Field Service Management with Service Chain Automation Optimizing Operations Through Integrated Technologies
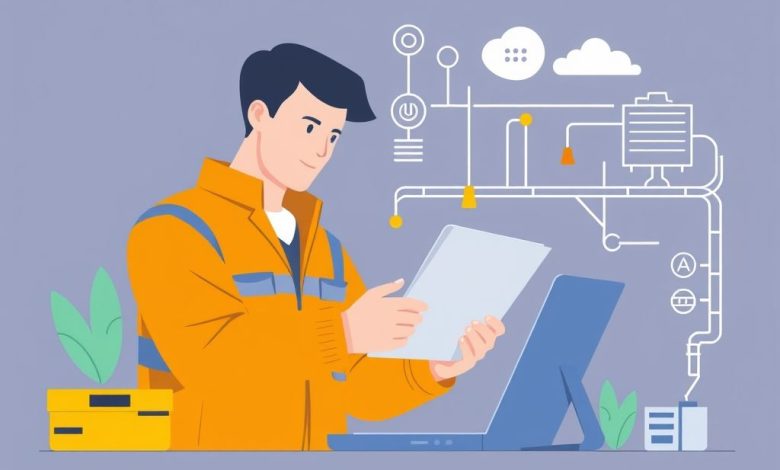
Field Service Management with Service Chain Automation
Introduction
Field service management (FSM) refers to the processes and systems used to manage and coordinate work orders, schedules, and resources for field-based services. With the advent of technology, particularly automation and Internet of Things (IoT), FSM has evolved significantly. One such advancement is service chain automation, which aims to streamline and optimize the entire service delivery process from start to finish.
Service chain automation involves integrating various technologies and data sources to create a seamless, efficient, and customer-centric approach to field service operations. This article will explore the concept of field service management with service chain automation, its benefits, challenges, and best practices for implementation.
The Evolution of Field Service Management
Traditionally, field service management relied heavily on manual processes and paper-based systems. Technicians would receive work orders through phone calls or emails, travel to job sites, complete tasks, and then return to the office to update records. This method was time-consuming, prone to errors, and lacked real-time visibility into service activities.
The introduction of computerized maintenance management systems (CMMS) marked the beginning of digital transformation in FSM. These early systems allowed for better scheduling and resource allocation but still had limitations in terms of mobility and real-time communication.
The Rise of Service Chain Automation
Service chain automation represents the next step in the evolution of FSM. It combines advanced technologies like artificial intelligence, machine learning, and IoT sensors to create a more intelligent and responsive service ecosystem.
Key components of service chain automation include:
- Predictive analytics: Using historical data and real-time inputs to forecast equipment failures and schedule preventive maintenance.
- Automated scheduling: Optimizing routes and assigning jobs based on technician skills, location, and availability.
- Real-time tracking: Providing live updates on technician locations and job progress.
- Augmented reality: Enhancing technician capabilities with virtual instructions and remote assistance.
- Customer self-service portals: Allowing customers to schedule appointments and access service history online.
Benefits of Service Chain Automation
Implementing service chain automation can bring numerous advantages to field service organizations:
- Improved efficiency: By automating routine tasks and optimizing schedules, technicians can complete more jobs in less time.
- Enhanced customer experience: Real-time updates and transparent communication lead to higher customer satisfaction.
- Reduced costs: Lower operational expenses due to optimized routing and reduced paperwork.
- Increased accuracy: Minimized human error through automated data collection and processing.
- Better decision-making: Access to real-time data enables more informed strategic decisions.
- Competitive advantage: Organizations that adopt advanced technologies stand out in their industry.
Challenges in Implementing Service Chain Automation
While the benefits of service chain automation are significant, there are several challenges to consider when implementing this technology:
- Initial investment: Adopting advanced technologies requires substantial upfront costs for hardware, software, and training.
- Data integration: Combining data from various sources and ensuring interoperability between different systems can be complex.
- Change management: Employees may resist adopting new tools and workflows, requiring careful training and support.
- Cybersecurity concerns: Connected devices and cloud-based systems increase the risk of data breaches and cyber attacks.
- Standardization: Ensuring consistency across different regions or divisions can be challenging.
Best Practices for Implementation
To successfully implement service chain automation, consider the following best practices:
- Start small: Begin with a pilot program or specific department before rolling out organization-wide.
- Involve stakeholders: Engage employees at all levels in the implementation process to ensure buy-in.
- Provide comprehensive training: Offer thorough training on new systems and processes to minimize disruption.
- Focus on user experience: Design intuitive interfaces that make it easy for technicians to adopt new tools.
- Regularly update and maintain: Keep software and hardware up-to-date to leverage the latest features and improvements.
- Measure and analyze: Continuously monitor key performance indicators (KPIs) to assess the impact of automation.
Conclusion
Field service management with service chain automation represents a significant leap forward in how organizations deliver field-based services. By leveraging advanced technologies like IoT sensors, AI, and machine learning, FSM can become more efficient, responsive, and customer-centric.
While there are challenges to overcome, the benefits of improved efficiency, enhanced customer satisfaction, and competitive advantage make the investment worthwhile. As technology continues to evolve, we can expect even more innovative solutions to emerge in the field of field service management.
For field service managers looking to stay ahead in their industry, embracing service chain automation should be a priority. By doing so, they can transform their operations, improve their bottom line, and provide better value to their customers.