Field Service Management Strategies for Minimizing Equipment Downtime
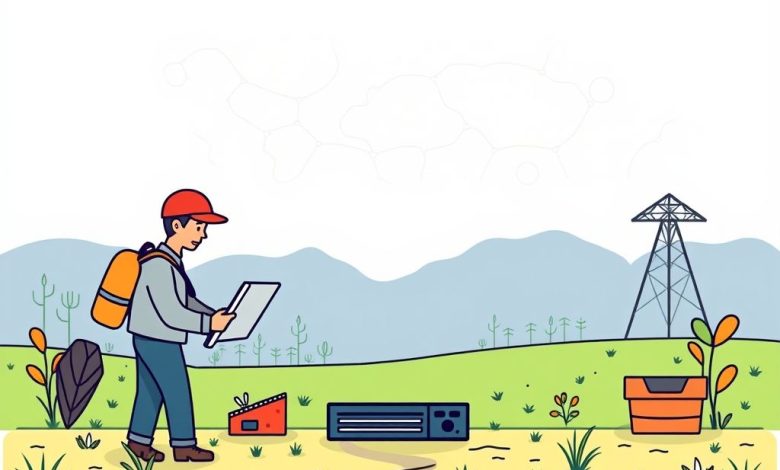
Introduction
Field Service Management (FSM) is a critical component of modern business operations, particularly in industries where equipment maintenance and repair are essential. In today’s fast-paced world, downtime can have severe consequences, including lost revenue, damaged customer relationships, and decreased competitiveness. This article explores the importance of effective Field Service Management in reducing downtime and improving overall operational efficiency.
The Impact of Downtime
Downtime can occur due to various factors such as equipment failure, scheduled maintenance, or unexpected events. Regardless of the cause, it can significantly impact a company’s bottom line and reputation. Some key statistics on downtime include:
- According to a study by Gartner, IT downtime costs businesses approximately $700 per minute.
- A survey by IT Brand Pulse found that 60% of organizations experience IT outages lasting more than four hours annually.
- In the manufacturing sector, unplanned downtime can result in losses ranging from 20% to 40% of annual production capacity.
These figures underscore the need for robust Field Service Management strategies to minimize downtime and ensure continuous operation.
Key Components of Effective Field Service Management
To reduce downtime effectively, organizations must implement a comprehensive FSM strategy that includes several crucial elements:
Real-time Scheduling and Dispatching
Real-time scheduling and dispatching systems allow for efficient allocation of resources based on current job requirements and technician availability. These systems consider factors such as:
- Technician skill sets and location
- Job urgency and priority
- Equipment type and model
- Historical performance data
By leveraging real-time data, organizations can optimize their resource allocation, ensuring that the right technician arrives at the right place at the right time.
Mobile Workforce Management
Mobile workforce management solutions provide technicians with the tools needed to perform their jobs efficiently. These typically include:
- Mobile apps for accessing job details, inventory, and customer information
- GPS tracking for real-time location monitoring
- Digital signature capture for proof of work completion
Mobile solutions enable technicians to stay connected and productive while on-site, reducing response times and improving first-time fix rates.
Predictive Maintenance
Predictive maintenance uses advanced analytics and machine learning algorithms to forecast potential equipment failures before they occur. This proactive approach allows organizations to schedule maintenance during off-peak hours, minimizing disruption to operations.
Key aspects of predictive maintenance include:
- Sensor integration to collect real-time data from equipment
- Advanced analytics for identifying patterns and anomalies
- Automated alerts for impending failures
By implementing predictive maintenance, organizations can significantly reduce unexpected downtime and extend equipment lifespan.
Inventory Management
Proper inventory management is crucial for efficient field service operations. This includes:
- Real-time tracking of parts and equipment
- Automated reordering based on usage patterns
- Integration with scheduling systems to ensure necessary items are available when needed
Effective inventory management helps reduce travel times, minimize stockouts, and improve overall operational efficiency.
Case Study: Implementing FSM at XYZ Corporation
XYZ Corporation, a leading manufacturer of industrial machinery, faced significant challenges with downtime and customer satisfaction. They implemented a comprehensive Field Service Management solution that included real-time scheduling, mobile workforce management, predictive maintenance, and advanced analytics.
The results were impressive:
- Reduced average response time by 30%
- Increased first-time fix rate from 70% to 85%
- Decreased scheduled downtime by 25%
- Improved customer satisfaction scores by 40%
These outcomes demonstrate the tangible benefits of implementing a robust FSM strategy.
Challenges in Implementing FSM
While the benefits of FSM are clear, organizations may face several challenges when implementing such solutions:
- Initial investment costs can be substantial
- Integrating new systems with existing infrastructure can be complex
- Changing technician behavior and adopting new workflows requires training and buy-in
- Ensuring data privacy and security, particularly when dealing with sensitive customer information
Addressing these challenges requires careful planning, change management strategies, and ongoing support from leadership.
Conclusion
Field Service Management is a critical component of modern business operations, especially in industries where equipment maintenance and repair are essential. By implementing effective FSM strategies, organizations can significantly reduce downtime, improve operational efficiency, and enhance customer satisfaction.
As technology continues to evolve, we can expect further advancements in FSM tools and techniques. Organizations must stay ahead of these trends to remain competitive in today’s fast-paced business environment.
By leveraging the power of Field Service Management, businesses can transform their approach to equipment maintenance and repair, ultimately driving growth, profitability, and long-term success.