes and systems used to manage and coordinate field-based work activities. In the context of wind energy maintenance, FSM plays a critical role in optimizing operations and improving overall performance. Some of the key aspects of FSM in this industry include:
Work Order Management
Effective work order management is essential for efficient wind farm maintenance. It involves creating, assigning, and tracking tasks related to routine inspections, repairs, and upgrades. A robust FSM system helps ensure that all necessary work orders are completed on time and within budget.
• Implementing a centralized database for storing and managing work orders
• Assigning tasks based on technician expertise and location
• Setting realistic deadlines and allocating appropriate resources
Technician Scheduling
Proper scheduling of technicians is vital for maintaining optimal wind farm performance. FSM systems help optimize routes and allocate tasks efficiently, considering factors such as:
• Technicians’ skill levels and certifications
• Equipment availability and location
• Weather conditions and potential safety hazards
Inventory Management
Accurate inventory management is crucial for wind energy maintenance. FSM systems assist in tracking spare parts, tools, and equipment, ensuring that everything needed for each job is readily available.
• Implementing a barcode scanning system for quick inventory checks
• Setting reorder points for frequently used items
• Maintaining detailed records of part usage and replacements
Customer Relationship Management
Building strong relationships with wind farm owners and operators is essential for long-term success. FSM systems help streamline communication, track customer feedback, and provide insights into satisfaction levels.
• Implementing a customer portal for easy access to job status updates
• Conducting regular surveys to gauge customer satisfaction
• Analyzing data to identify areas for improvement
Challenges in Field Service Management for Wind Energy Maintenance
Despite the benefits of FSM, several challenges exist in implementing and maintaining effective field service management systems for wind energy maintenance:
Remote Locations
Many wind farms are located in remote areas, making it challenging to maintain reliable connectivity and access to resources.
• Implementing satellite-based communication systems
• Partnering with local suppliers for emergency parts delivery
• Training technicians on self-reliance techniques
Variable Weather Conditions
Harsh weather conditions common in wind farm locations can impact both equipment reliability and technician safety.
• Developing weather-resistant equipment designs
• Creating contingency plans for extreme weather scenarios
• Providing regular safety training for technicians
High-Tech Equipment Complexity
Modern wind turbines feature sophisticated control systems and complex mechanical components, requiring specialized knowledge to maintain effectively.
• Investing in ongoing training programs for technicians
• Collaborating with manufacturers for technical support
• Implementing virtual reality training simulations
Best Practices for Effective Field Service Management in Wind Energy Maintenance
To overcome the challenges and maximize the benefits of FSM in wind energy maintenance, consider the following best practices:
Invest in Cloud-Based FSM Software
Cloud-based FSM software offers real-time visibility, scalability, and accessibility from anywhere with an internet connection.
• Look for solutions specifically designed for renewable energy industries
• Ensure the system integrates with existing ERP and CRM platforms
• Consider mobile apps for on-site data capture and reporting
Implement Predictive Maintenance Strategies
By leveraging data analytics and machine learning algorithms, predictive maintenance can help prevent unexpected downtime and reduce maintenance costs.
• Integrating IoT sensors to collect real-time equipment data
• Establishing baseline performance metrics for each turbine
• Automating alerts for potential issues before they occur
Foster a Culture of Continuous Improvement
Encourage open communication among technicians, supervisors, and customers to continuously refine and improve FSM processes.
• Conducting regular team meetings to discuss challenges and successes
• Implementing a suggestion box system for innovative ideas
• Celebrating milestones and achievements to boost morale
Develop Comprehensive Training Programs
Invest in ongoing training and development to keep technicians up-to-date with the latest technologies and best practices.
• Offering manufacturer-specific training courses
• Encouraging cross-training between different types of equipment
• Providing certification programs for specialized skills
Conclusion
Field service management plays a critical role in ensuring the smooth operation and longevity of wind energy assets. By implementing robust FSM systems, investing in cutting-edge technology, and fostering a culture of continuous improvement, organizations can optimize their maintenance processes and contribute to the growth of the renewable energy sector. As the industry continues to evolve, staying ahead of technological advancements and adapting to changing environmental conditions will remain essential for success in wind energy maintenance.