Field Service Management for Fast Food Chain Equipment
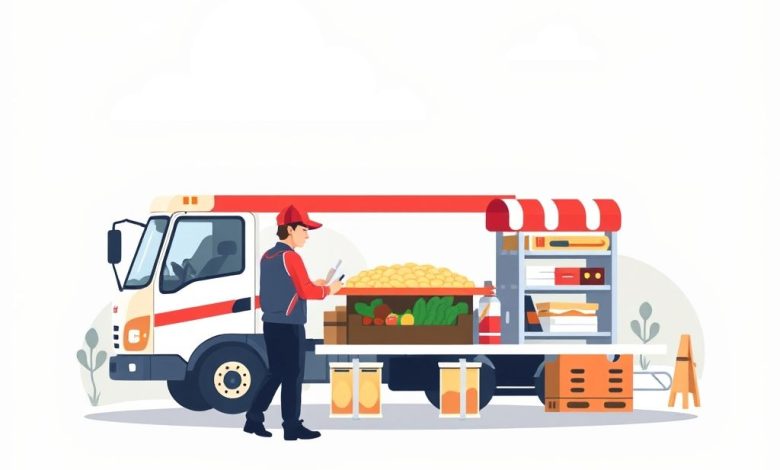
Introduction
Field Service Management (FSM) is a crucial aspect of maintaining equipment in fast food chains. It involves managing and coordinating the activities of technicians who travel to various locations to perform maintenance, repairs, and installations. In the fast food industry, FSM plays a vital role in ensuring that equipment operates efficiently and effectively, minimizing downtime and improving overall customer satisfaction.
The Importance of FSM in Fast Food Chains
Fast food chains rely heavily on specialized equipment such as fryers, grills, refrigerators, and point-of-sale systems. These machines require regular maintenance to function optimally. FSM helps fast food chains manage this equipment effectively by:
- Scheduling routine maintenance visits
- Tracking equipment performance and identifying potential issues early
- Coordinating emergency repairs quickly
- Ensuring compliance with health and safety regulations
Key Components of Field Service Management Systems
Modern FSM systems typically include several key components:
- Work Order Management
- Creation and assignment of service requests
- Prioritization based on urgency and impact
- Tracking of work completion status
2. Scheduling and Dispatching
- Automated scheduling based on technician availability and job priority
- Real-time dispatching of nearest available technicians
- Route optimization for efficient travel
3. Inventory Management
- Tracking of spare parts and equipment
- Automatic ordering of replacement parts when needed
- Optimization of inventory levels to minimize stockouts
4. Customer Relationship Management (CRM)
- Storage of customer information and service history
- Communication with customers about scheduled visits or completed work
- Collection of feedback for continuous improvement
5. Reporting and Analytics
- Generation of reports on equipment performance and maintenance trends
- Identification of common issues across multiple locations
- Analysis of cost-effectiveness of different maintenance strategies
Implementing FSM in Fast Food Chains
Implementing an effective FSM system requires careful planning and execution:
- Assessment of Current Operations
- Evaluate the current state of equipment management
- Identify pain points and areas for improvement
2. Selection of FSM Software
- Choose a system that aligns with your specific needs
- Consider factors such as ease of use, scalability, and integration capabilities
3. Training and Onboarding
- Provide comprehensive training to all staff involved
- Ensure smooth transition from existing systems to new FSM software
4. Phased Implementation
- Start with a pilot program in a few locations
- Gradually roll out to other sites once initial results are positive
5. Continuous Improvement
- Regularly review and refine the FSM process
- Gather feedback from technicians and customers to enhance the system
Challenges in Field Service Management for Fast Food Chains
Despite its importance, implementing and maintaining an effective FSM system can face several challenges:
- Equipment Variety
- Fast food chains often have a wide range of specialized equipment
- This variety can make it challenging to standardize maintenance procedures
2. High Turnover Rates
- Technicians may leave the company frequently
- Ensuring consistent quality of service can be difficult
3. Time-Sensitive Nature of Repairs
- Equipment failures can occur at any time, requiring immediate attention
- Coordinating emergency repairs while minimizing disruption to business operations is crucial
4. Regulatory Compliance
- Fast food chains must adhere to strict health and safety regulations
- FSM systems must ensure compliance with these regulations during maintenance activities
5. Cost Management
- Balancing the need for regular maintenance with operational costs
- Optimizing resource allocation to maximize efficiency
Best Practices for Effective FSM in Fast Food Chains
To overcome the challenges and achieve success with FSM, consider the following best practices:
- Standardized Procedures
- Develop clear, standardized operating procedures for all equipment types
- Ensure all technicians follow these procedures consistently
2. Cross-Training
- Train technicians on multiple equipment types to improve flexibility
- Reduce downtime by having skilled technicians handle various tasks
3. Proactive Maintenance
- Implement predictive maintenance techniques using data analytics
- Perform routine checks and minor adjustments before major issues arise
4. Customer Communication
- Keep customers informed about scheduled visits and completed work
- Address concerns promptly to maintain high customer satisfaction
5. Performance Metrics
- Establish key performance indicators (KPIs) for FSM activities
- Regularly review and analyze these metrics to identify areas for improvement
6. Integration with Other Systems
- Integrate FSM with POS systems and inventory management software
- Streamline processes and reduce manual data entry
Conclusion
Field Service Management is a critical component of maintaining fast food chain equipment. By implementing an effective FSM system, fast food chains can significantly improve their equipment’s reliability, reduce downtime, and enhance overall customer experience. As technology continues to evolve, FSM systems will become even more sophisticated, incorporating artificial intelligence and Internet of Things (IoT) devices to predict and prevent equipment failures.
For field service managers, staying up-to-date with the latest FSM technologies and best practices is essential. Continuously seeking feedback from both technicians and customers will help refine the FSM process, ensuring it remains aligned with the evolving needs of fast food chains.