Field Service Management with Preventive Task Forecasting Enhancing Operational Efficiency and Customer Satisfaction
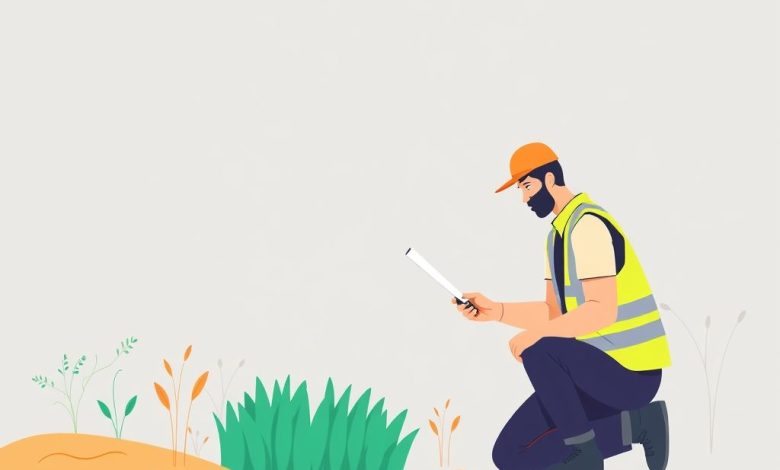
Introduction
Field Service Management (FSM) is a critical component of modern business operations, particularly in industries such as HVAC, electrical contracting, plumbing, and home maintenance. As companies strive to deliver exceptional customer service while optimizing resource allocation, FSM systems have evolved to incorporate advanced features like preventive task forecasting. This article explores the concept of FSM with a focus on preventive task forecasting, its benefits, implementation strategies, and best practices for field service managers.
- The Evolution of Field Service Management
- Preventive Task Forecasting in Field Service Management
- Benefits of Implementing Preventive Task Forecasting
- Implementation Strategies for Field Service Managers
- 1. Assess Current Operations
- 2. Choose the Right Technology
- 3. Train Your Team
- 4. Gradual Implementation
- 5. Continuous Monitoring and Improvement
- Best Practices for Field Service Managers
- Challenges and Considerations
- Conclusion
The Evolution of Field Service Management
Field Service Management has come a long way since its inception. From manual scheduling and paper-based work orders to sophisticated software solutions, the industry has witnessed significant technological advancements. Modern FSM systems now offer real-time tracking, automated dispatching, and data-driven decision making capabilities.
Key Components of Field Service Management
- Customer Relationship Management (CRM)
- Work Order Management
- Resource Allocation
- Inventory Management
- Reporting and Analytics
These components work together to streamline operations, improve efficiency, and enhance customer satisfaction.
Preventive Task Forecasting in Field Service Management
Preventive task forecasting is a cutting-edge feature in FSM that uses historical data, current trends, and predictive analytics to anticipate and schedule maintenance tasks before they become urgent. This approach helps prevent equipment failures, reduces downtime, and ensures optimal performance of assets.
How Preventive Task Forecasting Works
- Data Collection: Historical service records, equipment specifications, and environmental factors are analyzed.
- Pattern Recognition: Advanced algorithms identify recurring patterns and potential failure points.
- Risk Assessment: A risk score is assigned to each asset based on its likelihood of failure.
- Scheduling Optimization: Based on the risk assessment, scheduled maintenance is planned proactively.
Benefits of Implementing Preventive Task Forecasting
- Reduced Emergency Calls: By addressing issues before they occur, emergency calls decrease significantly.
- Extended Equipment Lifespan: Regular maintenance prevents premature wear and tear.
- Improved Customer Satisfaction: Predictive maintenance leads to more reliable services and fewer disruptions.
- Cost Savings: Proactive maintenance reduces repair costs and extends the life of equipment.
- Increased Efficiency: Optimized scheduling minimizes travel time and improves resource utilization.
Implementation Strategies for Field Service Managers
Implementing preventive task forecasting in FSM requires careful planning and execution. Here are some strategies for field service managers:
1. Assess Current Operations
Conduct a thorough analysis of your current FSM processes, identifying areas where preventive maintenance can be integrated.
2. Choose the Right Technology
Select an FSM software that offers advanced predictive analytics capabilities. Ensure the system can integrate with your existing tools and processes.
3. Train Your Team
Provide comprehensive training to your technicians on the new forecasting system and its benefits.
4. Gradual Implementation
Start with a pilot program in a specific region or for a particular service type before rolling out company-wide.
5. Continuous Monitoring and Improvement
Regularly review the effectiveness of the preventive task forecasting system and gather feedback from both customers and technicians.
Best Practices for Field Service Managers
- Regularly update equipment records and maintenance histories.
- Utilize real-time data to adjust schedules dynamically.
- Implement a tiered response system for urgent vs. non-urgent tasks.
- Conduct regular performance reviews to optimize scheduling algorithms.
- Foster a culture of continuous improvement within your team.
Challenges and Considerations
While preventive task forecasting offers numerous benefits, field service managers should be aware of some challenges:
- Initial Investment: Implementing advanced FSM systems requires significant upfront costs.
- Data Accuracy: The quality of predictions depends heavily on the accuracy and completeness of historical data.
- Technological Complexity: Some teams may struggle to adapt to new technologies and algorithms.
- Resistance to Change: Employees may resist changes to established workflows and scheduling practices.
Conclusion
Field Service Management with preventive task forecasting represents a significant leap forward in operational efficiency and customer satisfaction. By leveraging advanced analytics and predictive modeling, companies can proactively manage their assets, reduce downtime, and deliver more reliable services.
As technology continues to evolve, we can expect even more sophisticated FSM solutions to emerge. Field service managers who embrace these innovations will be well-positioned to lead their organizations into a future characterized by increased efficiency, reduced costs, and improved customer experiences.
Remember, the key to successful implementation lies in careful planning, thorough training, and a commitment to continuous improvement. By following the strategies outlined in this article, field service managers can harness the power of preventive task forecasting to transform their operations and stay ahead in today’s competitive market.