Field Service Management with Preventive Cadence Forecasting Optimizing High-Volume Preventive Visits
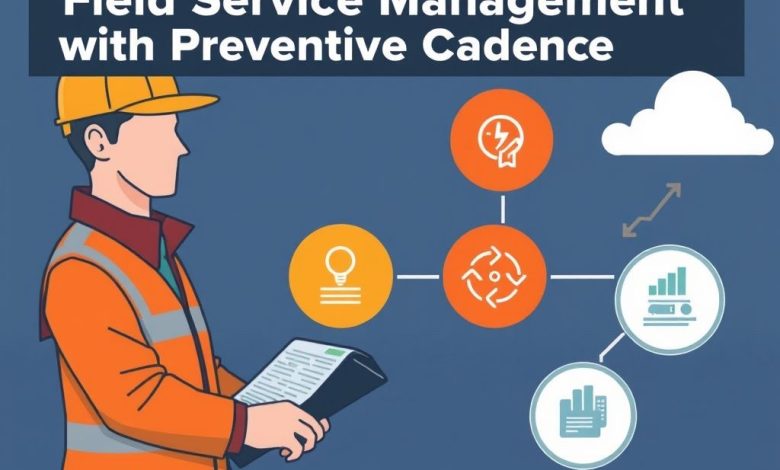
Field Service Management with Preventive Cadence Forecasting
- Introduction
- Understanding Preventive Cadence Forecasting
- Benefits of Implementing Preventive Cadence Forecasting
- Improved Schedule Accuracy
- Enhanced Customer Satisfaction
- Cost Reduction
- Increased Operational Efficiency
- Implementation Strategies for Preventive Cadence Forecasting
- Invest in Advanced Analytics Tools
- Develop a Comprehensive Data Strategy
- Train Technicians and Support Staff
- Integrate with Existing Systems
- Start Small and Scale Up
- Best Practices for Successful Adoption
- Regular Model Updates
- Balance Proactivity and Flexibility
- Focus on High-Impact Equipment
- Measure and Communicate ROI
- Conclusion
Introduction
Field service management (FSM) is a critical component of many industries, including HVAC, electrical work, plumbing, and home maintenance services. It involves managing and coordinating the activities of technicians who provide on-site services to customers. With the increasing demand for efficient and cost-effective service delivery, FSM companies are turning to advanced technologies like preventive cadence forecasting to optimize their operations.
Preventive cadence forecasting is a data-driven approach that predicts when equipment failures are likely to occur based on historical patterns and current conditions. This technique allows FSM companies to schedule maintenance visits proactively, reducing unexpected breakdowns and improving customer satisfaction.
In this article, we will explore the concept of preventive cadence forecasting in field service management, its benefits, implementation strategies, and best practices for successful adoption.
Understanding Preventive Cadence Forecasting
Preventive cadence forecasting is a predictive analytics technique used in FSM to anticipate potential equipment failures before they occur. The process involves analyzing historical data on equipment performance, failure rates, and environmental factors to identify patterns and trends.
Key components of preventive cadence forecasting include:
- Data collection: Gathering information on equipment usage, performance metrics, and failure events.
- Pattern analysis: Identifying recurring patterns in equipment behavior and failure rates.
- Predictive modeling: Developing algorithms to forecast future equipment failures based on identified patterns.
- Risk assessment: Evaluating the likelihood and potential impact of predicted failures.
By leveraging preventive cadence forecasting, FSM companies can create more accurate schedules, reduce unexpected downtime, and improve overall operational efficiency.
Benefits of Implementing Preventive Cadence Forecasting
The integration of preventive cadence forecasting into field service management offers several advantages:
Improved Schedule Accuracy
One of the primary benefits of preventive cadence forecasting is improved scheduling accuracy. By predicting equipment failures before they happen, FSM companies can create more realistic and reliable schedules for their technicians.
This leads to better resource allocation, reduced overtime costs, and increased job completion rates. According to a study by Field Service News, organizations implementing predictive maintenance saw a 25% improvement in schedule adherence compared to traditional reactive approaches.
Enhanced Customer Satisfaction
Proactive maintenance scheduling through preventive cadence forecasting contributes significantly to enhanced customer satisfaction. When equipment issues are addressed before they cause disruptions, customers experience fewer interruptions and enjoy longer periods of uninterrupted service.
A survey conducted by PTC found that 70% of customers reported higher satisfaction levels when their service providers used predictive maintenance techniques. This translates to improved brand reputation and increased customer loyalty for FSM companies.
Cost Reduction
Implementing preventive cadence forecasting can lead to substantial cost savings for FSM companies. By scheduling maintenance visits proactively, companies can avoid the high costs associated with emergency repairs and unexpected downtime.
According to a report by ResearchAndMarkets.com, organizations adopting predictive maintenance strategies could potentially save up to 30% on maintenance costs compared to traditional reactive approaches.
Increased Operational Efficiency
Preventive cadence forecasting enables FSM companies to streamline their operations and maximize technician productivity. By identifying potential issues before they become major problems, companies can allocate resources more effectively and minimize unnecessary travel time.
A case study by Schneider Electric revealed that their predictive maintenance program resulted in a 20% reduction in truck rolls and a 15% increase in first-time fix rates.
Implementation Strategies for Preventive Cadence Forecasting
To successfully implement preventive cadence forecasting in field service management, consider the following strategies:
Invest in Advanced Analytics Tools
FSM companies need robust analytics platforms capable of processing large volumes of data from various sources. Look for solutions that offer machine learning capabilities, real-time data processing, and predictive modeling features.
Consider integrating IoT sensors and smart devices to collect real-time equipment data, which can be fed into the analytics platform for continuous improvement of predictive models.
Develop a Comprehensive Data Strategy
A successful preventive cadence forecasting system relies on high-quality, consistent data. Establish clear data collection protocols and ensure all relevant information is captured accurately and consistently.
This may involve standardizing data formats across different systems, implementing data validation checks, and creating processes for regular data cleansing and updating.
Train Technicians and Support Staff
To fully leverage the benefits of preventive cadence forecasting, it’s crucial to educate technicians and support staff on how to interpret and act upon predictive insights.
Develop training programs that cover topics such as understanding predictive models, interpreting risk scores, and adjusting schedules based on forecasted outcomes.
Integrate with Existing Systems
Ensure seamless integration between the preventive cadence forecasting system and other FSM software, such as CRM, scheduling, and inventory management tools. This will enable end-to-end automation of workflows and prevent manual errors.
Consider implementing APIs or middleware solutions to facilitate smooth data exchange between different systems while maintaining data integrity and security.
Start Small and Scale Up
Begin with a pilot project focusing on a specific subset of equipment or a particular region. As the system matures and proves its value, gradually expand its application to other areas of the business.
Monitor key performance indicators (KPIs) closely during the rollout phase to identify any challenges and make necessary adjustments.
Best Practices for Successful Adoption
To ensure the successful adoption of preventive cadence forecasting in field service management, consider the following best practices:
Regular Model Updates
Maintain and update predictive models regularly to account for changes in equipment behavior, environmental factors, and new data points. This ensures the continued accuracy and relevance of forecasts.
Schedule periodic reviews of model performance and adjust parameters as needed to maintain optimal results.
Balance Proactivity and Flexibility
While proactive scheduling is beneficial, it’s essential to maintain flexibility in the system. Allow for last-minute adjustments based on changing circumstances or unexpected events.
Implement a feedback loop where actual outcomes are compared against predictions, enabling continuous improvement of the forecasting model.
Focus on High-Impact Equipment
Prioritize preventive cadence forecasting for equipment that has significant impacts on business operations or customer satisfaction. This approach maximizes the return on investment in predictive analytics technology.
Identify high-risk assets and focus initial efforts on optimizing maintenance schedules for these items.
Measure and Communicate ROI
Establish clear KPIs to measure the effectiveness of preventive cadence forecasting. Track metrics such as schedule adherence, first-time fix rates, and overall customer satisfaction.
Regularly communicate the tangible benefits of the new system to stakeholders, including technicians, dispatchers, and senior management. This helps build buy-in and encourages ongoing support for the initiative.
Conclusion
Field service management with preventive cadence forecasting represents a significant leap forward in operational efficiency and customer satisfaction. By leveraging advanced analytics and predictive modeling techniques, FSM companies can anticipate equipment failures before they occur, optimize scheduling, and reduce costs.
While implementing preventive cadence forecasting requires investment in technology and training, the long-term benefits far outweigh the initial costs. As this technology continues to evolve, we can expect even more sophisticated applications in field service management, further enhancing the ability of service providers to deliver exceptional value to their customers.
For field service managers looking to stay competitive in today’s fast-paced service economy, embracing preventive cadence forecasting is not just a recommendation—it’s a necessity for success in the years ahead.