Field Service Management Leveraging Historical Service Patterns for Enhanced Operational Efficiency
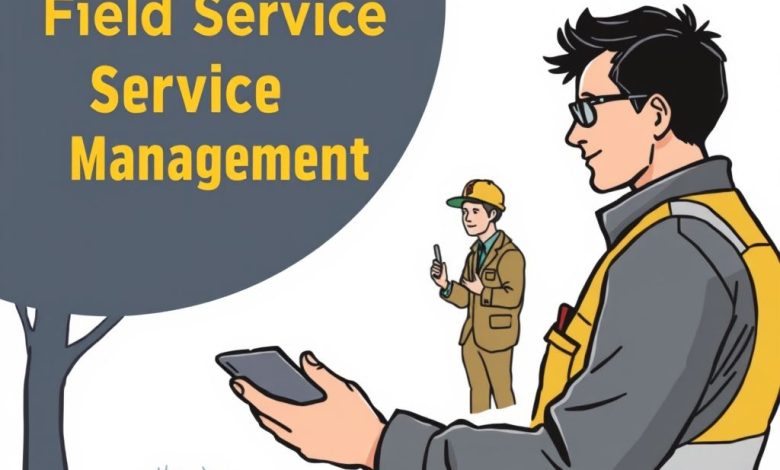
Field Service Management with Historical Service Patterns
Introduction
Field service management (FSM) refers to the processes and systems used to manage and coordinate work orders, schedules, and resources for field-based services. In today’s fast-paced business environment, FSM has become increasingly crucial for companies seeking to improve operational efficiency, customer satisfaction, and overall competitiveness. This article explores how historical service patterns can enhance field service management strategies, focusing on predictive maintenance techniques and data-driven decision making.
The Importance of Historical Data in Field Service Management
Historical data plays a vital role in optimizing field service operations. By analyzing past service requests, response times, and resolution rates, organizations can gain valuable insights into their customers’ needs and preferences. This information allows for more effective resource allocation, improved scheduling, and enhanced customer experience.
Key benefits of leveraging historical data in FSM include:
- Identifying recurring issues and developing targeted solutions
- Optimizing technician routes and reducing travel time
- Improving first-time fix rates through better preparation
- Enhancing customer communication and expectation management
Implementing Historical Service Pattern Analysis
To effectively implement historical service pattern analysis, organizations should consider the following steps:
- Data Collection and Storage
- Implement robust data collection systems that capture all relevant information from each service interaction
- Store this data in a centralized database for easy access and analysis
2. Data Analysis Tools
- Utilize specialized software designed for FSM data analysis
- Consider implementing machine learning algorithms to identify complex patterns
3. Regular Reporting and Visualization
- Create dashboards and reports that provide actionable insights from historical data
- Ensure real-time updates to keep stakeholders informed of current trends
4. Continuous Improvement Loop
- Regularly review and refine FSM processes based on analytical findings
- Encourage feedback from technicians and customers to further improve patterns recognition
Case Study: Predictive Maintenance in HVAC Services
One industry where historical service patterns have significantly impacted operations is heating, ventilation, and air conditioning (HVAC). By analyzing past service records, HVAC companies can predict equipment failures before they occur, reducing downtime and improving customer satisfaction.
Here’s how one HVAC company implemented predictive maintenance:
- Data Collection
- Implemented smart sensors on HVAC units to collect real-time performance data
- Integrated this data with historical service records and weather information
2. Pattern Recognition
- Used machine learning algorithms to identify correlations between environmental factors, unit performance, and service history
- Developed predictive models that forecast potential equipment failures
3. Proactive Maintenance
- Scheduled preventive maintenance visits based on predicted failure probabilities
- Provided customers with advance notice of upcoming maintenance activities
4. Improved Customer Experience
- Reduced unexpected breakdowns, minimizing inconvenience to customers
- Demonstrated proactive approach to customer care, enhancing brand reputation
Challenges and Limitations
While historical service pattern analysis offers numerous benefits, it also presents several challenges:
- Data Quality Issues
- Ensuring accuracy and completeness of historical data
- Addressing inconsistencies in reporting across different regions or teams
2. Technological Complexity
- Integrating various data sources and analysis tools
- Maintaining up-to-date skills among staff to interpret complex analytics outputs
3. Privacy Concerns
- Balancing the need for detailed historical data with customer privacy expectations
- Ensuring compliance with data protection regulations
4. Cost-Benefit Analysis
- Justifying investment in advanced analytics tools and training
- Measuring tangible improvements in operational efficiency and customer satisfaction
Conclusion
Implementing historical service pattern analysis in field service management can lead to significant improvements in operational efficiency, customer satisfaction, and overall business performance. By leveraging the power of historical data, organizations can make data-driven decisions, optimize their service delivery processes, and stay ahead of competitors in today’s fast-paced market.
As technology continues to evolve, we can expect even more sophisticated tools and techniques to emerge for analyzing historical service patterns. It is crucial for field service managers to embrace these innovations and continuously adapt their strategies to maximize the benefits of historical data analysis in FSM.
By combining traditional expertise with cutting-edge analytics, field service organizations can transform their operations and deliver exceptional value to their customers in an increasingly competitive landscape.