Field Service Management with Plug-and-Play IoT Kits Revolutionizing Equipment Maintenance
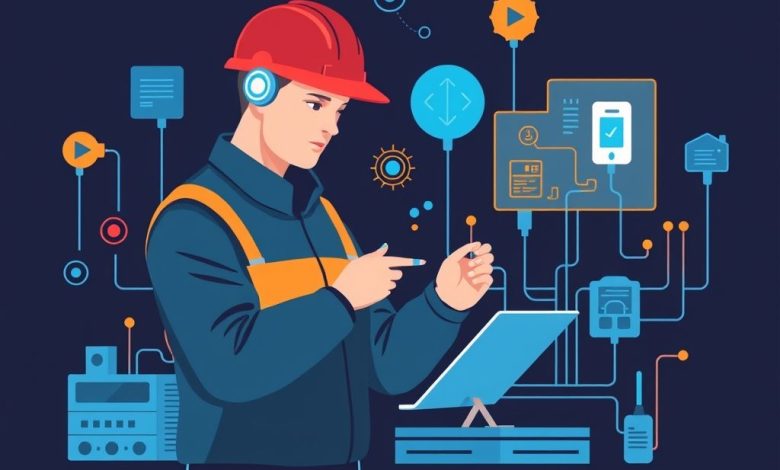
Introduction
Field Service Management (FSM) is a critical component of modern business operations, particularly in industries such as manufacturing, healthcare, and telecommunications. Traditionally, FSM relied heavily on manual processes and limited technology integration. However, the advent of Internet of Things (IoT) devices and plug-and-play solutions has revolutionized how field service teams operate. This article explores the concept of Field Service Management with Plug-and-Play IoT Kits, examining their benefits, implementation strategies, and future trends.
- The Evolution of Field Service Management
- Plug-and-Play IoT Kits in Field Service Management
- Implementation Strategies for Plug-and-Play IoT Kits
- Hardware Selection and Deployment
- Software Integration and Data Management
- Change Management and Training
- Case Studies and Success Stories
- Example 1: HVAC Company Reduces Service Calls by 30%
- Example 2: Manufacturing Plant Optimizes Equipment Maintenance
- Challenges and Limitations
- Future Trends in Field Service Management with IoT
- Conclusion
The Evolution of Field Service Management
Field Service Management has undergone significant transformations since its inception. From paper-based scheduling systems to advanced software solutions, the industry has continuously adapted to technological advancements. The incorporation of IoT devices and plug-and-play kits represents the latest evolution in FSM technology.
Traditional Field Service Management Challenges
Before the introduction of IoT-based solutions, field service teams faced numerous challenges:
- Inefficient scheduling and resource allocation
- Limited real-time data availability
- Manual data entry and reporting
- Difficulty in tracking equipment condition
- High operational costs due to unnecessary site visits
These challenges often resulted in delayed response times, increased costs, and reduced customer satisfaction.
Plug-and-Play IoT Kits in Field Service Management
Plug-and-play IoT kits have emerged as a game-changer in the field service management landscape. These kits typically consist of:
- Sensors and monitoring devices
- Data transmission modules
- User-friendly interfaces
- Integration capabilities with existing FSM software
Benefits of Plug-and-Play IoT Kits
The adoption of plug-and-play IoT kits offers numerous advantages to field service organizations:
- Real-time equipment monitoring and predictive maintenance
- Improved scheduling accuracy through data-driven insights
- Enhanced customer communication and transparency
- Reduced operational costs through optimized resource allocation
- Increased technician productivity and efficiency
Implementation Strategies for Plug-and-Play IoT Kits
Successfully implementing plug-and-play IoT kits requires careful planning and execution. Here are some key considerations:
Hardware Selection and Deployment
Choosing the right hardware is crucial for effective FSM implementation. Factors to consider include:
- Compatibility with existing infrastructure
- Ease of installation and maintenance
- Durability and reliability of sensors and devices
- Power requirements and battery life for remote locations
Deployment strategies may involve:
- Gradual rollout to test and refine the system
- Training technicians on new equipment usage
- Establishing clear protocols for device maintenance and replacement
Software Integration and Data Management
Effective integration of IoT data with FSM software is essential for maximizing benefits. Considerations include:
- API compatibility between IoT devices and FSM platforms
- Data visualization tools for easy interpretation of sensor readings
- Security measures to protect sensitive equipment information
- Scalability of the system to accommodate growing data volumes
Change Management and Training
Implementing new technologies often requires cultural shifts within organizations. Key aspects of change management include:
- Educating stakeholders on the benefits and functionality of IoT-enabled FSM
- Providing hands-on training sessions for technicians
- Addressing potential resistance to adopting new workflows
- Establishing clear policies for data privacy and security
Case Studies and Success Stories
Several companies have successfully implemented plug-and-play IoT kits in their field service operations, resulting in significant improvements:
Example 1: HVAC Company Reduces Service Calls by 30%
A leading HVAC company deployed temperature and humidity sensors in residential units. These sensors automatically triggered service requests when thresholds were exceeded. As a result, the company reduced unnecessary service calls by 30% while improving response times and customer satisfaction.
Example 2: Manufacturing Plant Optimizes Equipment Maintenance
A large manufacturing facility integrated vibration sensors and predictive analytics into their FSM process. This allowed them to schedule preventive maintenance based on real-time equipment condition rather than fixed intervals. The result was a 25% reduction in downtime and a 15% decrease in overall maintenance costs.
Challenges and Limitations
While plug-and-play IoT kits offer numerous benefits, there are also challenges to consider:
- Initial investment costs for hardware and software
- Potential cybersecurity risks associated with increased connectivity
- Need for ongoing support and maintenance of IoT devices
- Potential for false alarms or inaccurate readings from sensors
- Resistance to change among traditionalists within the organization
Future Trends in Field Service Management with IoT
As technology continues to evolve, we can expect several exciting developments in FSM with IoT:
- Artificial intelligence integration for more sophisticated predictive maintenance
- Augmented reality applications for enhanced troubleshooting
- Blockchain technology for secure data sharing and verification
- Edge computing for improved real-time processing of IoT data
- Standardization efforts to simplify integration across different platforms
Conclusion
Field Service Management with plug-and-play IoT kits represents a significant leap forward in operational efficiency and customer satisfaction. By leveraging the power of connected devices and data-driven decision-making, organizations can optimize their field service operations, reduce costs, and improve overall performance.
As the technology continues to mature, it’s crucial for field service managers to stay informed about the latest developments and best practices. Embracing this innovative approach will position organizations at the forefront of efficient field service delivery in the digital age.