Field Service Management for Cold Chain Compliance
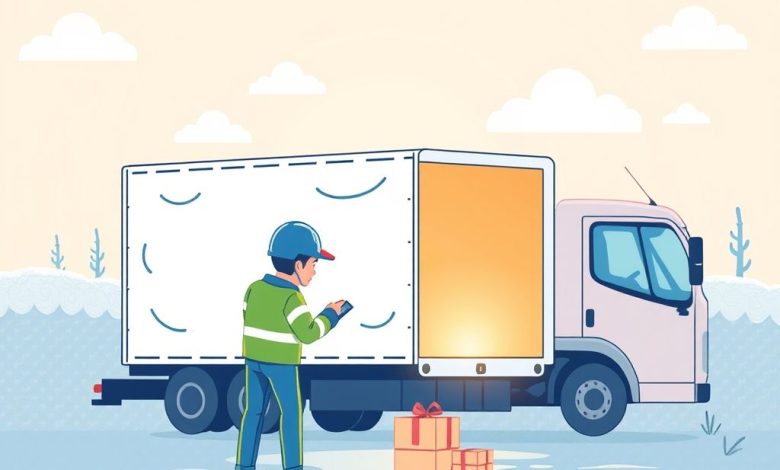
Field Service Management for Cold Chain Compliance
Introduction
Cold chain compliance is crucial in maintaining the integrity and safety of temperature-sensitive goods throughout their lifecycle. As the demand for perishable products continues to grow, companies must ensure that their logistics and supply chain management practices adhere to strict regulations and industry standards. Field service management (FSM) plays a vital role in ensuring cold chain compliance, particularly when it comes to monitoring and maintaining proper temperatures during transportation and storage.
This article will explore the importance of FSM in cold chain compliance, highlighting the challenges faced by companies and the strategies they can employ to maintain compliance standards. We will examine the role of FSM software in streamlining operations, improving efficiency, and reducing costs associated with cold chain management.
The Importance of Cold Chain Compliance
Cold chain compliance refers to the adherence to regulations and guidelines that ensure the proper handling, storage, and transportation of temperature-sensitive goods. These products include pharmaceuticals, vaccines, blood products, and perishable foods, among others.
Maintaining cold chain compliance is critical for several reasons:
- Ensures product safety and efficacy
- Prevents spoilage and contamination
- Reduces liability risks associated with non-compliance
- Maintains customer trust and satisfaction
- Complies with regulatory requirements
Challenges in Cold Chain Management
Despite its importance, maintaining cold chain compliance presents several challenges:
- Temperature fluctuations during transportation
- Inadequate storage facilities
- Insufficient monitoring and tracking systems
- Lack of trained personnel
- High costs associated with maintaining cold chain infrastructure
These challenges can lead to product spoilage, recalls, and financial losses for companies.
Role of Field Service Management in Cold Chain Compliance
Field service management software has emerged as a crucial tool in ensuring cold chain compliance. FSM solutions provide real-time visibility into field operations, enabling companies to monitor temperature-sensitive goods throughout their journey.
Key features of FSM software relevant to cold chain compliance include:
- Real-time tracking and monitoring of shipments
- Automated alerts for temperature deviations
- Route optimization to minimize transit times
- Integration with temperature-controlled vehicles and storage units
- Reporting and analytics capabilities
By leveraging these features, companies can improve their ability to maintain cold chain compliance while reducing operational costs and improving efficiency.
Strategies for Maintaining Cold Chain Compliance
In addition to implementing FSM software, companies can employ several strategies to maintain cold chain compliance:
- Training and Certification:
- Ensure that all staff involved in handling temperature-sensitive goods undergo regular training on cold chain procedures
- Obtain certifications from recognized bodies (e.g., IATA CEIV Pharma)
2. Equipment Maintenance:
- Regularly inspect and maintain refrigerated vehicles and storage facilities
- Replace faulty equipment promptly to prevent temperature fluctuations
3. Quality Control Checks:
- Conduct regular quality control checks at various stages of transportation and storage
- Implement random sampling to detect any anomalies
4. Data Management:
- Maintain accurate records of shipment details, including temperatures logged during transit
- Use data analytics to identify trends and areas for improvement
5. Risk Assessment:
- Conduct regular risk assessments to identify potential vulnerabilities in the cold chain
- Develop contingency plans for unexpected events (e.g., power outages, traffic delays)
6. Partner Selection:
- Carefully select and vet third-party logistics providers who specialize in cold chain management
- Conduct audits of partner facilities to ensure they meet compliance standards
7. Technology Integration:
- Integrate FSM software with other supply chain management tools for seamless operation
- Utilize Internet of Things (IoT) devices for real-time monitoring of temperature-sensitive goods
Case Study: Improving Cold Chain Compliance with FSM Software
XYZ Pharmaceutical Company, a leading manufacturer of temperature-sensitive drugs, faced significant challenges in maintaining cold chain compliance. Their existing manual tracking system was prone to errors and lacked real-time visibility into shipments.
To address these issues, XYZ implemented a comprehensive FSM solution that integrated with their existing ERP system. The new software provided real-time tracking, automated alerts for temperature deviations, and route optimization capabilities.
Results after implementation:
- Reduced temperature deviation incidents by 75%
- Improved on-time delivery rate from 85% to 95%
- Decreased logistics costs by 20% through optimized routing
- Enhanced visibility into field operations, allowing for better decision-making
Conclusion
Field service management plays a critical role in ensuring cold chain compliance. By leveraging FSM software and implementing strategic practices, companies can significantly improve their ability to maintain compliance standards while enhancing operational efficiency and reducing costs.
As the demand for perishable products continues to grow, the importance of cold chain compliance will only increase. Companies must invest in robust FSM solutions and develop comprehensive strategies to address the unique challenges of managing temperature-sensitive goods.
By prioritizing cold chain compliance through FSM, companies can protect their reputation, ensure product safety, and remain competitive in an increasingly regulated industry.