Field Service Management with Digital Twin Diagnostics Revolutionizing Maintenance and Repair Operations
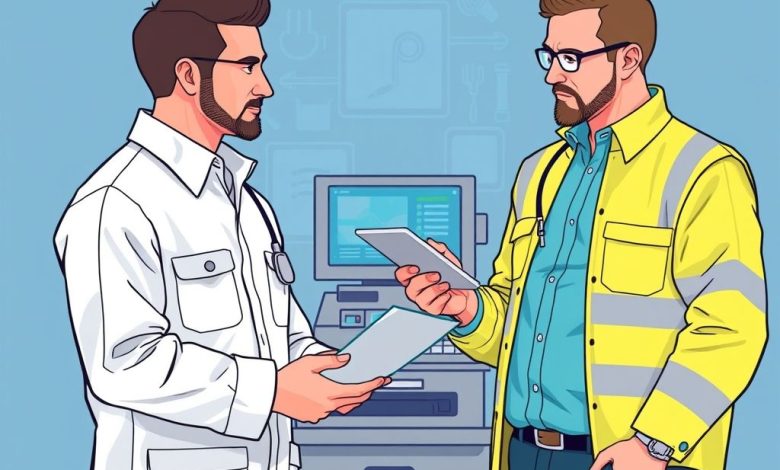
Field Service Management with Digital Twin Diagnostics: Revolutionizing Maintenance and Repair
Introduction
Field service management has long been a crucial aspect of various industries, including manufacturing, healthcare, and telecommunications. Traditionally, field service operations relied heavily on manual processes and limited technological support. However, the advent of digital twin diagnostics has transformed the landscape of field service management, offering unprecedented levels of efficiency, accuracy, and cost-effectiveness.
In this article, we will explore the concept of field service management, the role of digital twin diagnostics within this context, and the benefits it brings to organizations and their customers alike. We will also discuss the challenges associated with implementing such technology and provide insights into its future potential.
Understanding Field Service Management
Field service management refers to the processes and systems used by organizations to manage and coordinate work performed outside of a traditional office environment. This includes tasks such as equipment maintenance, repairs, installations, and troubleshooting across various sites or customer premises.
Traditionally, field service operations were characterized by:
- Manual scheduling and dispatching
- Limited real-time data collection
- Paper-based reporting
- Inconsistent quality of service delivery
- Difficulty in tracking inventory and resources
These limitations often resulted in inefficiencies, delays, and increased costs for both service providers and customers.
The Rise of Digital Twin Diagnostics
Digital twin diagnostics represents a significant advancement in field service management technology. It involves creating virtual replicas of physical assets, which are then monitored and analyzed in real-time to predict and prevent issues before they occur.
Key features of digital twin diagnostics include:
- Real-time monitoring of asset performance
- Predictive analytics for maintenance scheduling
- Remote diagnostics and troubleshooting
- Improved first-time fix rates
- Enhanced customer satisfaction through faster response times
Benefits of Digital Twin Diagnostics in Field Service Management
- Increased Efficiency
Digital twin diagnostics enables more efficient scheduling and resource allocation. By analyzing real-time data from connected devices, service teams can prioritize jobs based on urgency and optimize routes to minimize travel time and fuel consumption.
2. Improved Accuracy
Virtual replicas of assets allow technicians to access detailed information about each device before arriving at the job site. This reduces the likelihood of misdiagnosis and improves the overall quality of service delivery.
3. Enhanced Customer Experience
Real-time updates and proactive communication with customers regarding estimated arrival times and job status contribute to higher customer satisfaction scores. Additionally, remote diagnostics can often resolve issues without requiring a physical visit, further improving the customer experience.
4. Cost Reduction
By predicting and preventing issues before they occur, organizations can reduce unnecessary service calls and extend the lifespan of equipment. This leads to significant cost savings in terms of reduced labor, parts, and travel expenses.
5. Data-Driven Decision Making
The wealth of data generated by digital twin diagnostics provides valuable insights into equipment performance, usage patterns, and common issues. This data can be leveraged to improve product design, optimize maintenance schedules, and develop more effective training programs for technicians.
Challenges in Implementing Digital Twin Diagnostics
While the benefits of digital twin diagnostics are substantial, there are several challenges that organizations may face when implementing this technology:
- Initial Investment Costs
Implementing a comprehensive digital twin diagnostic system requires significant upfront investment in hardware, software, and training. This can be a barrier for smaller organizations or those with limited budgets.
2. Integration Complexity
Integrating digital twin diagnostics with existing field service management systems and processes can be complex. It may require significant changes to current workflows and may necessitate retraining of staff.
3. Data Security Concerns
The collection and transmission of sensitive data related to equipment performance and customer information raise important privacy and security considerations. Organizations must ensure robust data protection measures are in place.
4. Technological Dependence
Overreliance on digital twin diagnostics could potentially lead to a loss of traditional skills among technicians. Organizations must balance the benefits of automation with the need to maintain human expertise.
Case Studies and Success Stories
Several companies have successfully implemented digital twin diagnostics in their field service operations, resulting in significant improvements in efficiency and customer satisfaction.
For example, Siemens, a global leader in industrial automation, has reported a 30% reduction in service call volumes and a 25% improvement in first-time fix rates after deploying digital twin diagnostics across its installed base of industrial equipment.
Similarly, a major telecommunications provider in Europe saw a 40% increase in technician productivity and a 15% reduction in operational costs after adopting digital twin diagnostics for network maintenance.
Conclusion
Field service management with digital twin diagnostics represents a paradigm shift in how organizations approach equipment maintenance and repair. By leveraging the power of digital twins, companies can achieve unprecedented levels of efficiency, accuracy, and customer satisfaction in their field service operations.
As this technology continues to evolve, we can expect even more sophisticated applications of digital twin diagnostics in fields beyond traditional maintenance. From predictive healthcare to smart city infrastructure management, the potential impact of digital twin diagnostics is vast and exciting.
For field service managers looking to stay ahead of the curve, embracing digital twin diagnostics is not just a choice – it’s a necessity. As the industry continues to embrace this transformative technology, those who adapt early will reap the rewards of improved operational efficiency, enhanced customer experiences, and sustainable competitive advantage in their respective markets.