Field Service Management with Field Asset Tagging via NFC Enhancing Efficiency and Accuracy
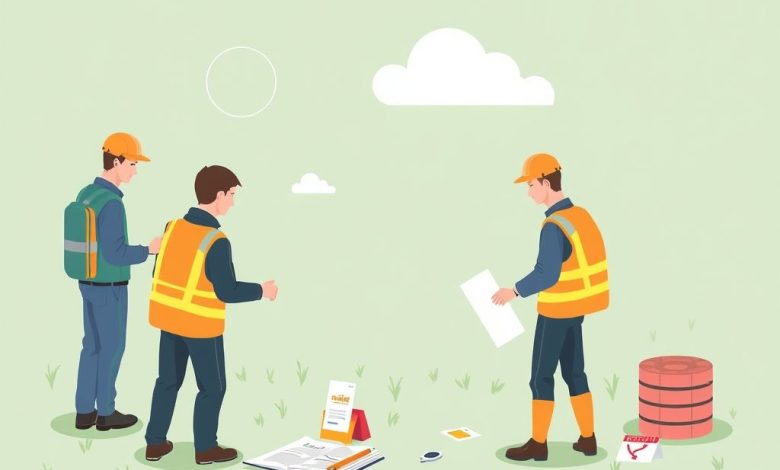
Introduction
Field Service Management (FSM) is a critical component of modern business operations, particularly in industries such as manufacturing, healthcare, and telecommunications. As companies strive to improve efficiency, reduce costs, and enhance customer satisfaction, FSM has become increasingly sophisticated. One innovative technology that has revolutionized FSM is Near Field Communication (NFC) asset tagging. This article explores how NFC-based field asset tagging enhances FSM processes, improves operational efficiency, and provides valuable insights for field service managers.
- The Evolution of Field Service Management
- The Role of NFC in Field Asset Tagging
- Benefits of NFC-based Field Asset Tagging in FSM
- Improved Accuracy and Efficiency
- Enhanced Asset Tracking
- Streamlined Maintenance Scheduling
- Increased Customer Satisfaction
- Data-driven Decision Making
- Implementation Challenges and Solutions
- Case Studies: Successful Implementation of NFC in FSM
- Conclusion
The Evolution of Field Service Management
Field Service Management has undergone significant transformations since its inception. From manual scheduling and paper-based work orders to digital platforms and mobile applications, the industry has embraced technological advancements to streamline operations. Today, FSM encompasses various aspects of field service delivery, including:
- Work order management
- Resource allocation
- Scheduling optimization
- Inventory tracking
- Customer communication
- Performance monitoring
These components work together to ensure efficient service delivery while maintaining high-quality standards.
The Role of NFC in Field Asset Tagging
Near Field Communication (NFC) is a short-range wireless communication technology that allows devices to exchange data when in close proximity (typically within 10 cm). In the context of field asset tagging, NFC enables seamless interaction between physical assets and digital systems. Here’s how NFC contributes to improved FSM:
- Automatic Identification: NFC tags can be attached to equipment, vehicles, or other assets, allowing for quick identification without manual scanning.
- Data Storage: NFC tags can store small amounts of information, such as asset IDs, maintenance history, or configuration details.
- Real-time Updates: NFC technology allows for instant updates to asset information, ensuring data accuracy and reducing administrative overhead.
Benefits of NFC-based Field Asset Tagging in FSM
Implementing NFC-based field asset tagging in FSM offers numerous advantages:
Improved Accuracy and Efficiency
NFC tags eliminate the need for manual data entry, reducing errors associated with human input. This leads to faster processing of work orders and improved overall efficiency in service delivery.
Enhanced Asset Tracking
Real-time location tracking of assets becomes possible when NFC tags are integrated with GPS technology. This feature helps in optimizing resource allocation and improving response times to customer requests.
Streamlined Maintenance Scheduling
By storing maintenance history and schedule information directly on NFC tags, FSM systems can automatically generate reminders and schedule preventive maintenance, ensuring equipment longevity and minimizing unexpected downtime.
Increased Customer Satisfaction
Quick access to accurate asset information enables faster diagnosis of issues and more efficient resolution of problems. This translates to higher customer satisfaction scores and increased loyalty.
Data-driven Decision Making
The wealth of data generated by NFC tags provides valuable insights into asset usage patterns, maintenance needs, and operational trends. This information can be used to optimize service routes, improve inventory management, and enhance overall FSM strategies.
Implementation Challenges and Solutions
While the benefits of NFC-based field asset tagging in FSM are substantial, implementation can present challenges:
- Cost of NFC Tags: Initially, the cost of NFC tags may seem prohibitive compared to traditional barcodes or RFID tags.
Solution: Gradual rollout, starting with high-value or frequently used assets, can help offset initial costs.
2. Compatibility Issues: Not all devices or systems may be compatible with NFC technology.
Solution: Invest in NFC-compatible hardware and ensure proper integration with existing FSM software.
3. Training Employees: Staff may need training on how to use NFC-enabled devices effectively.
Solution: Provide comprehensive training sessions and create user-friendly guidelines for NFC interactions.
4. Security Concerns: There may be concerns about data privacy and security when using NFC technology.
Solution: Implement robust encryption methods and adhere to industry-standard security protocols.
Case Studies: Successful Implementation of NFC in FSM
Several companies have successfully implemented NFC-based field asset tagging in their FSM systems, demonstrating tangible improvements in operational efficiency and customer satisfaction.
Example 1: Utility Company
A large utility company replaced its traditional meter reading system with NFC-enabled smart meters. This change resulted in:
- Reduced time spent on meter readings from 30 minutes to less than 10 minutes per property
- Elimination of manual data entry errors
- Improved real-time monitoring of energy consumption patterns
- Faster response times to customer inquiries about energy usage
Example 2: Manufacturing Facility
An industrial manufacturing plant implemented NFC tags on critical machinery parts. The outcome was:
- 25% reduction in equipment downtime
- Improved predictive maintenance scheduling
- Enhanced traceability of production materials
- Better inventory management leading to reduced stockouts
Conclusion
Field Service Management with NFC-based field asset tagging represents a significant leap forward in operational efficiency and customer satisfaction. By leveraging the power of Near Field Communication technology, companies can streamline their FSM processes, gain valuable insights into their operations, and deliver superior service to their customers.
As the technology continues to evolve, it’s likely that we’ll see even more innovative applications of NFC in FSM. For field service managers looking to stay ahead of the curve, embracing NFC-based field asset tagging should be a top priority in their digital transformation strategies.
Remember, the key to successful implementation lies not just in adopting the technology, but in understanding its potential impact on your specific business operations and tailoring its application accordingly. As you embark on this journey, keep in mind that the future of FSM is not just about managing field services – it’s about revolutionizing them with cutting-edge technology.