Field Service Management in Mining Field Operations Efficient Maintenance Strategies for Underground Success
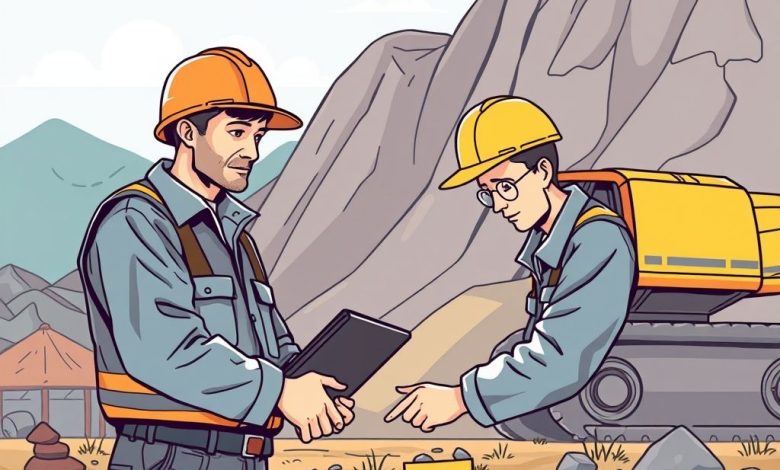
Introduction
Field Service Management (FSM) plays a crucial role in the success of mining operations. It encompasses various aspects of managing and executing field services, from scheduling and dispatching to monitoring and reporting. In the context of mining, FSM is particularly vital due to the remote nature of many mining sites and the need for efficient management of resources and equipment.
- The Importance of Field Service Management in Mining
- Key Components of Field Service Management in Mining
- Scheduling and Dispatching
- Work Order Management
- Inventory Management
- Remote Monitoring and Maintenance
- Challenges in Implementing Field Service Management in Mining
- Best Practices for Implementing Field Service Management in Mining
- Conclusion
The Importance of Field Service Management in Mining
Mining operations often take place in remote locations, making it challenging to manage field services effectively. However, proper implementation of FSM can significantly improve operational efficiency, reduce costs, and enhance safety standards. Some key reasons why FSM is essential in mining include:
- Improved resource allocation
- Enhanced customer satisfaction through timely service delivery
- Increased productivity and efficiency
- Better tracking and management of assets and equipment
- Improved safety protocols and compliance with regulations
Key Components of Field Service Management in Mining
Scheduling and Dispatching
Scheduling and dispatching are critical components of FSM in mining operations. These processes involve:
- Creating optimized schedules based on job requirements and technician availability
- Assigning tasks to appropriate technicians or teams
- Managing real-time updates and changes to schedules
- Ensuring seamless communication between dispatchers and field technicians
Effective scheduling and dispatching systems help minimize downtime, reduce travel times, and ensure that the right personnel are deployed for each task.
Work Order Management
Work order management is another crucial aspect of FSM in mining. This process involves:
- Receiving and processing work requests from customers or internal stakeholders
- Assigning priorities to work orders based on urgency and importance
- Tracking progress and status updates throughout the job lifecycle
- Managing attachments and documentation related to each work order
A robust work order management system helps ensure that all issues are addressed promptly and efficiently, contributing to overall operational excellence.
Inventory Management
Proper inventory management is critical in mining operations due to the large number of assets and equipment involved. FSM systems should include:
- Real-time tracking of inventory levels
- Automated reordering based on predefined thresholds
- Integration with other systems like accounting and procurement
- Reporting capabilities to analyze usage patterns and optimize stock levels
Effective inventory management helps reduce costs associated with overstocking or understocking, improves response times, and ensures that necessary equipment is always available when needed.
Remote Monitoring and Maintenance
Remote monitoring and maintenance have become increasingly important in modern mining operations. FSM systems should incorporate features such as:
- Real-time monitoring of equipment performance and health
- Predictive maintenance capabilities
- Remote troubleshooting and diagnostics
- Integration with IoT devices for enhanced data collection
These capabilities allow for proactive maintenance, reduced downtime, and improved safety standards by identifying potential issues before they become major problems.
Challenges in Implementing Field Service Management in Mining
Despite its numerous benefits, implementing FSM in mining operations can present several challenges:
- Connectivity Issues: Many mining sites lack reliable internet connectivity, making real-time communication challenging.
- Data Privacy Concerns: The sensitive nature of mining operations requires strict data protection measures.
- Technological Limitations: Some older equipment may not be compatible with advanced FSM systems.
- Resistance to Change: Staff may resist adopting new technology and processes.
- High Initial Costs: Implementing comprehensive FSM solutions can be expensive, especially for smaller operations.
Best Practices for Implementing Field Service Management in Mining
To overcome these challenges and ensure successful implementation of FSM in mining operations, consider the following best practices:
- Start Small: Begin with a pilot program in one area or department before expanding across the entire operation.
- Invest in Training: Provide comprehensive training to staff on new systems and processes.
- Ensure Data Security: Implement robust security measures to protect sensitive operational data.
- Leverage Existing Infrastructure: Utilize existing communication networks and equipment where possible to minimize costs.
- Regularly Review and Update: Continuously assess and improve FSM processes based on feedback and changing operational needs.
Conclusion
Field Service Management is a critical component of successful mining operations. By implementing robust FSM systems, mining companies can improve efficiency, reduce costs, enhance safety standards, and ultimately increase profitability. As technology continues to evolve, it’s essential for mining operations to stay ahead of the curve by adopting innovative FSM solutions.
While challenges may arise during implementation, the benefits of FSM far outweigh the costs. Mining companies that embrace FSM will be better positioned to compete in an increasingly competitive global market and contribute to sustainable mining practices for generations to come.