Field Service Management Leveraging Automation for Efficient Parts Replenishment
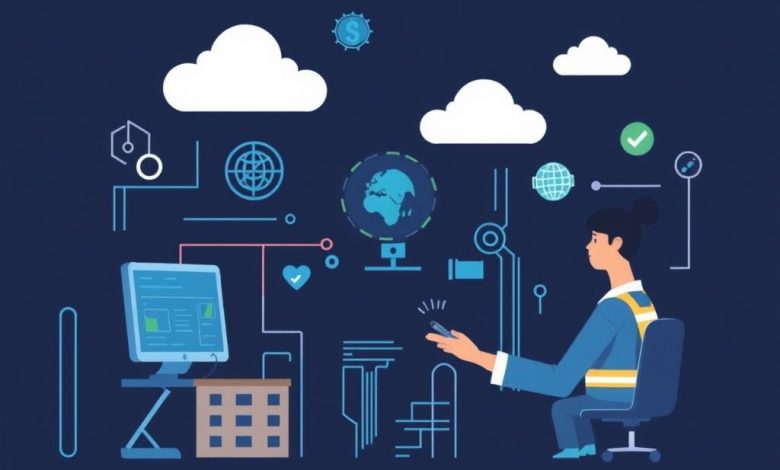
Introduction
Field Service Management (FSM) is a critical component of many businesses, particularly in industries such as HVAC, electrical work, plumbing, and home maintenance. As companies strive to provide efficient and cost-effective services, the need for effective FSM solutions has never been more pressing. One innovative approach that is gaining traction in the industry is Automated Parts Replenishment (APR). This technology integrates seamlessly with existing FSM systems to optimize inventory management and streamline operations.
What is Field Service Management?
Field Service Management refers to the processes and technologies used to manage and coordinate work performed outside of a traditional office environment. It encompasses various aspects of service delivery, including scheduling, dispatching, resource allocation, and customer communication. Effective FSM enables businesses to respond quickly to customer needs, improve operational efficiency, and enhance overall customer satisfaction.
Key Components of Field Service Management
- Scheduling and Dispatching
- Efficiently allocating resources based on job priority and technician availability
- Optimizing routes to minimize travel time and reduce costs
2. Resource Allocation
- Assigning appropriate technicians to jobs based on skill sets and location
- Managing vehicle fleets and maintaining equipment
3. Inventory Management
- Tracking stock levels and ordering supplies as needed
- Minimizing stockouts and overstocking
4. Customer Communication
- Providing timely updates on appointment status and estimated arrival times
- Handling customer inquiries and resolving issues efficiently
5. Reporting and Analytics
- Generating insights from service data to identify trends and areas for improvement
- Monitoring key performance indicators (KPIs) such as first-time fix rates and response times
The Challenge of Parts Replenishment
Traditionally, parts replenishment has been a manual process involving phone calls, emails, or paper-based systems. This approach often leads to delays, stockouts, and overstocking issues. The consequences can be severe, including:
- Delays in completing jobs due to missing parts
- Increased costs associated with expedited shipping or unnecessary inventory
- Dissatisfied customers waiting for delayed repairs or maintenance
- Wasted time and resources on managing inventory manually
How Automated Parts Replenishment Works
Automated Parts Replenishment integrates with FSM systems to create a seamless, efficient process for ordering and restocking parts. Here’s how it typically functions:
- Real-time Inventory Tracking
- Sensors and RFID tags monitor stock levels in real-time
- Automated alerts trigger when inventory falls below predetermined thresholds
2. AI-Powered Recommendations
- Machine learning algorithms analyze historical usage patterns
- Suggest optimal part quantities and types for each job
3. Automated Ordering
- System automatically generates purchase orders based on recommendations
- Integrates with supplier networks for quick fulfillment
4. Just-in-Time Delivery
- Parts are delivered precisely when needed, reducing storage requirements
- Reduces waste and minimizes the risk of obsolescence
5. Integration with FSM Systems
- Seamless communication between APR and scheduling/dispatching modules
- Ensures accurate part availability at the point of dispatch
Benefits of Automated Parts Replenishment
Implementing Automated Parts Replenishment brings numerous advantages to field service organizations:
Improved Efficiency
- Reduced administrative time spent on manual inventory management
- Faster response times as technicians have immediate access to necessary parts
- Optimized routes and schedules based on real-time inventory data
Cost Savings
- Elimination of overstocking and related storage costs
- Reduction in expedited shipping expenses
- Lower overall operational costs through improved resource allocation
Enhanced Customer Satisfaction
- Faster completion of jobs due to readily available parts
- More accurate estimates provided to customers
- Improved first-time fix rates leading to increased customer trust
Data-Driven Decision Making
- Access to detailed analytics on part usage and consumption patterns
- Ability to adjust inventory strategies based on actual demand
- Identification of opportunities for cost reduction and process improvement
Case Study: XYZ Plumbing Services
XYZ Plumbing Services, a medium-sized plumbing company operating in urban areas, implemented an Automated Parts Replenishment system alongside their existing Field Service Management software. Here’s how it impacted their operations:
Implementation Process
- Integration with Existing FSM System
- Installation of RFID tags on inventory items
- Training of staff on new system procedures
- Initial setup of part categories and reorder points
Results After Six Months
- Inventory accuracy improved from 85% to 98%
- Average job completion time reduced by 30 minutes
- Overstocking decreased by 40%
- Customer satisfaction scores increased by 25%
Challenges and Considerations
While Automated Parts Replenishment offers significant benefits, there are several factors to consider when implementing such a system:
- Initial Investment Costs
- Higher upfront expenses for hardware, software, and training
- Potential disruption to existing processes during transition period
2. Data Accuracy and Reliability
- Ensuring accurate tracking of inventory levels
- Addressing potential issues with sensor malfunctions or RFID tag loss
3. Supplier Integration
- Ensuring seamless communication between APR system and supplier networks
- Managing multiple suppliers for different parts categories
4. Scalability
- Adapting the system as business grows or evolves
- Handling fluctuations in demand during seasonal peaks
Conclusion
Field Service Management with Automated Parts Replenishment represents a significant leap forward in operational efficiency for service-based businesses. By integrating real-time inventory tracking, AI-powered recommendations, and automated ordering processes, companies can streamline their operations, reduce costs, and enhance customer satisfaction.
As technology continues to advance, we can expect even more sophisticated solutions to emerge. However, for many organizations, implementing Automated Parts Replenishment alongside their Field Service Management systems could be the key to unlocking improved performance and competitiveness in today’s fast-paced service industry.
For field service managers looking to stay ahead of the curve, exploring Automated Parts Replenishment solutions should be at the top of their priority list. The potential benefits in terms of efficiency, cost savings, and customer satisfaction make it an investment worth considering for any organization serious about optimizing its field service operations.