Field Service Management for Non-Destructive Testing Services
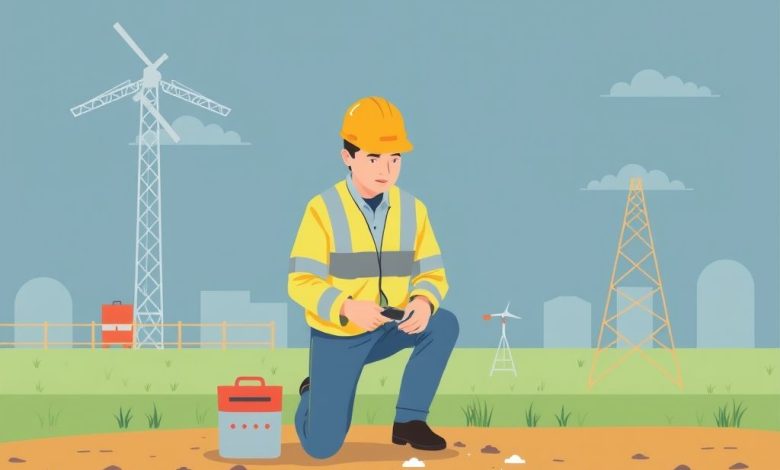
Introduction
Field Service Management (FSM) is a crucial aspect of modern business operations, particularly in industries where equipment maintenance and inspection are essential. One such industry is Non-Destructive Testing (NDT), which requires specialized skills and equipment to inspect materials and components without causing damage. In this article, we’ll explore how FSM plays a vital role in NDT services, focusing on the challenges faced by field service managers and the strategies they employ to ensure efficient and effective service delivery.
- The Importance of Field Service Management in NDT
- Challenges Faced by Field Service Managers in NDT
- Strategies for Effective Field Service Management in NDT
- 1. Implementing Advanced FSM Software
- 2. Standardizing Work Processes
- 3. Investing in Continuous Training and Certification
- 4. Implementing Quality Control Measures
- 5. Leveraging Technology for Data Management
- Conclusion
The Importance of Field Service Management in NDT
Non-Destructive Testing is a critical process used across various industries, including aerospace, automotive, energy, and manufacturing. It involves examining materials and components to detect defects, flaws, or changes in properties without altering the object being tested. This method is preferred over destructive testing as it saves time and resources while providing valuable insights into material integrity.
Field Service Management is essential for NDT companies because it enables them to coordinate and manage their mobile workforce effectively. With FSM systems, NDT technicians can be dispatched efficiently to client sites, ensuring timely completion of inspections and tests. This approach also helps in maintaining consistency in service quality across all locations.
Challenges Faced by Field Service Managers in NDT
Despite its importance, managing a field service operation for NDT presents several challenges:
- Scheduling Complexity: Coordinating schedules for NDT technicians who may need to travel long distances to remote locations can be challenging.
- Equipment Maintenance: Specialized NDT equipment often requires regular calibration and maintenance, adding complexity to the FSM process.
- Skill Set Requirements: NDT technicians require specific training and certifications, making it difficult to find and retain qualified personnel.
- Data Management: Collecting and analyzing data from various NDT techniques can be overwhelming, especially when dealing with large-scale projects.
- Regulatory Compliance: NDT services must adhere to strict regulations and standards, requiring careful management of documentation and certification processes.
Strategies for Effective Field Service Management in NDT
To overcome the challenges mentioned above, field service managers in the NDT industry employ several strategies:
1. Implementing Advanced FSM Software
Modern FSM software solutions offer powerful features specifically designed for NDT operations:
- Real-time scheduling and dispatch capabilities
- Automated work order generation based on client requests
- Integration with GPS tracking for accurate location monitoring
- Mobile apps for technicians to access job details and report findings directly from the field
These tools help streamline operations, improve efficiency, and enhance communication between headquarters and field technicians.
2. Standardizing Work Processes
Developing standardized operating procedures ensures consistency across all NDT services:
- Creating detailed checklists for each type of inspection
- Establishing protocols for equipment setup and calibration
- Defining clear reporting formats for test results
Standardization reduces errors, improves quality control, and speeds up the overall inspection process.
3. Investing in Continuous Training and Certification
Maintaining a skilled workforce is crucial in the NDT industry:
- Regular workshops and seminars to keep technicians updated on latest techniques and technologies
- Mandatory refresher courses for all NDT methods
- Cross-training programs to broaden skill sets and increase versatility
This approach not only enhances the competence of the team but also contributes to employee satisfaction and retention.
4. Implementing Quality Control Measures
Ensuring high-quality NDT services is paramount:
- Conducting regular audits of inspection reports and test data
- Maintaining detailed records of equipment calibration and maintenance
- Implementing peer review processes for complex inspections
These measures help maintain the highest standards of accuracy and reliability in NDT services.
5. Leveraging Technology for Data Management
Advanced technology plays a significant role in managing the vast amounts of data generated in NDT operations:
- Utilizing cloud-based storage solutions for secure data backup and sharing
- Implementing data analytics tools to identify trends and patterns in inspection results
- Developing custom dashboards for real-time monitoring of project progress and resource allocation
By leveraging these technological advancements, NDT companies can make data-driven decisions and optimize their operations more effectively.
Conclusion
Field Service Management is a critical component of successful Non-Destructive Testing operations. By implementing advanced FSM software, standardizing work processes, investing in continuous training, implementing robust quality control measures, and leveraging technology for data management, field service managers in the NDT industry can overcome challenges and deliver high-quality services efficiently.
As technology continues to evolve, FSM solutions will likely incorporate even more advanced features tailored specifically for NDT operations. This may include augmented reality tools for virtual inspections, artificial intelligence for predictive maintenance, and blockchain technology for secure data storage and transmission.
In conclusion, field service managers in the NDT industry must stay adaptable, embrace new technologies, and continuously refine their management strategies to meet the evolving demands of this specialized field. By doing so, they can ensure that their companies remain competitive in the ever-growing market for non-destructive testing services.