Field Service Management for Building Automation Systems
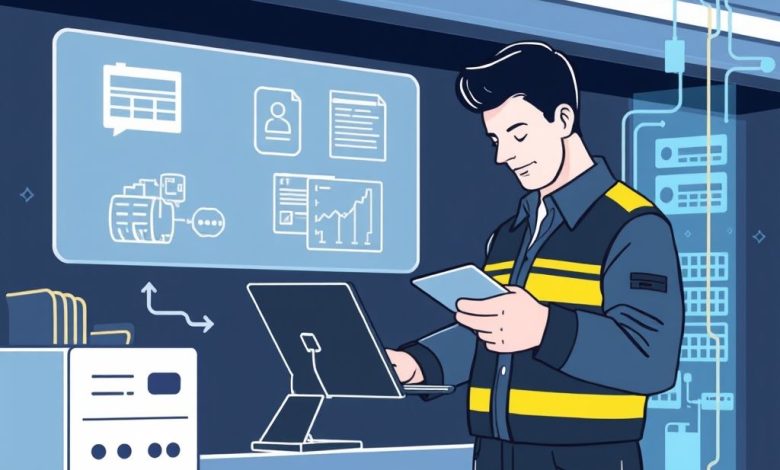
Introduction
Building automation systems (BAS) have become increasingly sophisticated in recent years, integrating various technologies such as HVAC control, lighting management, security systems, and energy monitoring. As these systems grow more complex, the need for efficient field service management becomes crucial. This article explores the importance of field service management in building automation systems, its challenges, and best practices for implementation.
The Role of Field Service Management in BAS
Field service management (FSM) refers to the processes and tools used to manage and coordinate work orders, schedules, and resources for on-site maintenance and repairs. In the context of building automation systems, FSM plays a critical role in ensuring optimal performance, reducing downtime, and improving overall efficiency.
Benefits of Effective FSM in BAS
- Improved Response Time: FSM allows for quick identification and prioritization of issues, enabling faster response times to minimize disruptions in building operations.
- Enhanced Customer Satisfaction: By providing prompt and reliable service, organizations can build trust and loyalty among their clients.
- Cost Reduction: Efficient scheduling and resource allocation help reduce operational costs associated with unnecessary travel or overtime.
- Data-driven Decision Making: FSM systems provide valuable insights into equipment performance, usage patterns, and potential areas for improvement.
Challenges in Implementing FSM for BAS
Despite its benefits, implementing effective field service management for building automation systems presents several challenges:
- Complexity of BAS: The intricate nature of modern BAS requires specialized knowledge, making it challenging to find qualified technicians.
- Integration Issues: Seamlessly integrating FSM software with existing BAS platforms can be technically demanding.
- Real-time Communication: Ensuring reliable communication between field technicians and central dispatch teams is crucial but can be problematic in large-scale operations.
- Regulatory Compliance: Various industries have specific regulations regarding service records and reporting, which FSM systems must adhere to.
Best Practices for Implementing FSM in BAS
To overcome the challenges and maximize the benefits of FSM in building automation systems, consider the following best practices:
- Invest in Comprehensive FSM Software: Choose a robust FSM solution that offers features such as scheduling, inventory management, and mobile workforce optimization.
- Provide Ongoing Training: Ensure that all staff members, including dispatchers and technicians, receive regular training on both the FSM software and the BAS they work with.
- Implement Real-time Communication Tools: Utilize mobile apps and cloud-based platforms to facilitate seamless communication between field technicians and central dispatch teams.
- Establish Clear SLAs: Set Service Level Agreements (SLAs) that outline response times, resolution rates, and other performance metrics to ensure consistent quality of service.
- Leverage IoT Integration: Take advantage of Internet of Things (IoT) capabilities to monitor equipment health remotely and predict potential issues before they occur.
- Regular Audits and Performance Reviews: Conduct periodic assessments of FSM processes and technician performance to identify areas for improvement.
- Foster Collaboration: Encourage open communication between different departments within the organization to ensure a cohesive approach to BAS maintenance and management.
Case Study: Efficient FSM Implementation at a Large Commercial Complex
The XYZ Corporation operates a 50-story office complex with a sophisticated BAS. Prior to implementing a comprehensive FSM system, the company faced frequent disruptions due to delayed responses and inefficient scheduling. Here’s how they improved their FSM processes:
- System Selection: The corporation chose a FSM platform specifically designed for building automation systems, integrating seamlessly with their existing BAS.
- Technician Training: All 30+ technicians underwent intensive training on the new FSM software and the intricacies of the BAS.
- Mobile Workforce Optimization: Technicians were equipped with ruggedized tablets running the FSM app, enabling them to access schedules, parts lists, and real-time updates while on-site.
- Predictive Maintenance: The FSM system was configured to analyze historical data and predict potential equipment failures, allowing for proactive maintenance scheduling.
- Customer Portal: A secure online portal was created for tenants to report issues directly to the FSM system, streamlining the request process.
Results after implementation:
- Response time reduced by 40%
- First-time fix rate increased by 25%
- Overall customer satisfaction score improved by 35%
Conclusion
Field service management plays a critical role in ensuring the optimal performance and longevity of building automation systems. By implementing effective FSM strategies, organizations can improve efficiency, reduce costs, and enhance customer satisfaction. As technology continues to advance, the importance of FSM in managing complex BAS will only grow, making it essential for businesses to invest in robust solutions and ongoing training to stay competitive in this rapidly evolving landscape.