Field Service Management for Water Pipeline Maintenance
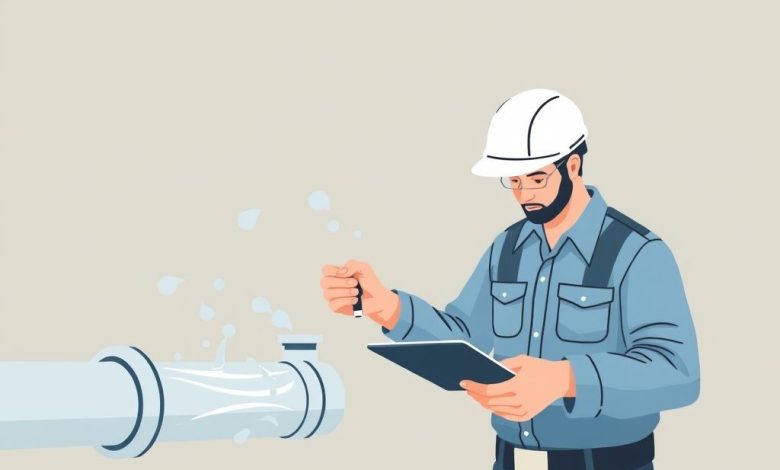
Introduction
Field Service Management (FSM) plays a crucial role in ensuring the efficient maintenance of water pipelines. As urban populations grow and infrastructure ages, maintaining reliable water supply systems becomes increasingly important. This article explores how FSM technologies can optimize water pipeline maintenance operations, improve efficiency, and enhance customer satisfaction.
The Importance of Water Pipeline Maintenance
Water pipelines are critical infrastructure that requires regular maintenance to prevent leaks, ensure water quality, and maintain pressure. However, traditional maintenance methods often rely on manual processes, which can lead to inefficiencies and potential safety hazards. Modern FSM solutions offer a more streamlined approach to managing water pipeline maintenance tasks.
Challenges in Traditional Water Pipeline Maintenance
- Manual data entry and reporting
- Inefficient scheduling and resource allocation
- Lack of real-time monitoring capabilities
- Difficulty in tracking equipment and assets
- Limited visibility into job status and completion times
These challenges can result in delayed responses to issues, increased costs, and compromised water quality. By implementing FSM technologies, many of these problems can be addressed effectively.
Key Components of Field Service Management for Water Pipeline Maintenance
A robust FSM system typically includes several key components:
- Scheduling and Dispatching
- Work Order Management
- Inventory and Equipment Tracking
- Mobile Workforce Management
- Customer Relationship Management (CRM)
- Reporting and Analytics
Each of these components contributes to a seamless and efficient maintenance process.
Scheduling and Dispatching
Effective scheduling is crucial for water pipeline maintenance. FSM systems use algorithms to optimize routes and assign jobs to technicians based on their location, skillset, and availability. This ensures that the right person is sent to the right location at the right time.
Work Order Management
Work order management is at the heart of FSM for water pipeline maintenance. It involves creating, assigning, and tracking tasks related to pipe repairs, inspections, and other maintenance activities.
Inventory and Equipment Tracking
Proper inventory management is essential for maintaining the right tools and equipment for each job. FSM systems allow managers to track asset locations, usage rates, and maintenance schedules, ensuring that everything needed for a job is available when required.
Mobile Workforce Management
Mobile workforce management enables technicians to access critical information and complete work orders directly from their mobile devices. This includes:
- Job details and instructions
- Customer information
- Inventory management
- Time tracking
- Signature capture for completion verification
Mobile apps also allow technicians to update job status in real-time, providing immediate visibility to managers.
Customer Relationship Management (CRM)
A CRM component helps manage customer interactions and data throughout the entire service lifecycle. This includes:
- Service history
- Complaint resolution
- Preventive maintenance scheduling
- Billing and invoicing
By maintaining strong relationships with customers, water utility companies can improve satisfaction levels and reduce repeat calls.
Reporting and Analytics
FSM systems generate valuable insights through reporting and analytics capabilities. These reports help managers:
- Identify trends in maintenance activities
- Optimize resource allocation
- Improve response times
- Reduce costs
- Enhance overall operational efficiency
Implementation Strategies for FSM in Water Pipeline Maintenance
Implementing an FSM system for water pipeline maintenance involves several key steps:
- Assess current processes and identify pain points
- Select an appropriate FSM solution
- Customize the system to meet specific needs
- Train staff on new technologies
- Gradually phase in new processes
- Monitor progress and gather feedback
Case Study: City of Los Angeles’ Water Department
The City of Los Angeles’ Water Department implemented an FSM system to streamline their water pipeline maintenance operations. As a result, they experienced:
- 25% reduction in response times
- 15% decrease in maintenance costs
- Improved technician productivity
- Enhanced customer satisfaction
These outcomes demonstrate the tangible benefits of implementing FSM technologies in water pipeline maintenance.
Conclusion
Field Service Management is revolutionizing the way water pipeline maintenance is conducted. By leveraging advanced technologies such as mobile workforce management, work order automation, and real-time tracking, water utilities can significantly improve their operational efficiency, reduce costs, and enhance customer satisfaction.
As the world’s population continues to grow and urbanization increases, the importance of reliable water infrastructure will only intensify. Field Service Management solutions offer a powerful toolset for water utility companies to maintain their critical assets effectively and efficiently.
While challenges remain, the adoption of FSM technologies represents a significant step forward in ensuring the long-term sustainability of our water supply systems. As these technologies continue to evolve, we can expect even greater improvements in water pipeline maintenance operations in the years to come.