Field Service Management with Visual Work Instructions Enhancing Efficiency and Quality in Multi-Site Operations
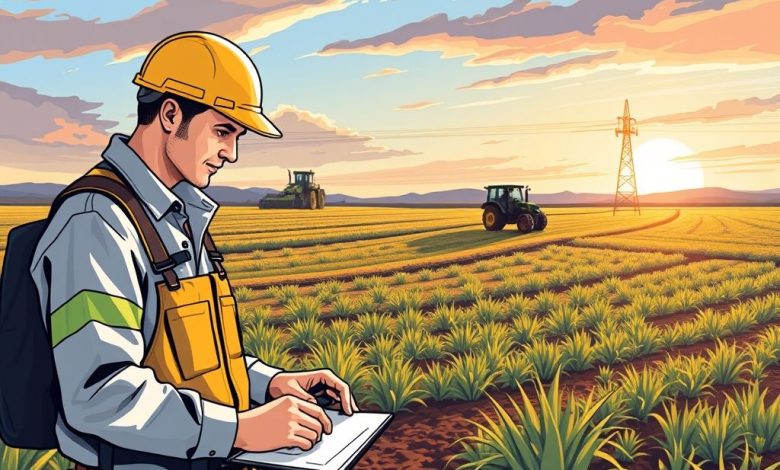
Field Service Management with Visual Work Instructions: Enhancing Efficiency and Quality
Introduction
Field service management (FSM) has become increasingly crucial in today’s fast-paced business landscape. As companies strive to deliver exceptional customer experiences while managing complex operations, FSM systems have evolved to meet these demands. One innovative approach that has gained significant attention in recent years is the integration of visual work instructions into field service management processes. This article explores the concept of FSM with visual work instructions, examining its benefits, implementation strategies, and impact on field service operations.
Understanding Field Service Management
Field service management refers to the practices and technologies used by organizations to manage and coordinate tasks performed outside of a traditional office setting. These tasks typically involve sending technicians or service representatives to customers’ locations to perform maintenance, repairs, or installations. Effective FSM ensures that service requests are handled efficiently, resources are allocated optimally, and customer satisfaction is maximized.
The Role of Visual Work Instructions in FSM
Visual work instructions are detailed, step-by-step guides that utilize images, videos, and other visual elements to communicate complex procedures. In the context of FSM, these instructions aim to simplify and standardize the execution of service tasks. By providing clear, easily understandable guidance, visual work instructions help reduce errors, improve efficiency, and enhance overall quality of service delivery.
Benefits of Implementing Visual Work Instructions
- Improved Accuracy: Visual instructions reduce misinterpretation of written procedures, leading to fewer errors and improved overall quality of work.
- Enhanced Efficiency: By providing clear, concise guidance, technicians can complete tasks more quickly, reducing downtime and improving customer satisfaction.
- Increased Training Effectiveness: Visual instructions serve as valuable training aids, allowing new technicians to learn complex procedures more easily.
- Better Customer Experience: With reduced errors and faster completion times, customers receive higher-quality service, leading to increased loyalty and positive reviews.
- Cost Savings: Improved efficiency and accuracy can lead to significant cost reductions in labor and materials.
Implementation Strategies
Implementing visual work instructions in FSM requires careful planning and execution. Here are some key considerations:
- Develop Comprehensive Instruction Sets: Create detailed, step-by-step guides for each service procedure, incorporating both textual and visual elements.
- Utilize Modern Technology: Leverage mobile devices, augmented reality (AR) glasses, and other digital tools to deliver visual instructions in real-time during field operations.
- Integrate with Existing Systems: Ensure seamless integration between visual instruction platforms and existing FSM software to maintain operational continuity.
- Provide Regular Updates: Keep instructions current with any changes in procedures or equipment specifications.
- Offer Feedback Mechanisms: Allow technicians to provide input on the effectiveness of visual instructions to continuously improve the system.
Case Studies and Best Practices
Several companies have successfully implemented visual work instructions in their FSM processes, resulting in significant improvements in efficiency and quality. For example:
- A major appliance manufacturer reduced installation errors by 75% after implementing AR-guided visual instructions for technicians.
- An HVAC company reported a 30% decrease in service call times after adopting visual work instructions for routine maintenance procedures.
Best practices for implementing visual work instructions include:
- Conduct thorough needs assessments to identify areas where visual instructions would be most beneficial.
- Involve technicians in the development process to ensure instructions meet real-world needs.
- Provide regular training sessions to familiarize technicians with new instruction systems.
- Monitor key performance indicators (KPIs) such as error rates and completion times to measure the impact of visual instructions.
Challenges and Limitations
While visual work instructions offer numerous benefits, they also present some challenges:
- Initial Investment: Implementing comprehensive visual instruction systems requires significant upfront investment in technology and content creation.
- Training Requirements: Technicians may require time to adapt to new instruction formats and learn how to effectively utilize visual tools.
- Connectivity Issues: In areas with poor internet connectivity, real-time access to visual instructions can be problematic.
- Equipment Compatibility: Ensuring all necessary equipment is compatible with chosen visual instruction delivery platforms can be challenging.
Conclusion
Field service management with visual work instructions represents a powerful approach to enhancing operational efficiency, quality, and customer satisfaction. By leveraging modern technologies and innovative instructional methods, companies can streamline their FSM processes, reduce errors, and improve overall service delivery. As the field service industry continues to evolve, the integration of visual work instructions is likely to play an increasingly crucial role in shaping the future of FSM practices.
For field service managers looking to implement or enhance their visual work instruction strategies, careful planning, ongoing evaluation, and a commitment to continuous improvement are essential. By embracing this technology-driven approach to FSM, organizations can position themselves at the forefront of efficient, high-quality service delivery in today’s competitive business landscape.