Field Service Management for Cold Room Compliance
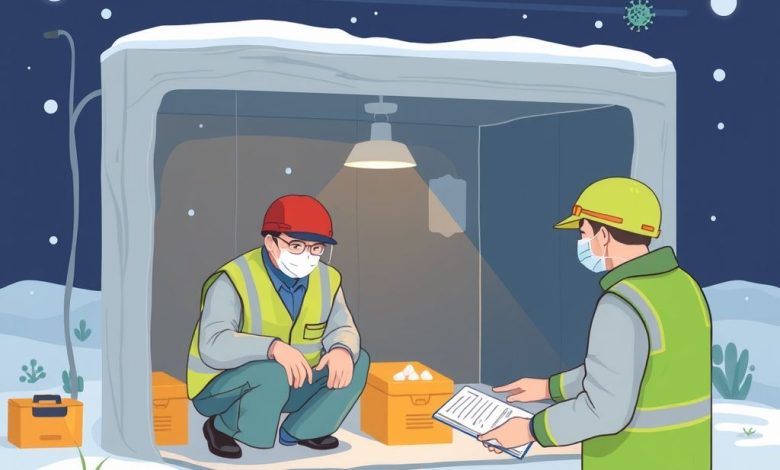
Introduction
Cold room compliance is crucial in various industries such as pharmaceuticals, biotechnology, and food processing. Maintaining proper temperature control within cold rooms ensures the safety and efficacy of stored products. However, managing cold rooms effectively requires more than just maintaining the correct temperature; it involves a comprehensive approach to field service management.
This article explores the importance of field service management in ensuring cold room compliance. We will discuss the key aspects of cold room maintenance, the role of field service technicians, and best practices for implementing effective field service management systems.
- The Importance of Cold Room Compliance
- Role of Field Service Technicians
- Best Practices for Field Service Management
- Implement a Centralized Field Service Management System
- Invest in Mobile Technology
- Develop Comprehensive Training Programs
- Establish Clear Communication Channels
- Conduct Regular Audits and Quality Assurance Checks
- Challenges in Field Service Management for Cold Room Compliance
- Conclusion
The Importance of Cold Room Compliance
Cold rooms are used to store sensitive materials that require precise temperature control. These rooms are typically maintained between 2°C and 8°C (36°F to 46°F), depending on the specific requirements of the stored items. Non-compliance with temperature regulations can lead to several issues:
- Product degradation: Many pharmaceuticals and biological samples lose potency when exposed to temperatures outside the recommended range.
- Contamination risk: Bacteria and other microorganisms thrive in warmer temperatures, potentially contaminating stored products.
- Regulatory penalties: Failure to maintain proper temperature control may result in fines and legal consequences.
- Loss of business reputation: Companies found non-compliant with cold room standards may face public scrutiny and loss of customer trust.
Given these risks, it is essential for organizations to implement robust field service management strategies to ensure cold room compliance.
Role of Field Service Technicians
Field service technicians play a critical role in maintaining cold room compliance. Their responsibilities include:
- Regular temperature monitoring: Technicians must check temperature readings at multiple points within the cold room to ensure uniformity.
- Equipment maintenance: They perform routine checks on refrigeration systems, including compressors, evaporators, and condensers.
- Leak detection: Technicians inspect for any signs of refrigerant leaks, which can compromise the effectiveness of the cooling system.
- Alarm system testing: They verify that temperature alarms are functioning correctly to alert staff of potential issues.
- Documentation: Field service technicians maintain detailed records of their visits, including temperature readings, equipment status, and any necessary repairs or adjustments.
Best Practices for Field Service Management
To ensure effective field service management for cold room compliance, organizations should consider the following best practices:
Implement a Centralized Field Service Management System
A centralized system allows for better tracking of service requests, technician schedules, and job completion status. This helps in:
- Improving response times to temperature-related issues
- Ensuring consistent follow-up visits
- Providing real-time updates to stakeholders
Invest in Mobile Technology
Mobile devices equipped with specialized software enable field service technicians to:
- Access critical information about the cold room and its contents
- Record temperature readings directly on-site
- Submit work orders electronically for immediate processing
Develop Comprehensive Training Programs
Field service technicians require ongoing training to stay updated on:
- Latest refrigeration technologies
- Regulatory changes affecting cold room requirements
- Best practices for maintaining specific types of stored products
Establish Clear Communication Channels
Effective communication is crucial between field service teams, operations staff, and management. This includes:
- Regular status updates on cold room conditions
- Prompt notification of any deviations from set temperatures
- Clear escalation procedures for critical issues
Conduct Regular Audits and Quality Assurance Checks
Periodic audits help identify areas for improvement in the field service management process. These may include:
- Reviewing temperature logs for consistency
- Assessing the efficiency of the current maintenance schedule
- Evaluating the effectiveness of alarm systems
Challenges in Field Service Management for Cold Room Compliance
Despite the importance of field service management for cold room compliance, several challenges exist:
- Remote monitoring limitations: In some cases, remote monitoring may not be sufficient to detect all temperature fluctuations.
- Technician availability: Ensuring adequate coverage during off-hours or holidays can be challenging.
- Cost considerations: Maintaining high-quality field service teams and advanced technology can be expensive.
- Balancing proactive and reactive maintenance: Finding the right balance between scheduled maintenance and responding to urgent issues can be difficult.
Conclusion
Field service management plays a vital role in ensuring cold room compliance. By implementing robust systems, investing in appropriate technology, and developing comprehensive training programs, organizations can significantly reduce the risk of non-compliance and associated consequences.
As regulations continue to evolve and the stakes remain high, it is essential for companies to prioritize field service management for cold room compliance. By doing so, they not only protect their products but also safeguard their reputation and business continuity.
In the ever-changing landscape of pharmaceuticals, biotechnology, and food processing, staying ahead of compliance requirements through effective field service management is no longer optional—it’s imperative.