Field Service Management with Preventive Maintenance Workflows Optimizing Operations and Enhancing Customer Satisfaction
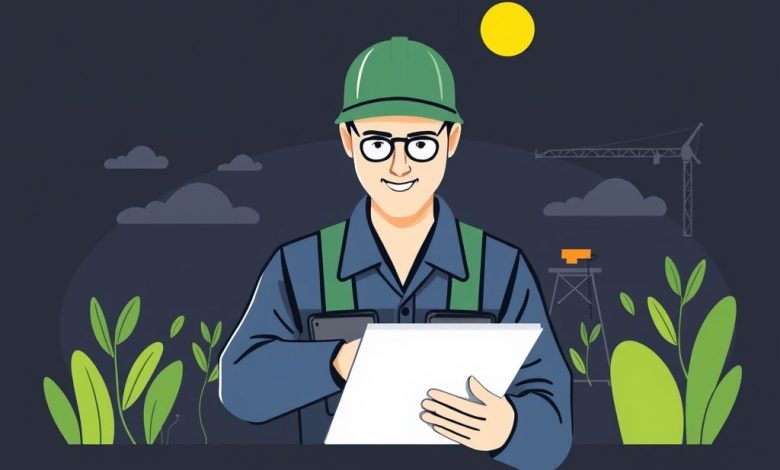
Introduction
Field Service Management (FSM) is a critical component of many industries, particularly in sectors such as HVAC, electrical work, plumbing, and manufacturing. It involves managing and coordinating the activities of technicians who provide services directly at customer locations. In recent years, FSM has evolved significantly with advancements in technology, leading to more efficient and effective management of field operations.
One key aspect of modern FSM is the implementation of preventive maintenance workflows. These workflows aim to proactively maintain equipment and systems to prevent breakdowns and minimize downtime. This approach not only improves operational efficiency but also enhances customer satisfaction by ensuring consistent service delivery.
In this article, we will explore the concept of Field Service Management with a focus on preventive maintenance workflows. We’ll discuss the importance of FSM, the role of preventive maintenance, how to implement these workflows, and the benefits they bring to both businesses and customers.
- The Importance of Field Service Management
- Preventive Maintenance in Field Service Management
- Implementing Preventive Maintenance Workflows
- 1. Assess Current Operations
- 2. Develop a Maintenance Schedule
- 3. Assign Tasks to Technicians
- 4. Utilize Technology
- 5. Monitor and Adjust
- Benefits of Preventive Maintenance Workflows
- Challenges in Implementing Preventive Maintenance Workflows
- Conclusion
The Importance of Field Service Management
Field Service Management encompasses various aspects of service delivery, including scheduling, dispatching, resource allocation, and job execution. Effective FSM ensures that:
- Customer needs are met promptly and efficiently
- Resources are utilized optimally
- Operational costs are minimized
- Quality of service is maintained consistently
With the increasing complexity of modern equipment and systems, FSM has become crucial for maintaining competitive advantage in many industries. Companies that excel in FSM tend to have higher customer retention rates, improved operational efficiency, and better financial performance compared to those lagging behind in this area.
Preventive Maintenance in Field Service Management
Preventive maintenance refers to scheduled maintenance tasks performed on equipment before it fails or shows signs of wear. This approach differs from reactive maintenance, which addresses issues only after they occur. By implementing preventive maintenance workflows, organizations can:
- Reduce unexpected equipment failures
- Minimize downtime and associated costs
- Extend the lifespan of equipment
- Improve overall operational efficiency
Preventive maintenance involves regular inspection, cleaning, lubrication, and replacement of parts based on predetermined schedules. It requires careful planning and execution to ensure that all necessary tasks are completed efficiently without disrupting normal operations.
Implementing Preventive Maintenance Workflows
To implement preventive maintenance workflows effectively, organizations should consider the following steps:
1. Assess Current Operations
Begin by evaluating your current FSM processes and identifying areas where preventive maintenance can be integrated. Analyze equipment performance data, customer feedback, and operational metrics to pinpoint opportunities for improvement.
2. Develop a Maintenance Schedule
Create detailed schedules for each piece of equipment based on its type, age, usage patterns, and manufacturer recommendations. These schedules should account for both routine tasks and more intensive maintenance procedures.
3. Assign Tasks to Technicians
Ensure that technicians have the necessary skills and training to perform preventive maintenance tasks. Create job cards or work orders that outline specific tasks to be completed during each visit.
4. Utilize Technology
Leverage field service management software to streamline scheduling, dispatching, and task assignment. Many modern FSM systems offer features specifically designed for preventive maintenance, such as automated reminders and customizable workflows.
5. Monitor and Adjust
Continuously monitor the effectiveness of your preventive maintenance program. Collect data on equipment performance, technician productivity, and customer satisfaction. Use this information to refine your schedules and improve your overall FSM strategy.
Benefits of Preventive Maintenance Workflows
Implementing preventive maintenance workflows in Field Service Management offers numerous benefits:
- Reduced Downtime: By proactively maintaining equipment, organizations can minimize unexpected breakdowns and associated downtime.
- Extended Equipment Life: Regular maintenance helps extend the lifespan of equipment, reducing the need for premature replacements.
- Improved Customer Satisfaction: Consistent service delivery and reduced downtime contribute to higher customer satisfaction rates.
- Cost Savings: While initial investment may be required, preventive maintenance often leads to long-term cost savings by reducing repair costs and minimizing emergency service calls.
- Enhanced Operational Efficiency: Streamlined processes and optimized resource allocation contribute to improved overall operational efficiency.
Challenges in Implementing Preventive Maintenance Workflows
Despite the numerous benefits, implementing preventive maintenance workflows can present several challenges:
- Initial Investment: Setting up a robust preventive maintenance program requires significant upfront investment in technology, training, and process development.
- Resistance to Change: Some technicians may resist changes to their established routines, requiring careful communication and training.
- Balancing Act: Finding the right balance between proactive maintenance and reactive repairs can be challenging, especially in fast-paced environments.
- Data Management: Properly managing and analyzing the vast amounts of data generated by preventive maintenance activities can be overwhelming without the right tools and processes.
Conclusion
Field Service Management with preventive maintenance workflows represents a powerful combination for optimizing field operations. By proactively maintaining equipment and systems, organizations can significantly improve operational efficiency, reduce costs, and enhance customer satisfaction.
As technology continues to evolve, we can expect further advancements in FSM and preventive maintenance strategies. Field service managers who embrace these innovations will be well-positioned to drive success in their organizations and stay competitive in today’s fast-paced business environment.
Remember, effective implementation of preventive maintenance workflows requires commitment, resources, and continuous improvement. By following the steps outlined in this article and addressing the challenges head-on, organizations can reap the full benefits of this powerful approach to Field Service Management.