Field Service Management for Brewery Equipment Maintenance
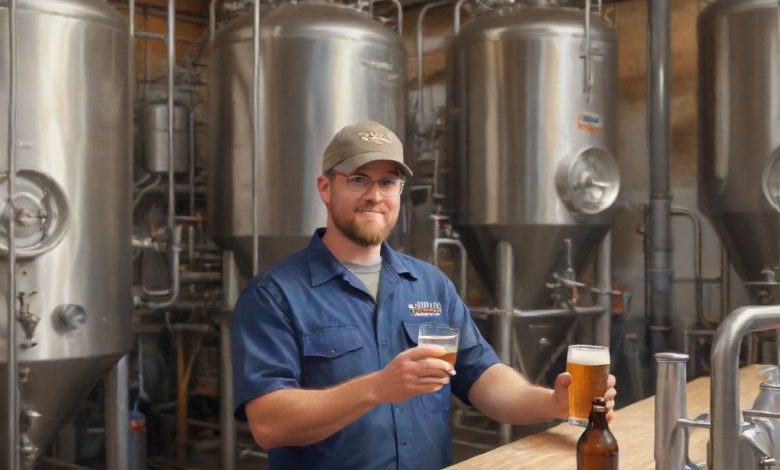
Introduction
Field Service Management (FSM) plays a crucial role in maintaining brewery equipment efficiently. As breweries continue to grow and expand their operations, effective FSM becomes increasingly important to ensure smooth production processes and minimize downtime. This article explores the importance of FSM in brewery equipment maintenance, its benefits, challenges, and best practices.
- The Importance of Field Service Management in Brewing Industry
- Benefits of Implementing Field Service Management Systems
- Challenges in Implementing Field Service Management
- Best Practices for Implementing Field Service Management in Breweries
- Start Small
- Invest in Proper Training
- Leverage Mobile Technology
- Integrate with Existing Systems
- Regularly Review and Refine
- Conclusion
The Importance of Field Service Management in Brewing Industry
Breweries rely heavily on specialized equipment for fermentation, brewing, packaging, and other processes. These machines require regular maintenance to function optimally and prevent costly breakdowns. Field Service Management systems help breweries manage their equipment maintenance more effectively by:
- Scheduling routine checks and maintenance tasks
- Tracking equipment performance and identifying potential issues early
- Assigning appropriate technicians based on skill sets and location
- Managing inventory of spare parts and consumables
- Providing real-time updates on maintenance activities
By implementing FSM, breweries can significantly reduce equipment failures, improve overall efficiency, and enhance customer satisfaction through consistent product quality.
Benefits of Implementing Field Service Management Systems
Implementing FSM systems offers numerous advantages for breweries:
Improved Efficiency
FSM allows breweries to streamline their maintenance operations by automating scheduling, assigning tasks, and tracking progress. This leads to faster response times and reduced downtime, resulting in increased productivity and profitability.
Enhanced Customer Satisfaction
With FSM, breweries can respond quickly to equipment issues, ensuring minimal disruption to production schedules. This translates to improved delivery timelines and higher-quality products, ultimately leading to increased customer satisfaction.
Cost Savings
Proactive maintenance strategies enabled by FSM can help breweries avoid expensive repairs and replacements. By addressing minor issues before they escalate, breweries can reduce maintenance costs and extend the lifespan of their equipment.
Better Resource Allocation
FSM provides valuable insights into equipment usage patterns and maintenance needs. This data helps breweries optimize resource allocation, assign the right personnel to specific tasks, and maintain the necessary inventory levels.
Challenges in Implementing Field Service Management
While FSM offers numerous benefits, breweries may face several challenges when implementing such systems:
Initial Investment Costs
Implementing a robust FSM system requires significant upfront investment in software, hardware, and training. This can be a barrier for smaller breweries with limited budgets.
Data Integration Issues
Integrating FSM data with existing brewery management systems can be challenging, especially for older legacy systems. This may require significant IT infrastructure changes.
Technological Complexity
FSM systems involve various technologies like mobile apps, cloud computing, and IoT devices. Ensuring all staff members are comfortable with these tools can be time-consuming and costly.
Resistance to Change
Some brewery employees may resist adopting new technology and processes. Changing established workflows and habits can be difficult and require strong leadership support.
Best Practices for Implementing Field Service Management in Breweries
To overcome the challenges and maximize the benefits of FSM, breweries should consider the following best practices:
Start Small
Begin with a pilot program involving a few key pieces of equipment. This allows breweries to test the system, identify any issues, and refine their approach before full-scale implementation.
Invest in Proper Training
Provide comprehensive training to all staff members who will use the FSM system. This includes both technical training for equipment operators and non-technical training for administrative staff.
Leverage Mobile Technology
Utilize mobile apps and tablets to enable technicians to access FSM systems remotely. This improves responsiveness and reduces paperwork errors.
Integrate with Existing Systems
Ensure seamless integration between the FSM system and other brewery management systems. This might require custom development or consulting with system integrators.
Regularly Review and Refine
Continuously monitor the effectiveness of the FSM system and gather feedback from users. Make adjustments as needed to optimize the system for the brewery’s specific needs.
Conclusion
Field Service Management is a powerful tool for breweries looking to optimize their equipment maintenance processes. By leveraging FSM systems, breweries can improve efficiency, enhance customer satisfaction, and reduce costs. While there are challenges to implementation, the long-term benefits make it an essential investment for breweries aiming to stay competitive in today’s fast-paced industry.
As the brewing industry continues to evolve, embracing advanced technologies like FSM will be crucial for breweries to maintain their edge in terms of productivity, quality, and customer service. By understanding the importance of FSM and implementing it effectively, breweries can ensure their equipment runs smoothly, their customers are satisfied, and their bottom line remains healthy.