Field Service Management for Greenhouse Equipment Support
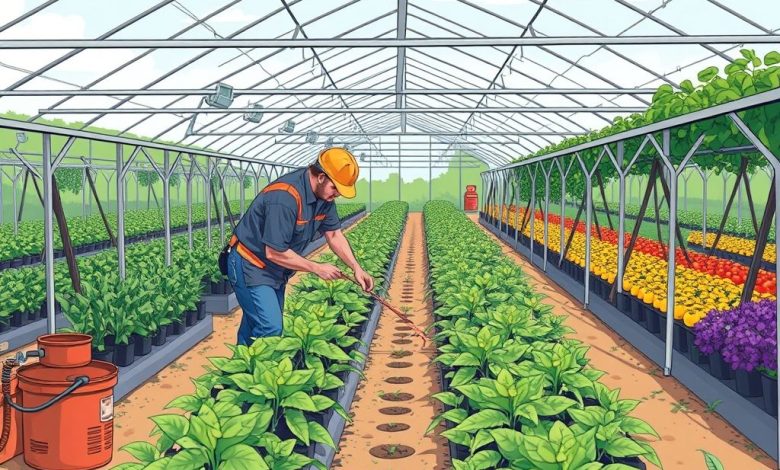
Field Service Management for Greenhouse Equipment Support
- Introduction
- Importance of FSM in Greenhouse Equipment Support
- Key Components of Field Service Management for Greenhouses
- Asset Tracking and Inventory Management
- Scheduling and Dispatch Optimization
- Work Order Management
- Customer Relationship Management (CRM)
- Training and Certification Programs
- Best Practices for Implementing FSM in Greenhouse Operations
- Challenges in Field Service Management for Greenhouses
- Conclusion
Introduction
Field service management (FSM) plays a crucial role in maintaining and supporting greenhouse equipment. Greenhouses require specialized care and attention to ensure optimal growing conditions for plants. Effective FSM strategies help maintain the integrity of greenhouse structures, control environmental factors, and ensure proper functioning of equipment.
Importance of FSM in Greenhouse Equipment Support
Field service management is essential for several reasons:
- Timely maintenance: Regular checks and repairs prevent equipment failures, reducing downtime and ensuring continuous operation.
- Cost-effective operations: Preventive maintenance reduces long-term costs associated with frequent replacements and emergency repairs.
- Improved efficiency: Well-maintained equipment operates more efficiently, leading to better crop yields and reduced energy consumption.
- Enhanced safety: Properly maintained equipment minimizes risks to personnel working within the greenhouse environment.
Key Components of Field Service Management for Greenhouses
Asset Tracking and Inventory Management
Implementing an asset tracking system helps manage inventory levels and locate specific items quickly. This includes:
- RFID tags for easy identification of equipment parts
- Barcode scanning for efficient inventory checks
- Real-time tracking of equipment location and status
Scheduling and Dispatch Optimization
Effective scheduling ensures prompt response times and optimal resource allocation:
- Automated scheduling software for efficient route planning
- Integration with GPS systems for real-time location tracking
- Prioritization of high-priority tasks based on urgency and impact
Work Order Management
Streamlined work order processes improve operational efficiency:
- Digital work orders for quick creation and assignment
- Mobile apps for technicians to access job details and update statuses
- Customizable templates for standardizing repair procedures
Customer Relationship Management (CRM)
Maintaining strong relationships with customers is crucial:
- Centralized customer database for easy access to information
- Automated reminders for scheduled maintenance appointments
- Feedback mechanisms for continuous improvement
Training and Certification Programs
Investing in employee development enhances overall performance:
- Regular training sessions on new equipment and techniques
- Certification programs for specialized skills
- Cross-training to increase versatility among staff
Best Practices for Implementing FSM in Greenhouse Operations
Regular Maintenance Checks
Conduct routine inspections to identify potential issues early:
- Daily visual inspections of equipment and structures
- Weekly checks of temperature controls and irrigation systems
- Monthly assessments of electrical components and mechanical parts
Documentation and Record Keeping
Maintain comprehensive records for improved decision-making:
- Detailed logs of all maintenance activities
- Historical data analysis for identifying recurring issues
- Compliance documentation for regulatory requirements
Continuous Improvement
Encourage a culture of ongoing learning and innovation:
- Regular reviews of FSM processes and their effectiveness
- Implementation of new technologies and tools
- Collaboration with industry experts and peers to share best practices
Challenges in Field Service Management for Greenhouses
Despite the importance of FSM, several challenges exist:
- Remote locations: Accessibility issues may delay response times
- Specialized knowledge: Technicians require expertise in both general maintenance and greenhouse-specific equipment
- Weather conditions: Extreme temperatures and weather events can affect equipment performance and technician safety
Conclusion
Field service management plays a vital role in supporting greenhouse equipment. By implementing robust FSM strategies, including asset tracking, scheduling optimization, work order management, CRM systems, and training programs, greenhouses can maintain peak operational efficiency while minimizing costs and improving safety. As technology continues to evolve, FSM solutions will become increasingly sophisticated, enabling even more effective support for this critical infrastructure in agriculture.