Field Service Management and Digital Twins Revolutionizing Operations with AI and IoT
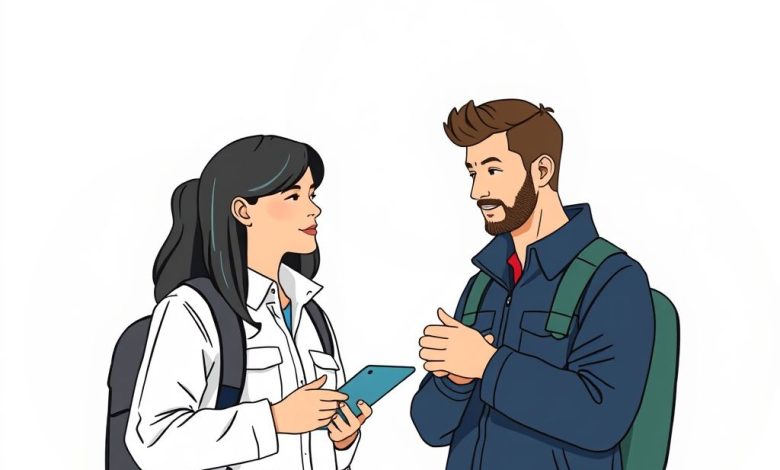
Introduction
Field Service Management (FSM) and Digital Twins are two interconnected technologies revolutionizing how businesses manage their operations and deliver services. FSM focuses on optimizing field-based work processes, while Digital Twins create virtual replicas of physical assets. Together, they form a powerful synergy that enhances efficiency, reduces costs, and improves customer satisfaction.
What is Field Service Management?
Field Service Management refers to the practices and systems used to coordinate and execute tasks performed outside the company’s main office. It encompasses various aspects of service delivery, including scheduling, dispatching, resource allocation, and performance tracking.
Key components of FSM include:
- Scheduling and dispatching software
- Mobile workforce management tools
- Customer relationship management (CRM) systems
- Inventory and parts management
- Reporting and analytics dashboards
What is Digital Twin Technology?
Digital Twin technology creates virtual replicas of physical assets or systems. These virtual models mirror real-world objects, allowing businesses to monitor, analyze, and optimize performance remotely.
Key features of Digital Twin technology:
- Real-time monitoring and data collection
- Predictive maintenance capabilities
- Improved decision-making through data-driven insights
- Enhanced collaboration between physical and digital worlds
The Intersection of Field Service Management and Digital Twins
The integration of FSM and Digital Twins creates a powerful synergy that transforms field service operations. Here are some ways this combination benefits businesses:
- Predictive Maintenance
Digital Twins allow for continuous monitoring of equipment health. By analyzing sensor data from connected devices, businesses can predict potential failures before they occur. This enables proactive scheduling of maintenance visits, reducing downtime and improving overall efficiency.
2. Optimized Resource Allocation
FSM systems can leverage data from Digital Twins to allocate resources more effectively. By knowing exactly where equipment is located and its current status, dispatchers can quickly assign the right technician with the appropriate skills and tools for each job.
3. Enhanced Customer Experience
Real-time monitoring through Digital Twins allows service providers to keep customers informed about the status of their service requests. This transparency builds trust and improves customer satisfaction.
4. Improved Safety
Digital Twins can simulate various scenarios to identify potential safety hazards before they occur in the physical world. This allows businesses to take preventive measures and ensure worker safety.
Implementing Field Service Management and Digital Twins
Implementing FSM and Digital Twin technology requires careful planning and execution:
- Assess Current Operations
Evaluate your current field service processes and identify areas for improvement.
2. Choose Appropriate Technology
Select FSM and Digital Twin solutions that align with your business needs and integrate well with existing systems.
3. Train Staff
Ensure all employees understand how to use new technologies and how they benefit the organization.
4. Gradual Implementation
Introduce new systems gradually, starting with pilot projects or specific departments.
5. Continuous Monitoring and Improvement
Regularly review performance metrics and gather feedback from users to refine and optimize the implementation.
Challenges and Considerations
While the integration of FSM and Digital Twins offers numerous benefits, there are challenges to consider:
- Data Security and Privacy
- Integration Complexity
- Initial Investment Costs
- Change Management within Organizations
Addressing these challenges requires careful planning and ongoing support from management.
Conclusion
The convergence of Field Service Management and Digital Twins represents a significant leap forward in operational efficiency and customer satisfaction. By leveraging real-time data, predictive analytics, and virtual replicas of assets, businesses can streamline their field service operations, reduce costs, and deliver higher quality services.
As this technology continues to evolve, it’s crucial for field service managers to stay informed about the latest developments and adapt their strategies accordingly. The future of field service lies in the seamless integration of digital and physical worlds, and those who embrace this change will be better positioned to thrive in an increasingly competitive market.
By implementing FSM and Digital Twin technology, businesses can transform their field service operations into efficient, responsive, and customer-centric entities that set new standards in the industry.