Field Service Management for Refrigerated Transport Maintenance
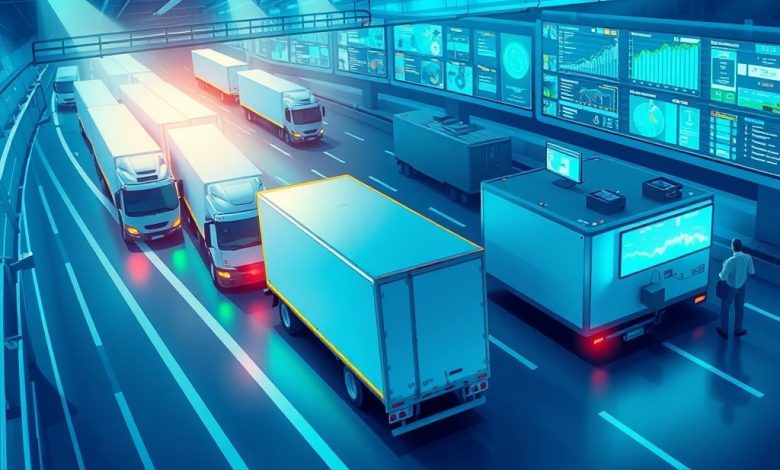
Introduction
Refrigerated transport plays a crucial role in maintaining food safety and quality during transportation. The maintenance of refrigerated vehicles requires efficient field service management systems to ensure timely and effective repairs. This article explores the importance of field service management in refrigerated transport maintenance, highlighting its benefits, challenges, and best practices.
- Benefits of Effective Field Service Management
- Challenges in Refrigerated Transport Maintenance
- Best Practices for Field Service Management in Refrigerated Transport Maintenance
- 1. Invest in Advanced Technology
- 2. Develop Comprehensive Training Programs
- 3. Establish Clear Communication Channels
- 4. Prioritize Preventive Maintenance
- 5. Foster Collaboration Between Departments
- Conclusion
Benefits of Effective Field Service Management
- Improved Response Time
Effective field service management allows companies to respond quickly to maintenance requests. This rapid response time ensures that refrigerated vehicles are back on the road as soon as possible, minimizing downtime and potential losses due to delayed deliveries. - Enhanced Customer Satisfaction
By providing prompt and reliable service, companies can improve customer satisfaction. Satisfied customers are more likely to continue doing business with the company and recommend it to others. - Increased Efficiency
Automated scheduling and dispatching systems streamline the process of assigning technicians to maintenance tasks. This efficiency leads to better resource allocation and reduced operational costs. - Data-Driven Decision Making
Modern field service management systems provide valuable insights into vehicle performance, technician productivity, and maintenance patterns. These data points enable informed decision-making regarding fleet management and resource allocation.
Challenges in Refrigerated Transport Maintenance
Despite the benefits, field service management in refrigerated transport maintenance faces several challenges:
- Specialized Knowledge Required
Technicians need specialized knowledge to work on refrigerated vehicles, which can limit the pool of available skilled workers. - Time-Sensitive Nature of Repairs
Delays in maintenance can lead to spoilage of perishable goods, resulting in significant financial losses. - Remote Locations
Many refrigerated transport operations occur in remote areas, making it challenging to quickly dispatch technicians when needed. - Technological Complexity
Modern refrigerated vehicles often feature advanced temperature control systems, requiring sophisticated diagnostic tools and expertise.
Best Practices for Field Service Management in Refrigerated Transport Maintenance
To overcome the challenges and maximize the benefits of field service management, consider implementing the following best practices:
1. Invest in Advanced Technology
Implement cloud-based field service management software that offers real-time tracking, automated scheduling, and mobile access for technicians.
2. Develop Comprehensive Training Programs
Create training programs that focus on both general vehicle maintenance and specialized refrigeration systems. This ensures that technicians have the necessary skills to diagnose and repair issues efficiently.
3. Establish Clear Communication Channels
Implement robust communication systems that enable seamless interaction between dispatchers, technicians, and customers. This includes real-time updates on maintenance status and estimated completion times.
4. Prioritize Preventive Maintenance
Implement regular preventive maintenance schedules based on vehicle usage patterns and manufacturer recommendations. This helps identify potential issues before they become major problems.
5. Foster Collaboration Between Departments
Encourage collaboration between field service teams and other departments, such as logistics and customer support. This integrated approach ensures a cohesive response to maintenance needs and improves overall operational efficiency.
Conclusion
Field service management plays a critical role in maintaining the reliability and efficiency of refrigerated transport operations. By implementing effective field service management systems and adhering to best practices, companies can improve their response time, enhance customer satisfaction, increase efficiency, and make data-driven decisions.
However, challenges such as specialized knowledge requirements, time-sensitive nature of repairs, remote locations, and technological complexity must be addressed through strategic planning and investment in technology and training.
As the refrigerated transport industry continues to evolve, companies that prioritize field service management will be better positioned to meet the demands of an increasingly complex logistics landscape. By leveraging advanced technologies and fostering a culture of continuous improvement, field service managers can ensure that refrigerated vehicles remain operational, maintaining food safety and quality throughout the transportation process.