Field Service Management for Maintenance Logs Optimizing Operations and Enhancing Efficiency
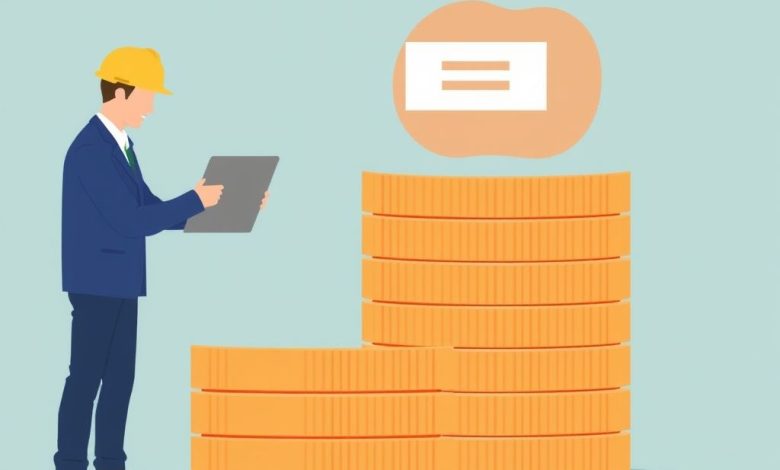
Introduction
Field Service Management (FSM) is a critical component of modern business operations, particularly in industries such as construction, manufacturing, and facilities management. One of the key aspects of FSM is maintenance logs, which play a vital role in ensuring equipment reliability, reducing downtime, and optimizing resource allocation. In this article, we will explore the importance of maintenance logs in FSM, discuss various tools and technologies used for their implementation, and examine best practices for effective log management.
- The Importance of Maintenance Logs in Field Service Management
- Tools and Technologies for Maintenance Log Management
- Computerized Maintenance Management Systems (CMMS)
- Enterprise Resource Planning (ERP) Systems
- Internet of Things (IoT) Devices
- Mobile Applications
- Best Practices for Effective Maintenance Log Management
- Challenges in Maintenance Log Management
- Conclusion
The Importance of Maintenance Logs in Field Service Management
Maintenance logs serve several crucial purposes in FSM:
- Equipment tracking: They provide a detailed record of all maintenance activities performed on assets, allowing technicians to quickly locate and assess the status of equipment in the field.
- Preventive maintenance scheduling: By analyzing historical data from maintenance logs, organizations can identify patterns and schedule routine maintenance before issues arise, reducing unexpected breakdowns and extending equipment lifespan.
- Cost reduction: Well-maintained equipment requires less frequent repairs, leading to significant cost savings over time.
- Quality control: Maintenance logs help ensure that all necessary procedures are followed during maintenance tasks, improving overall quality standards.
- Regulatory compliance: Many industries require detailed records of maintenance activities to meet regulatory requirements.
Tools and Technologies for Maintenance Log Management
Several software solutions have emerged to streamline maintenance log management in FSM:
Computerized Maintenance Management Systems (CMMS)
CMMS is one of the most popular tools for managing maintenance logs. These systems typically offer features such as:
- Automated work order creation and assignment
- Inventory management for spare parts and supplies
- Scheduling and reminders for upcoming maintenance tasks
- Reporting and analytics capabilities
Some notable CMMS providers include Hippo CMMS, Fiix, and MaintenX.
Enterprise Resource Planning (ERP) Systems
Many organizations use ERP systems like SAP or Oracle to manage their FSM processes, including maintenance logs. While not specifically designed for maintenance, these systems often have robust logging capabilities integrated into their broader suite of tools.
Internet of Things (IoT) Devices
IoT sensors and devices are increasingly being used to collect real-time data about equipment performance. This data can then be logged and analyzed to predict potential maintenance needs before they occur.
Mobile Applications
Mobile apps allow technicians to access and update maintenance logs directly from the field, streamlining the process and reducing errors associated with manual data entry.
Best Practices for Effective Maintenance Log Management
To maximize the benefits of maintenance logs in FSM, consider implementing the following best practices:
- Standardize log formats: Ensure consistent formatting across all maintenance logs to facilitate easy analysis and reporting.
- Implement regular audits: Periodically review maintenance logs to ensure accuracy and completeness.
- Utilize automation: Leverage automated tools where possible to reduce manual data entry and minimize human error.
- Provide training: Educate technicians on proper log-keeping techniques and the importance of accurate documentation.
- Integrate with other FSM systems: Ensure seamless integration between maintenance logs and other FSM tools for a holistic view of operations.
- Analyze trends: Regularly analyze maintenance log data to identify patterns and optimize maintenance schedules.
- Prioritize security: Implement robust security measures to protect sensitive maintenance data, especially when stored electronically.
- Maintain accessibility: Ensure that maintenance logs are easily accessible to authorized personnel both in the office and in the field.
Challenges in Maintenance Log Management
Despite the numerous benefits, there are several challenges that organizations may face when implementing and maintaining effective maintenance log management:
- Data overload: As maintenance logs grow in volume, it becomes increasingly difficult to extract meaningful insights without advanced analytics tools.
- Technological barriers: Some older equipment may not be compatible with newer digital logging systems, requiring hybrid approaches.
- Resistance to change: Some technicians may resist adopting new logging methods, especially if they feel it adds unnecessary complexity to their workflow.
- Security concerns: Electronic storage of sensitive maintenance data raises cybersecurity risks that must be carefully managed.
- Integration complexities: Combining data from various sources (e.g., IoT devices, CMMS, ERP) can be challenging and may require significant IT resources.
Conclusion
Field Service Management for Maintenance Logs is a critical aspect of modern business operations. By leveraging appropriate tools, implementing best practices, and addressing common challenges, organizations can significantly improve their maintenance processes, reduce costs, enhance equipment reliability, and gain valuable insights into their operations.
As technology continues to evolve, we can expect even more sophisticated solutions for maintenance log management. However, regardless of the tools used, the core principles of accurate, timely, and comprehensive logging remain essential for successful FSM.
By prioritizing maintenance logs and investing in robust FSM systems, organizations can position themselves for long-term success in an increasingly competitive and technologically driven marketplace.