Field Service Management in Agricultural Equipment Services Optimizing Farm Operations in the Digital Age
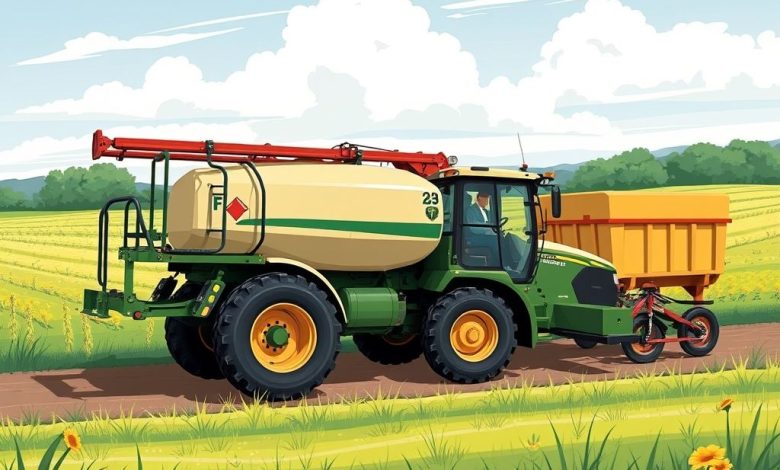
Introduction
Field Service Management (FSM) is a crucial aspect of modern agricultural equipment services. It encompasses the processes and technologies used to manage and optimize the delivery of maintenance, repair, and other services to customers’ farms and fields. In today’s fast-paced agricultural industry, efficient FSM can significantly improve operational efficiency, customer satisfaction, and overall business performance.
- The Importance of Field Service Management in Agriculture
- Key Components of Field Service Management Systems
- Scheduling and Dispatching
- Mobile Workforce Management
- Inventory and Parts Management
- Reporting and Analytics
- Implementing Field Service Management in Agricultural Equipment Services
- Case Study: Implementing FSM in a Large-Scale Agricultural Operation
- Conclusion
The Importance of Field Service Management in Agriculture
Agricultural equipment services face unique challenges compared to other industries. Farm operations often occur in remote areas, and equipment downtime can have severe consequences on crop yields and profitability. Effective FSM helps address these challenges by:
- Improving response times to equipment breakdowns
- Enhancing resource allocation and scheduling
- Streamlining communication between technicians and dispatchers
- Optimizing routes and reducing travel time
- Ensuring compliance with safety regulations and industry standards
Key Components of Field Service Management Systems
Modern FSM systems typically consist of several interconnected components:
Scheduling and Dispatching
This module handles the core function of assigning jobs to available technicians based on various factors such as:
- Job priority and urgency
- Technician skill sets and availability
- Vehicle location and status
- Customer preferences and history
Advanced scheduling algorithms can optimize route planning, minimize travel time, and ensure equitable distribution of workloads among technicians.
Mobile Workforce Management
Technicians in the field use mobile applications to:
- Access job details and instructions
- Update job statuses in real-time
- Capture electronic signatures from customers
- Scan barcodes for inventory management
- Take photos of completed work for quality assurance
These apps enable seamless communication between the office and the field, ensuring that all necessary information is readily available to technicians.
Inventory and Parts Management
Efficient inventory control is critical in agricultural equipment services due to the specialized nature of many parts. FSM systems help manage:
- Stock levels of common and less frequent parts
- Supplier relationships and pricing
- Warranty claims and returns
- Preventive maintenance schedules
Reporting and Analytics
Robust reporting capabilities allow businesses to gain valuable insights into their operations through:
- Performance metrics such as first-time fix rates and average response times
- Cost analysis of different service types and regions
- Customer satisfaction surveys and feedback
- Technician productivity and efficiency benchmarks
These analytics can inform strategic decisions, identify areas for improvement, and drive continuous optimization of the service delivery process.
Implementing Field Service Management in Agricultural Equipment Services
Adopting an FSM system requires careful consideration of several factors:
- Choose a solution that caters specifically to agricultural equipment services, rather than generic FSM platforms.
- Ensure compatibility with existing software and hardware infrastructure.
- Provide thorough training to all staff members who will interact with the new system.
- Plan for a gradual rollout to minimize disruption to ongoing operations.
- Establish clear policies and procedures for data privacy and security, especially when dealing with sensitive farm information.
- Regularly update and maintain the system to keep pace with evolving technological advancements and changing business needs.
Case Study: Implementing FSM in a Large-Scale Agricultural Operation
XYZ Farm Equipment Services, a leading provider of agricultural machinery support, implemented a comprehensive FSM solution across its network of regional depots. The company serves over 10,000 farmers across three states, managing a fleet of more than 500 service vehicles.
Prior to implementation, XYZ faced challenges with inconsistent service quality, lengthy response times, and inefficient resource allocation. After deploying the FSM system, the company reported significant improvements:
- Average response time reduced by 30%
- First-time fix rate increased by 25%
- Overall customer satisfaction scores improved by 40%
- Operational costs decreased by 15% due to optimized routing and reduced vehicle idle time
Conclusion
Field Service Management plays a vital role in optimizing agricultural equipment services. By leveraging advanced technology and streamlined processes, businesses can enhance their competitiveness, improve customer satisfaction, and contribute to the long-term sustainability of farming operations.
As the agricultural sector continues to evolve, embracing innovative FSM solutions will be crucial for maintaining a competitive edge in this dynamic industry. Whether you’re a small-scale operator or a large agricultural machinery provider, implementing a robust FSM system can significantly boost your service delivery capabilities and position your business for future success in the rapidly changing landscape of agricultural equipment services.