Field Service Management for Smart Locker-Based Parts Delivery
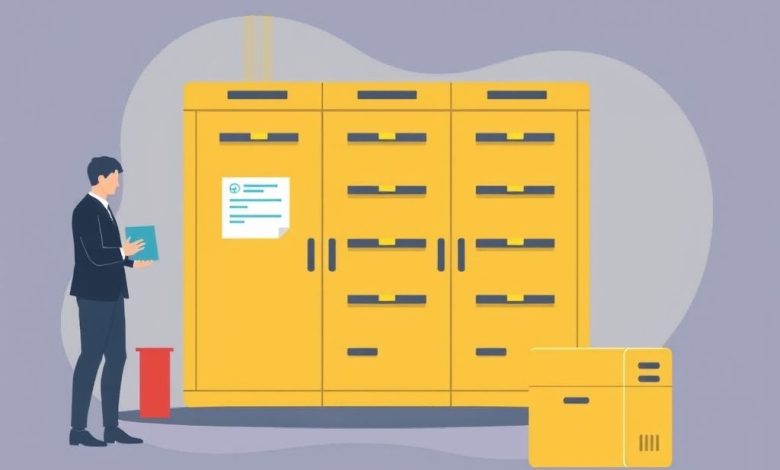
Field Service Management for Smart Locker-Based Parts Delivery
Introduction
Field service management (FSM) has evolved significantly in recent years, driven by technological advancements and changing customer expectations. One innovative approach that is gaining traction in the industry is the use of smart lockers for parts delivery in field service operations. This article explores the concept of FSM integrated with smart locker-based parts delivery systems, examining its benefits, implementation challenges, and potential impact on field service management practices.
The Rise of Smart Lockers in Field Service
Smart lockers have been increasingly adopted across various industries as a secure, efficient, and cost-effective solution for package delivery and retrieval. In the context of field service management, smart lockers offer a unique opportunity to streamline parts delivery processes, enhancing both operational efficiency and customer satisfaction.
Key features of smart lockers relevant to field service management include:
- Automated package sorting and storage
- Real-time inventory tracking
- Secure access control through biometric authentication or QR codes
- Integration with mobile apps for easy ordering and retrieval
By leveraging these capabilities, field service organizations can optimize their parts delivery processes, leading to improved response times, reduced costs, and enhanced overall service quality.
Benefits of Smart Locker-Based Parts Delivery
Implementing smart locker systems for parts delivery offers several advantages to field service organizations:
- Increased Efficiency
Smart lockers eliminate the need for manual handling of packages, reducing labor costs associated with receiving and storing parts. Technicians can quickly retrieve the required components without waiting for manual delivery or searching through physical storage areas.
2. Improved Inventory Management
Real-time tracking of inventory within smart lockers allows for better stock management. Organizations can easily monitor part availability, automate reordering processes, and prevent stockouts.
3. Enhanced Customer Experience
Customers benefit from faster access to replacement parts, reducing downtime and improving overall satisfaction. Smart lockers provide a convenient, self-service option for customers who prefer not to interact directly with technicians.
4. Scalability and Flexibility
As businesses grow or expand into new locations, smart locker systems can be easily replicated and integrated into existing infrastructure, offering greater flexibility compared to traditional warehousing solutions.
5. Data Analytics and Insights
Smart locker systems generate valuable data on usage patterns, which can be leveraged to improve operational efficiency and make informed decisions about inventory management and resource allocation.
Implementation Challenges
While the benefits of smart locker-based parts delivery are significant, implementing such a system comes with several challenges:
- Initial Investment Costs
Deploying smart locker systems requires a substantial upfront investment in hardware, software, and integration efforts. This can be a barrier for smaller organizations or those with limited budgets.
2. Technical Complexity
Integrating smart lockers with existing field service management systems and ensuring seamless communication between different components can be technically demanding. It may require significant IT resources and expertise.
3. Security Concerns
Ensuring the security of stored parts and maintaining access controls is crucial. Organizations must implement robust security measures to protect sensitive equipment and proprietary parts.
4. Training and Adoption
Technicians and other staff members may need training to effectively utilize the smart locker system, which can be time-consuming and costly.
5. Maintenance and Support
Regular maintenance of smart lockers and addressing any issues promptly is essential to ensure continuous operation. This adds another layer of responsibility to the organization’s IT support team.
Case Study: Implementing Smart Lockers in a Field Service Organization
To illustrate the practical application of smart locker-based parts delivery in field service management, let’s consider a hypothetical case study:
XYZ Corporation, a provider of HVAC services, decided to implement smart lockers for parts delivery to enhance their field service operations. They chose a cloud-based smart locker solution that could integrate with their existing FSM software.
Implementation process:
- Assessment and Planning
XYZ conducted a thorough assessment of their current parts delivery processes and identified areas for improvement. They determined that smart lockers could significantly reduce handling time and improve inventory management.
2. Hardware Installation
Smart lockers were installed at strategic locations near their main service centers and in some field locations. The lockers were equipped with RFID technology for easy tracking and retrieval.
3. Integration with Existing Systems
XYZ worked closely with their IT team to integrate the smart locker system with their FSM software. This allowed for seamless communication between the two systems, enabling real-time updates on part availability and technician requests.
4. Training and Rollout
Technicians and support staff received comprehensive training on using the smart locker system. A phased rollout approach was adopted, starting with a small pilot group before expanding to the entire organization.
5. Monitoring and Optimization
After the initial implementation, XYZ continuously monitored the performance of the smart locker system. They collected data on usage patterns, identified bottlenecks, and made necessary adjustments to optimize the system’s effectiveness.
Results after six months:
- Reduced average parts delivery time from 30 minutes to under 5 minutes
- Decreased labor costs associated with parts handling by 25%
- Improved first-time fix rate by 15% due to faster access to correct parts
- Received positive feedback from customers about improved service responsiveness
Conclusion
Field service management integrated with smart locker-based parts delivery represents a significant advancement in operational efficiency and customer satisfaction. By leveraging this technology, organizations can streamline their parts delivery processes, enhance inventory management, and ultimately deliver better service to their customers.
While challenges exist in implementing such a system, the benefits far outweigh the costs for many field service organizations. As the technology continues to evolve and become more accessible, we can expect to see wider adoption of smart locker systems across various industries.
For field service managers considering implementing smart locker-based parts delivery, it is crucial to conduct thorough assessments of their current processes, invest in proper training, and continuously monitor and optimize the system’s performance. By doing so, they can unlock the full potential of this innovative technology and take their field service operations to the next level.