Field Service Management for Water Filtration Systems
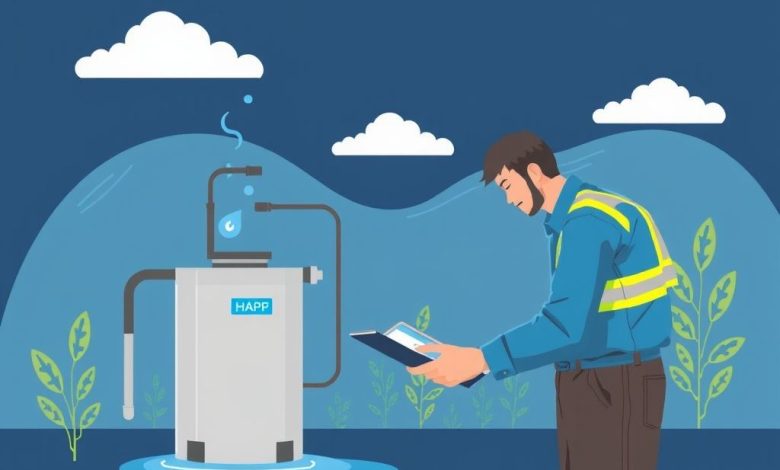
Introduction
Field Service Management (FSM) plays a crucial role in maintaining water filtration systems. These systems are essential for providing clean drinking water to communities worldwide. Effective FSM ensures that water filtration equipment operates efficiently, maintains water quality standards, and minimizes downtime. This article explores the importance of FSM in water filtration systems, its challenges, best practices, and future trends.
Importance of Field Service Management in Water Filtration Systems
Water filtration systems require regular maintenance to ensure optimal performance. FSM helps maintain these systems by:
- Scheduling routine inspections and maintenance tasks
- Identifying and addressing issues promptly
- Reducing equipment downtime
- Extending the lifespan of filtration units
- Ensuring compliance with regulatory requirements
Proper FSM not only improves system efficiency but also contributes to public health by ensuring consistent water quality.
Challenges in Field Service Management for Water Filtration Systems
Despite its importance, FSM for water filtration systems faces several challenges:
- Remote locations: Many water treatment facilities are located in remote areas, making it difficult to access them quickly.
- Limited resources: Some organizations may lack the necessary tools, technology, or trained personnel to manage FSM effectively.
- Regulatory compliance: Water treatment facilities must adhere to strict regulations, which can be challenging to maintain without proper FSM.
- Budget constraints: Implementing and maintaining effective FSM programs can be costly.
Best Practices for Field Service Management in Water Filtration Systems
To overcome the challenges and ensure efficient FSM for water filtration systems, consider the following best practices:
- Implement a robust scheduling system:
- Use cloud-based FSM software to manage work orders and schedules
- Integrate GPS tracking to optimize route planning
- Set reminders for routine maintenance tasks
2. Invest in advanced diagnostic tools:
- Utilize IoT sensors to monitor system performance in real-time
- Implement predictive maintenance techniques to identify potential issues before they occur
- Conduct regular equipment audits to assess condition and performance
3. Train and certify technicians:
- Provide ongoing training on new technologies and maintenance procedures
- Certify technicians through industry-specific programs
- Ensure all staff understand the importance of FSM in water quality management
4. Develop a comprehensive inventory management system:
- Maintain accurate records of spare parts and consumables
- Implement just-in-time ordering to reduce stockouts
- Regularly review and update inventory lists based on usage patterns
5. Foster strong relationships with customers:
- Communicate clearly about scheduled maintenance and any issues
- Provide transparent reporting on system performance and maintenance activities
- Offer proactive solutions to minimize disruptions
6. Implement data analytics:
- Analyze FSM data to identify trends and areas for improvement
- Use insights to optimize scheduling and resource allocation
- Track key performance indicators such as response times and first-time fix rates
7. Prioritize safety:
- Conduct regular safety assessments of work environments
- Provide personal protective equipment (PPE) to technicians
- Establish clear protocols for handling hazardous materials
8. Stay updated with industry developments:
- Attend conferences and workshops to stay informed about new technologies and best practices
- Participate in online forums to share knowledge and learn from peers
- Collaborate with other FSM professionals to improve overall industry standards
Future Trends in Field Service Management for Water Filtration Systems
As technology continues to evolve, FSM for water filtration systems will likely incorporate more innovative approaches:
- Artificial Intelligence (AI) Integration:
- AI-powered chatbots to assist with scheduling and troubleshooting
- Predictive maintenance algorithms to anticipate equipment failures
2. Augmented Reality (AR):
- AR glasses to guide technicians during maintenance tasks
- Virtual reality training simulations for new hires
3. Blockchain Technology:
- Secure tracking of equipment history and maintenance records
- Transparent supply chain management for spare parts
4. Internet of Things (IoT):
- Real-time monitoring of water quality parameters
- Automated alerts for critical system failures
5. Robotics and Automation:
- Autonomous vehicles for transporting personnel and equipment
- Robotic arms for performing routine maintenance tasks
Conclusion
Field Service Management is crucial for maintaining water filtration systems effectively. By implementing best practices and staying ahead of technological trends, organizations can ensure optimal system performance while contributing to public health and safety.
As FSM continues to evolve, it will play an increasingly important role in managing complex water treatment infrastructure. The challenges faced by FSM professionals in this sector highlight the need for innovative solutions and continuous improvement in service delivery.
By prioritizing FSM, water treatment facilities can maintain high-quality drinking water standards, reduce operational costs, and contribute to sustainable development goals. As the global population grows, effective FSM for water filtration systems will become even more critical in ensuring clean water access for all.