Field Service Management with Predictive Time-to-Repair Estimates Optimizing Operations Through Data Analytics
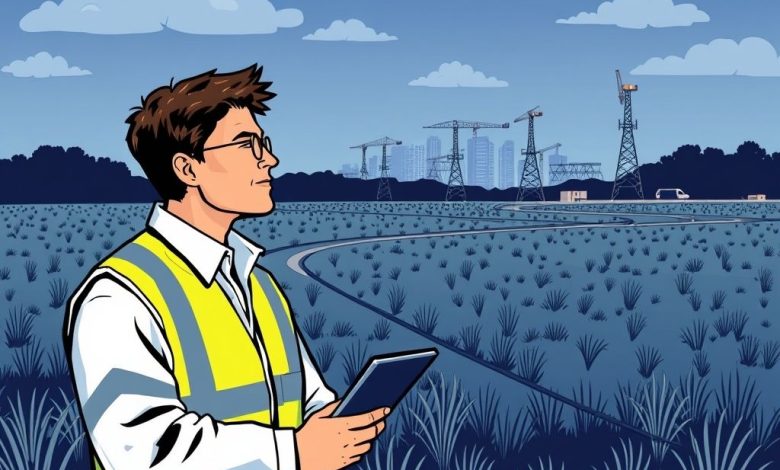
Field Service Management with Predictive Time-to-Repair Estimates
- Introduction
- Understanding Field Service Management
- The Rise of Predictive Analytics in FSM
- Benefits of Implementing Predictive Time-to-Repair Estimates
- Improved Accuracy
- Enhanced Customer Experience
- Increased Efficiency
- Data-Driven Decision Making
- Competitive Advantage
- Challenges in Implementing Predictive Analytics
- Best Practices for Successful Implementation
- Start Small
- Invest in Data Quality
- Provide Training
- Regular Monitoring and Adjustment
- Leverage Real-Time Feedback
- Conclusion
Introduction
Field service management (FSM) is a critical component of many industries, particularly in sectors such as HVAC, electrical work, plumbing, and home maintenance. The ability to efficiently manage and dispatch field technicians is essential for providing excellent customer service while maintaining profitability. In recent years, advancements in technology have led to the integration of predictive analytics into FSM systems, revolutionizing how companies estimate and manage repair times.
This article will explore the concept of field service management, its importance, and how predictive time-to-repair estimates have transformed the industry. We’ll delve into the benefits and challenges of implementing such systems, as well as best practices for successful integration.
Understanding Field Service Management
Field service management refers to the processes and systems used to coordinate and execute field-based service activities. These activities typically involve sending trained technicians to customers’ locations to perform maintenance, repairs, or installations. Effective FSM involves several key aspects:
- Work order management
- Resource allocation
- Technician scheduling
- Inventory management
- Customer communication
Traditionally, FSM relied heavily on manual processes and guesswork when estimating repair times. However, this approach often led to inaccurate timelines and frustrated customers.
The Rise of Predictive Analytics in FSM
Predictive analytics has become increasingly important in various industries, including field service management. By leveraging historical data, machine learning algorithms, and real-time information, companies can now make more accurate predictions about repair times.
Key features of predictive time-to-repair estimates include:
- Historical data analysis
- Machine learning models
- Real-time sensor data integration
- Dynamic adjustments based on changing conditions
These advanced tools allow companies to provide more precise estimates to customers, improve scheduling accuracy, and optimize resource allocation.
Benefits of Implementing Predictive Time-to-Repair Estimates
The integration of predictive analytics into FSM systems offers numerous advantages:
Improved Accuracy
Predictive models can analyze vast amounts of historical data to identify patterns and trends. This allows for more accurate time estimations, reducing the likelihood of underestimating or overestimating repair times.
Enhanced Customer Experience
By providing more accurate estimates, companies can manage customer expectations more effectively. This leads to increased satisfaction and reduced complaints about delayed appointments.
Increased Efficiency
With improved scheduling accuracy, companies can allocate resources more efficiently. This may result in cost savings through optimized routes and reduced overtime.
Data-Driven Decision Making
FSM managers can rely on empirical data rather than intuition when making decisions about staffing levels, vehicle maintenance schedules, and inventory management.
Competitive Advantage
Companies that adopt predictive analytics in FSM stand out from competitors who still rely on traditional methods. This can lead to market differentiation and potential business growth.
Challenges in Implementing Predictive Analytics
While the benefits of predictive analytics in FSM are significant, there are challenges to consider:
Initial Investment
Implementing a sophisticated predictive analytics system requires substantial upfront investment in technology, training, and potentially hiring data scientists or analysts.
Data Quality Issues
The effectiveness of predictive models depends on the quality and completeness of available data. Poor data quality can lead to inaccurate predictions.
Integration Complexity
Integrating predictive analytics with existing FSM systems can be complex, requiring careful planning and potentially involving multiple software vendors.
Change Management
Adopting new technologies often requires cultural shifts within organizations. Some employees may resist the change, especially if they’re accustomed to traditional methods.
Best Practices for Successful Implementation
To overcome the challenges and maximize the benefits of predictive analytics in FSM, consider the following best practices:
Start Small
Begin by implementing predictive analytics for a subset of your services or regions. This allows for testing and refinement before full-scale deployment.
Invest in Data Quality
Ensure that your data collection and management processes are robust. Clean and validate data regularly to maintain its integrity.
Provide Training
Offer comprehensive training to all staff members involved in the FSM process. This includes technicians, dispatchers, and management personnel.
Regular Monitoring and Adjustment
Continuously monitor the performance of your predictive models and be prepared to adjust parameters or update models as needed.
Leverage Real-Time Feedback
Encourage feedback from both customers and technicians to refine your predictive models and improve overall efficiency.
Conclusion
Field service management with predictive time-to-repair estimates represents a significant advancement in the industry. By leveraging the power of predictive analytics, companies can improve accuracy, enhance customer experience, increase efficiency, and gain a competitive edge.
As technology continues to evolve, we can expect even more sophisticated tools to emerge. The key for field service managers will be to stay ahead of the curve, embracing innovation while ensuring that new technologies align with their company’s goals and values.
In conclusion, the integration of predictive analytics into field service management is not just a trend – it’s a necessity for companies seeking to remain competitive in today’s fast-paced, technology-driven world.