Field Service Management for Safety Check Automation
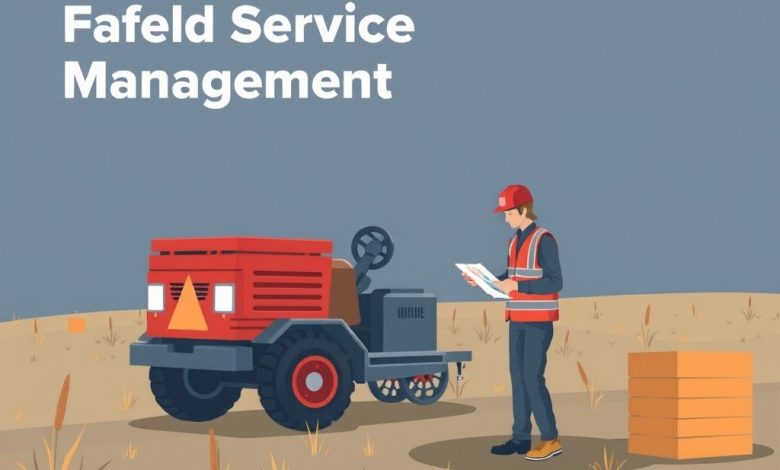
Field Service Management for Safety Check Automation
- Introduction
- Key Components of Field Service Management for Safety Check Automation
- Benefits of Implementing Field Service Management for Safety Check Automation
- Challenges in Implementing Field Service Management for Safety Check Automation
- Best Practices for Implementing Field Service Management for Safety Check Automation
- Conclusion
Introduction
Field service management (FSM) has become increasingly crucial in modern industries, particularly when it comes to ensuring safety checks automation. As technology advances, companies are leveraging various tools and strategies to streamline their operations while prioritizing worker safety. This article will explore the concept of FSM in relation to safety check automation, its benefits, challenges, and best practices.
The Evolution of Field Service Management
Field service management has undergone significant transformations over the years. From traditional paper-based systems to sophisticated digital platforms, FSM has evolved to meet the changing needs of businesses and workers alike. The integration of technology has enabled real-time tracking, efficient scheduling, and improved communication between dispatchers and technicians.
Safety check automation, as part of this evolution, has emerged as a critical component in maintaining workplace safety standards. By automating routine safety inspections and checks, organizations can reduce human error, ensure consistency across all locations, and allocate resources more effectively.
Key Components of Field Service Management for Safety Check Automation
- **Remote Monitoring**
Remote monitoring is a cornerstone of safety check automation in field service management. This technology allows supervisors to track worker activities in real-time, even when they are not physically present at the job site.
Key features of remote monitoring include:
- Live video streaming from wearable devices or mobile cameras
- GPS tracking of technician locations
- Environmental hazard detection (e.g., gas leaks, extreme temperatures)
By implementing remote monitoring, companies can significantly enhance safety protocols and respond quickly to potential hazards.
2. **Predictive Maintenance**
Predictive maintenance is another crucial aspect of FSM for safety check automation. This approach uses data analytics and machine learning algorithms to predict equipment failures before they occur.
Benefits of predictive maintenance include:
- Reduced downtime and increased operational efficiency
- Extended lifespan of equipment through proactive maintenance
- Improved safety by identifying potential hazards early
Implementing a robust predictive maintenance program can help prevent accidents caused by malfunctioning equipment and ensure a safer work environment.
3. **IoT Integration**
Internet of Things (IoT) technology plays a vital role in safety check automation within field service management. IoT devices can be deployed at various points throughout a facility or job site to monitor conditions and alert workers to potential dangers.
Examples of IoT applications in FSM include:
- Smart sensors detecting hazardous materials or gases
- Wearable devices tracking worker vital signs and environmental exposure
- Automated inventory management systems preventing stockouts and oversupply issues
The integration of IoT devices enhances situational awareness and enables rapid response to safety concerns.
4. **Mobile Applications**
Mobile applications have revolutionized field service management, particularly in the context of safety check automation. These apps allow technicians to perform safety checks, report incidents, and communicate with dispatchers directly from the field.
Key features of mobile apps for FSM include:
- Digital forms for standardized safety check reporting
- Real-time push notifications for urgent alerts
- Integration with other FSM software for seamless workflow
Mobile apps contribute to faster incident response times and ensure that safety information is captured consistently across all job sites.
Benefits of Implementing Field Service Management for Safety Check Automation
The implementation of FSM for safety check automation offers numerous advantages to organizations:
- **Improved Safety Standards**: By automating routine checks and monitoring worker activities, companies can maintain higher safety standards across all operations.
- **Increased Efficiency**: Streamlined processes and real-time data analysis enable faster decision-making and resource allocation.
- **Cost Reduction**: Preventive measures and reduced downtime lead to lower operational costs and improved bottom-line performance.
- **Enhanced Customer Satisfaction**: Timely completion of jobs and improved safety protocols contribute to higher customer satisfaction scores.
- **Compliance with Regulations**: Automated safety checks ensure consistent adherence to industry regulations and standards.
Challenges in Implementing Field Service Management for Safety Check Automation
Despite the numerous benefits, there are several challenges that organizations may face when implementing FSM for safety check automation:
- **Initial Investment Costs**: The setup and deployment of advanced technologies require significant upfront investments.
- **Data Privacy Concerns**: Collecting and storing sensitive safety data raises privacy considerations that must be addressed.
- **Technological Complexity**: Integrating various systems and ensuring interoperability can be technically challenging.
- **Resistance to Change**: Some employees may resist adopting new technologies and workflows.
- **Cybersecurity Risks**: Connected devices and cloud-based systems introduce potential cybersecurity vulnerabilities.
Best Practices for Implementing Field Service Management for Safety Check Automation
To overcome the challenges and maximize the benefits of FSM for safety check automation, consider the following best practices:
- **Phased Implementation**: Roll out new technologies gradually, starting with pilot programs and expanding to larger-scale deployments.
- **Employee Training**: Provide comprehensive training to ensure all staff members understand and can effectively use new systems and procedures.
- **Regular Audits**: Conduct regular audits to ensure compliance with safety protocols and identify areas for improvement.
- **Continuous Feedback Mechanisms**: Establish open channels for workers to provide feedback on the effectiveness of new systems and suggest improvements.
- **Integration with Existing Systems**: Ensure seamless integration with current FSM software and other business systems to minimize disruption.
Conclusion
Field service management for safety check automation represents a significant advancement in workplace safety protocols. By leveraging technologies such as remote monitoring, predictive maintenance, IoT integration, and mobile applications, organizations can enhance their safety standards while improving operational efficiency.
While challenges exist, the benefits of implementing FSM for safety check automation far outweigh the costs. As technology continues to evolve, it is crucial for field service managers to stay informed about emerging trends and best practices in this field.
By embracing these innovations, companies can create safer work environments, reduce risks, and contribute to a culture of safety excellence throughout their operations.