Field Service Management with Asset Tracking Optimizing Operations and Enhancing Customer Experience
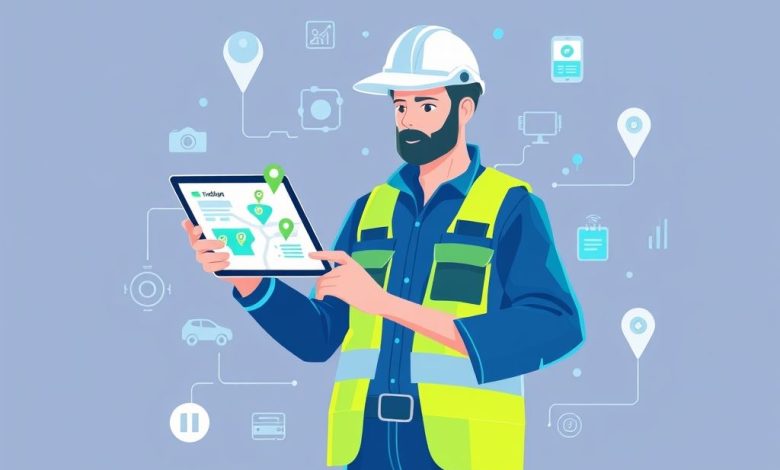
Introduction
Field Service Management (FSM) is a critical component of many businesses, particularly in industries such as HVAC, electrical work, plumbing, and home maintenance. It involves managing and coordinating the activities of technicians who provide services outside of a traditional office environment. In recent years, the integration of asset tracking technology has revolutionized how FSM operates, enhancing efficiency, reducing costs, and improving customer satisfaction.
This article will explore the concept of Field Service Management with Asset Tracking, its benefits, challenges, and best practices. We’ll delve into the technologies used, case studies, and future trends in this rapidly evolving field.
- What is Field Service Management?
- The Role of Asset Tracking in Field Service Management
- Key Technologies Used in Field Service Management with Asset Tracking
- Benefits of Implementing Field Service Management with Asset Tracking
- Challenges in Implementing Field Service Management with Asset Tracking
- Best Practices for Implementing Field Service Management with Asset Tracking
- Case Study: Utility Company Improves Response Times with FSM and Asset Tracking
- Conclusion
What is Field Service Management?
Field Service Management refers to the processes and systems used to manage and coordinate the activities of field workers or technicians. These individuals travel to customers’ locations to perform various tasks such as repairs, installations, and maintenance. Effective FSM ensures that:
- Jobs are scheduled efficiently
- Technicians have the necessary tools and equipment
- Customer expectations are met
- Data is collected and analyzed for continuous improvement
The Role of Asset Tracking in Field Service Management
Asset tracking is the process of monitoring the location, status, and condition of physical assets over time. When integrated with Field Service Management, it provides real-time visibility into the whereabouts and utilization of company-owned assets. This technology offers numerous advantages:
- Improved inventory management
- Enhanced job scheduling and optimization
- Reduced equipment loss or theft
- Better resource allocation
- Increased operational efficiency
Key Technologies Used in Field Service Management with Asset Tracking
Several technologies play crucial roles in modern FSM systems:
Mobile Applications
Mobile apps allow technicians to access job schedules, customer information, and diagnostic tools directly from their smartphones or tablets. They can also use these devices to scan barcodes, capture signatures, and update job statuses in real-time.
GPS Tracking
Global Positioning System (GPS) technology enables real-time location tracking of vehicles and equipment. This feature helps dispatchers optimize routes, reduce fuel consumption, and improve response times.
Internet of Things (IoT) Devices
IoT sensors embedded in equipment can monitor vital signs, detect anomalies, and predict potential failures. This data allows for proactive maintenance and reduces unexpected breakdowns.
Cloud-Based Software
Centralized cloud platforms store all FSM data, providing secure access to authorized personnel. They offer features like automated scheduling, resource allocation, and performance analytics.
Benefits of Implementing Field Service Management with Asset Tracking
The integration of asset tracking technology into FSM systems brings numerous benefits:
- Increased Efficiency: Real-time tracking and optimized routing lead to faster job completion and improved productivity.
- Cost Reduction: Minimized idle time, reduced fuel consumption, and lower equipment replacement costs contribute to overall cost savings.
- Enhanced Customer Experience: Faster response times, accurate arrival estimates, and transparent communication lead to higher customer satisfaction.
- Improved Resource Allocation: Accurate tracking of available resources allows for better job scheduling and allocation.
- Data-Driven Decision Making: Access to historical and real-time data enables more informed business decisions.
- Increased Safety: GPS tracking improves emergency response times and enhances safety measures for field workers.
Challenges in Implementing Field Service Management with Asset Tracking
While the benefits are significant, there are several challenges to consider when implementing FSM with asset tracking:
- Initial Investment Costs: The setup and implementation of advanced FSM systems require substantial upfront investment in hardware, software, and training.
- Data Privacy Concerns: Ensuring the security and privacy of customer and employee data becomes increasingly important with increased digitalization.
- Technological Complexity: Integrating various technologies (mobile apps, GPS, IoT, etc.) can be challenging and may require specialized IT support.
- Change Management: Adopting new systems often requires cultural changes within organizations, which can be difficult to implement.
- Connectivity Issues: Reliability of connectivity, especially in remote areas, can impact system effectiveness.
Best Practices for Implementing Field Service Management with Asset Tracking
To ensure successful implementation and maximize benefits, consider the following best practices:
- Conduct thorough needs analysis before selecting any solution.
- Provide comprehensive training to all staff members involved in the new system.
- Start with a pilot program to test the system in a controlled environment.
- Regularly review and update the system based on feedback and changing business needs.
- Ensure robust data security measures are in place.
- Integrate the new system with existing workflows and processes.
- Monitor key performance indicators (KPIs) regularly to measure success.
- Foster a culture of innovation and continuous improvement among employees.
Case Study: Utility Company Improves Response Times with FSM and Asset Tracking
A large utility company serving a metropolitan area implemented a comprehensive FSM system with asset tracking capabilities. Prior to implementation, they experienced frequent delays due to inefficient route planning and lack of real-time tracking.
After deploying the new system, the company observed significant improvements:
- Average response time decreased by 30%
- Fuel consumption per technician dropped by 25%
- Equipment downtime was reduced by 40%
- Overall customer satisfaction scores increased by 15%
These results were achieved through optimized routing algorithms, real-time tracking of vehicles and equipment, and predictive maintenance based on sensor data from IoT devices.
Conclusion
Field Service Management with Asset Tracking represents a powerful combination of technologies designed to enhance operational efficiency, reduce costs, and improve customer satisfaction. As the industry continues to evolve, we can expect further advancements in areas such as artificial intelligence, augmented reality, and blockchain technology.
For field service managers looking to stay competitive in today’s fast-paced market, embracing these innovations can provide a significant edge. By leveraging the power of FSM and asset tracking, companies can transform their operations, deliver superior service quality, and build long-lasting relationships with their customers.
Remember, while technology plays a crucial role, human expertise remains essential. Combine cutting-edge solutions with skilled professionals who understand the nuances of field service work, and you’ll be well-positioned to thrive in this dynamic industry.