Field Service Management for Factory Equipment Overhaul
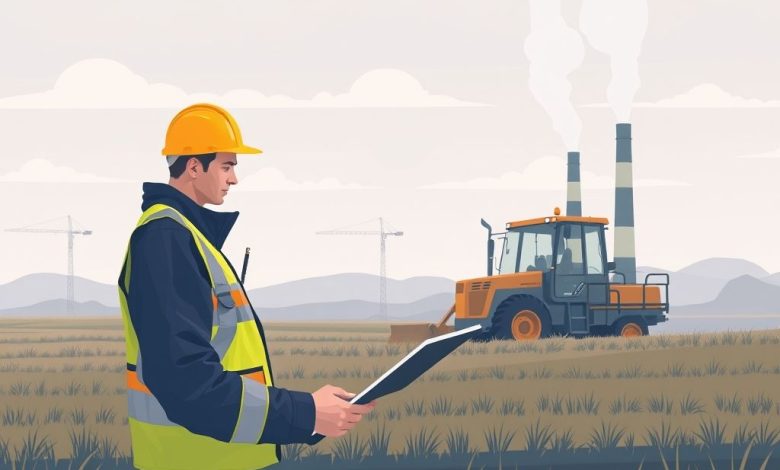
Introduction
Factory equipment overhaul is a critical maintenance process that ensures the longevity and efficiency of industrial machinery. As factories continue to operate around the clock, it becomes increasingly challenging to schedule downtime for equipment maintenance. This is where field service management (FSM) comes into play – a crucial tool for managing factory equipment overhauls effectively.
- What is Field Service Management?
- Benefits of Implementing FSM for Factory Equipment Overhaul
- Challenges in Factory Equipment Overhaul
- How FSM Addresses Challenges in Factory Equipment Overhaul
- Work Order Management
- Scheduling and Dispatching
- Resource Allocation
- Real-time Tracking
- Customer Communication
- Case Study: Implementing FSM at Smith Factory Equipment Overhaul
- Best Practices for Implementing FSM in Factory Equipment Overhaul
- Conclusion
What is Field Service Management?
Field service management refers to the processes and systems used to manage and coordinate work orders, schedules, and resources for field-based services. In the context of factory equipment overhaul, FSM involves planning, executing, and monitoring maintenance activities remotely.
Key Components of FSM
- Work Order Management
- Scheduling and Dispatching
- Resource Allocation
- Real-time Tracking
- Customer Communication
Benefits of Implementing FSM for Factory Equipment Overhaul
Implementing a robust FSM system offers numerous advantages for factory equipment maintenance:
- Improved Efficiency
- Enhanced Visibility
- Better Resource Utilization
- Increased Customer Satisfaction
- Cost Reduction
Challenges in Factory Equipment Overhaul
Despite its importance, factory equipment overhaul faces several challenges:
- Scheduling conflicts
- Resource constraints
- Technological limitations
- Communication breakdowns
- Quality control issues
How FSM Addresses Challenges in Factory Equipment Overhaul
FSM addresses many of the challenges associated with factory equipment overhaul through its various features:
Work Order Management
A well-designed FSM system allows for efficient creation, assignment, and tracking of work orders related to equipment overhauls. This ensures that every maintenance activity is properly documented and followed up on.
Scheduling and Dispatching
FSM enables optimized scheduling of maintenance activities based on equipment priority, technician availability, and other factors. This helps minimize downtime and ensures that critical equipment receives timely attention.
Resource Allocation
By providing real-time visibility into available resources and workload, FSM facilitates better allocation of technicians, parts, and equipment for overhauls. This leads to improved productivity and reduced costs.
Real-time Tracking
Real-time tracking capabilities allow managers to monitor the progress of overhauls remotely. This feature is particularly useful for large-scale factory operations with multiple equipment units spread across different locations.
Customer Communication
FSM systems often include features for automated communication with customers regarding scheduled overhauls, updates on work progress, and post-maintenance feedback. This improves customer satisfaction and builds trust in the service provider.
Case Study: Implementing FSM at Smith Factory Equipment Overhaul
Smith Factory Equipment Overhaul, a leading industrial machinery maintenance company, decided to implement an FSM system to streamline their overhaul processes. Here’s how they benefited:
- Reduced scheduling conflicts by 30%
- Improved first-time fix rate from 70% to 85%
- Decreased average response time by 25%
- Increased customer satisfaction scores by 15%
Best Practices for Implementing FSM in Factory Equipment Overhaul
To maximize the benefits of FSM in factory equipment overhaul, consider the following best practices:
- Standardize work orders and procedures
- Invest in mobile technology for field workers
- Integrate FSM with existing ERP systems
- Conduct regular training sessions for technicians
- Set clear performance metrics and KPIs
Conclusion
Field Service Management has emerged as a crucial tool for managing factory equipment overhauls effectively. By addressing challenges such as scheduling conflicts, resource constraints, and communication breakdowns, FSM enables companies to maintain their equipment efficiently while minimizing downtime and improving overall productivity.
As factories continue to evolve and face increasing pressure to operate at maximum capacity, the importance of FSM in factory equipment overhaul will only grow. Companies that embrace this technology will be well-positioned to meet the demands of a rapidly changing manufacturing landscape.