Field Service Management with Cold Chain Monitoring Optimizing Temperature-Controlled Deliveries
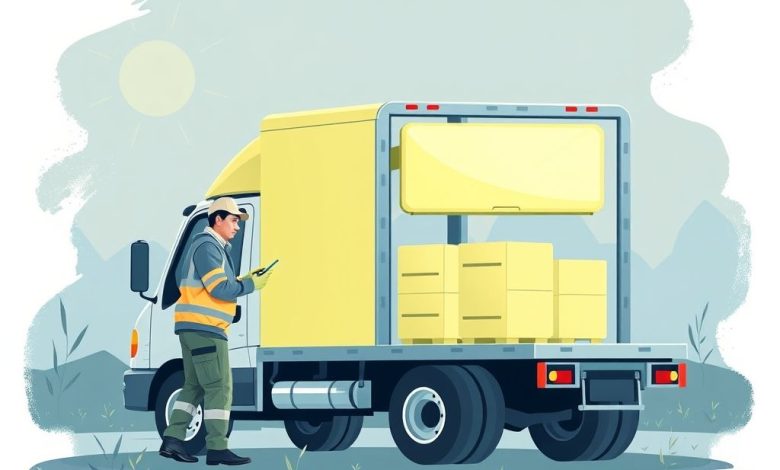
Field Service Management with Cold Chain Monitoring
Introduction
Field service management (FSM) is a critical component of many industries, particularly those dealing with perishable goods or time-sensitive services. The integration of cold chain monitoring technology has revolutionized how FSM operates, ensuring optimal efficiency and quality control throughout the entire process. This article will explore the intersection of field service management and cold chain monitoring, highlighting its benefits, challenges, and best practices.
What is Field Service Management?
Field service management refers to the processes and systems used to manage and coordinate work performed outside of a traditional office environment. It encompasses various aspects such as scheduling, dispatching, resource allocation, and customer interaction. In industries like healthcare, telecommunications, and utilities, FSM plays a crucial role in maintaining operational efficiency and customer satisfaction.
The Role of Cold Chain Monitoring in Field Service Management
Cold chain monitoring involves tracking and managing temperature-sensitive products from production to consumption. When integrated with field service management, it provides real-time data on product temperatures, location, and environmental conditions. This information allows service technicians to:
- Identify potential issues before they occur
- Prioritize high-risk deliveries
- Optimize delivery routes based on current conditions
- Provide accurate status updates to customers
Benefits of Cold Chain Monitoring in FSM
The integration of cold chain monitoring technology offers several advantages:
- Improved product quality: By maintaining consistent temperatures throughout the delivery process, the risk of spoilage is significantly reduced.
- Enhanced customer satisfaction: Real-time updates provide customers with accurate information about their deliveries.
- Increased operational efficiency: Automated temperature tracking eliminates manual data entry and reduces human error.
- Cost savings: Optimized routes and reduced spoilage lead to lower overall costs for businesses.
- Compliance adherence: Automated monitoring ensures regulatory compliance with food safety standards.
Challenges in Implementing Cold Chain Monitoring
Despite its benefits, implementing cold chain monitoring in field service management comes with some challenges:
- Initial investment costs: The necessary hardware and software can be expensive to implement initially.
- Data management: The sheer volume of data generated by temperature sensors requires robust data management systems.
- Battery life: Temperature sensors require frequent battery replacements or recharging, especially in remote areas.
- Connectivity issues: In some regions, reliable internet connectivity may be limited, affecting real-time data transmission.
Best Practices for Implementing Cold Chain Monitoring in FSM
To overcome the challenges and maximize the benefits of cold chain monitoring in field service management, consider the following best practices:
- Conduct thorough needs assessment: Evaluate your specific requirements before selecting a monitoring solution.
- Invest in quality hardware: Choose durable temperature sensors and ruggedized devices suitable for outdoor use.
- Implement robust data analytics: Develop systems capable of processing large volumes of real-time data efficiently.
- Establish clear protocols: Define procedures for handling alerts and exceptions generated by the monitoring system.
- Regular training: Educate staff on proper use and maintenance of monitoring equipment and software.
- Continuous improvement: Regularly review and refine your FSM processes based on insights gained from cold chain monitoring data.
Case Study: Healthcare Industry
In the healthcare industry, where medical supplies often require precise temperature control, the integration of cold chain monitoring with field service management has been particularly impactful. Here’s an example:
A major pharmaceutical company implemented a cold chain monitoring system integrated with their FSM platform. The system tracked temperature-sensitive vaccines during transportation from manufacturing facilities to distribution centers and finally to healthcare providers.
Results showed a significant reduction in vaccine spoilage rates, from 5% to less than 1%. This improvement led to cost savings of approximately $250,000 annually. Additionally, the real-time tracking enabled faster response times when temperature deviations were detected, ensuring timely replacement of affected shipments.
Conclusion
Field service management with cold chain monitoring represents a powerful synergy in modern logistics and supply chain management. By leveraging technology to track and maintain optimal conditions for time-sensitive goods, businesses can enhance product quality, improve customer satisfaction, and optimize operational efficiency.
As this technology continues to evolve, we can expect even more sophisticated solutions that integrate artificial intelligence, blockchain, and the Internet of Things (IoT) to further revolutionize field service management and cold chain monitoring. For field service managers looking to stay ahead in their industry, embracing these innovations could be the key to maintaining competitive advantage and delivering exceptional results.