Field Service Management for Industrial Park Infrastructure
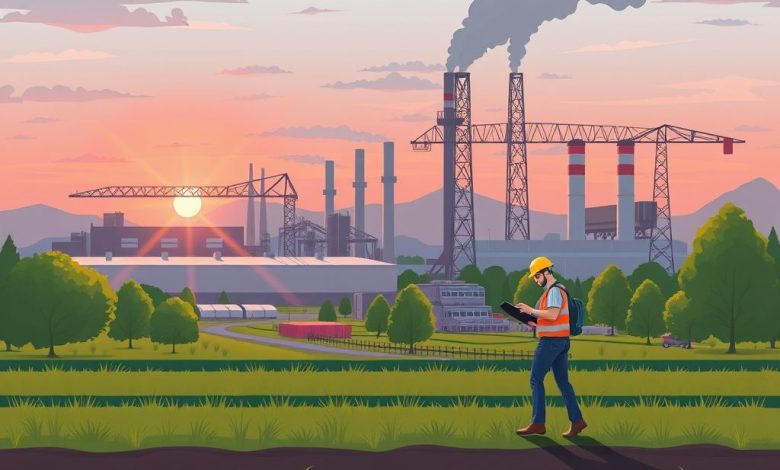
Field Service Management for Industrial Park Infrastructure
Introduction
Industrial parks play a crucial role in modern economies, serving as hubs for manufacturing, logistics, and various industries. These complexes require efficient management of infrastructure maintenance to ensure smooth operations and minimize downtime. Field service management (FSM) has emerged as a vital tool for industrial park operators to streamline maintenance processes, improve efficiency, and enhance overall performance.
This article explores the concept of field service management within the context of industrial park infrastructure. We will examine the key components of FSM systems, their benefits, challenges, and best practices for implementation in industrial settings.
Components of Field Service Management Systems
A robust FSM system typically consists of several interconnected modules:
- Work Order Management
- Centralized platform for creating, assigning, and tracking work orders
- Automated scheduling based on priority and resource availability
2. Inventory Management
- Real-time tracking of equipment and spare parts
- Automatic alerts for low stock levels
3. Mobile Field Operations
- Dedicated mobile apps for technicians to access job details and update status
- GPS tracking for real-time location monitoring
4. Customer Relationship Management (CRM)
- Integration with customer databases for historical records and preferences
- Automated communication tools for scheduling and updates
5. Reporting and Analytics
- Customizable dashboards for visualizing key metrics
- Performance insights for continuous improvement
Benefits of Implementing Field Service Management in Industrial Parks
Implementing an FSM system in industrial parks offers numerous advantages:
- Improved Efficiency
- Streamlined workflows reduce response times and increase first-time fix rates
- Automated scheduling optimizes resource allocation
2. Enhanced Customer Satisfaction
- Transparent communication through dedicated portals or mobile apps
- Predictive maintenance reduces unexpected outages
3. Cost Reduction
- Reduced travel time and fuel consumption
- Minimized inventory holding costs through optimized stock levels
4. Data-driven Decision Making
- Access to real-time operational data for strategic planning
- Identification of trends and patterns in maintenance needs
Challenges in Implementing Field Service Management
While FSM systems offer significant benefits, there are also challenges to consider:
- Initial Investment Costs
- High upfront expenses for software, hardware, and training
- Potential disruption during transition from traditional methods
2. Technological Adoption
- Resistance to change among older staff members
- Need for ongoing training and support
3. Data Security Concerns
- Protection of sensitive operational and customer data
- Compliance with industry-specific regulations
4. Integration Complexity
- Seamless integration with existing ERP and CRM systems
- Potential conflicts with legacy software
Best Practices for Implementing Field Service Management in Industrial Parks
To maximize the effectiveness of FSM systems in industrial parks, consider the following best practices:
- Conduct Thorough Needs Assessment
- Identify specific pain points and goals before selecting a solution
- Involve all stakeholders in the decision-making process
2. Provide Comprehensive Training
- Offer both technical and soft skills training for all users
- Regular refresher sessions to maintain proficiency
3. Start Small and Scale Up
- Begin with a pilot project to test the system
- Gradually expand coverage across the industrial park
4. Foster a Culture of Continuous Improvement
- Regularly review and refine processes
- Encourage feedback from end-users and customers
5. Ensure Data Privacy and Security
- Implement robust security measures and encryption protocols
- Conduct regular audits and penetration testing
6. Leverage IoT Technologies
- Integrate Internet of Things devices for predictive maintenance
- Analyze sensor data to optimize maintenance schedules
7. Optimize Scheduling Algorithms
- Utilize advanced algorithms for dynamic scheduling
- Consider factors like technician skill sets and vehicle locations
8. Implement Quality Assurance Processes
- Establish clear SLAs and KPIs for service quality
- Conduct regular audits and performance reviews
Conclusion
Field service management has revolutionized the way industrial parks manage their infrastructure maintenance. By implementing a comprehensive FSM system, operators can significantly improve efficiency, reduce costs, and enhance customer satisfaction. While challenges exist, the benefits far outweigh the drawbacks for forward-thinking industrial park managers.
As technology continues to evolve, it’s essential for field service managers to stay adaptable and embrace innovative solutions. The future of industrial park maintenance lies in smart, connected systems that leverage AI, IoT, and big data analytics to create truly optimized operations.
By investing in field service management, industrial parks can position themselves at the forefront of efficient infrastructure management, ensuring they remain competitive in today’s fast-paced business environment.