Field Service Management for Cold Storage Equipment Optimizing Maintenance and Efficiency
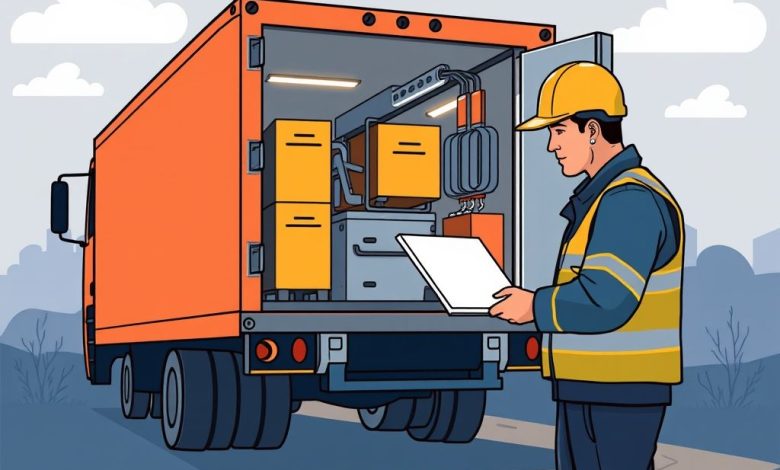
Introduction
Field Service Management (FSM) is crucial for maintaining cold storage equipment, ensuring optimal performance and longevity. Cold storage facilities require precise temperature control and humidity management to preserve perishable goods. Effective FSM strategies help minimize downtime, reduce energy consumption, and maintain product quality.
Importance of FSM in Cold Storage
Cold storage facilities face unique challenges:
- Temperature fluctuations can lead to spoilage and financial losses
- Equipment failures can disrupt entire supply chains
- Energy efficiency is critical due to high power consumption
Proper FSM helps address these issues by:
- Implementing preventive maintenance schedules
- Conducting regular inspections and repairs
- Optimizing routes and scheduling for efficient operations
Key Components of FSM Systems
Modern FSM systems typically include:
- Work Order Management
- Centralized platform for creating, assigning, and tracking work orders
- Automated notifications for technicians and customers
2. Scheduling and Dispatch
- Real-time scheduling based on priority and technician availability
- Route optimization algorithms for efficient travel
3. Inventory Management
- Tracking of spare parts and consumables
- Automatic reordering based on usage patterns
4. Customer Portal
- Self-service options for customers to request services
- Access to appointment history and completed jobs
5. Reporting and Analytics
- Performance metrics for technicians and equipment
- Identification of trends and areas for improvement
Best Practices for FSM Implementation
To ensure successful implementation of FSM for cold storage equipment:
- Standardize processes across all locations
- Invest in proper training for technicians
- Integrate FSM system with existing ERP and CRM systems
- Regularly review and update FSM policies
- Foster collaboration between FSM team and facility managers
Challenges in FSM for Cold Storage
Despite its importance, FSM for cold storage faces several challenges:
- Limited visibility into equipment condition
- Difficulty in scheduling during off-hours
- Ensuring compliance with food safety regulations
Addressing these challenges requires:
- Implementing predictive maintenance techniques
- Utilizing IoT sensors for real-time monitoring
- Developing flexible scheduling protocols
Case Study: Improved Efficiency through FSM
A large cold storage facility implemented a comprehensive FSM solution:
- Reduced average response time from 48 hours to 24 hours
- Decreased equipment downtime by 30%
- Achieved 15% reduction in energy consumption
This success story demonstrates the tangible benefits of effective FSM in cold storage environments.
Conclusion
Field Service Management plays a vital role in optimizing cold storage equipment performance. By implementing robust FSM strategies, facilities can improve efficiency, reduce costs, and enhance customer satisfaction. As technology continues to evolve, FSM solutions will become even more sophisticated, enabling smarter decision-making and better resource allocation in cold storage operations.
As field service managers, it’s essential to stay informed about the latest FSM trends and best practices to maintain competitive advantage in this critical sector of the logistics industry.