Revolutionizing Field Service Management How Predictive Maintenance is Transforming the Industry
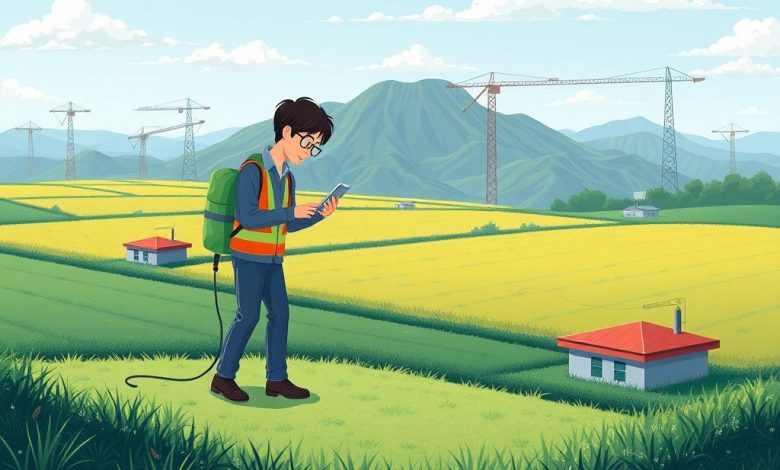
Introduction
Field Service Management (FSM) is a crucial aspect of modern business operations, particularly in industries such as HVAC, electrical, plumbing, and construction. As technology continues to advance, FSM is evolving to incorporate predictive maintenance techniques, revolutionizing how companies manage their field services. In this article, we’ll explore the concept of Field Service Management with Predictive Maintenance, its benefits, implementation strategies, and best practices for field service managers.
- What is Field Service Management?
- Predictive Maintenance in Field Service Management
- Implementing Predictive Maintenance in Field Service Management
- Step 1: Data Collection
- Step 2: Data Analysis
- Step 3: Integration with Existing Systems
- Step 4: Training and Adoption
- Best Practices for Field Service Managers
- Conclusion
What is Field Service Management?
Field Service Management refers to the processes and systems used to manage and coordinate work activities performed outside of a traditional office environment. It encompasses various aspects of service delivery, including scheduling, dispatching, resource allocation, and customer communication. Effective FSM ensures that field technicians have the necessary tools, information, and support to complete jobs efficiently and effectively.
Key Components of Field Service Management
- Scheduling and Dispatching
- Automated scheduling algorithms
- Real-time job assignment
- Route optimization
2. Resource Allocation
- Technician management
- Vehicle tracking
- Inventory control
3. Customer Communication
- Appointment booking
- Job status updates
- Invoice management
4. Work Order Management
- Job creation and assignment
- Task prioritization
- Reporting and analytics
Predictive Maintenance in Field Service Management
Predictive maintenance is an advanced technique that uses data analytics, machine learning algorithms, and IoT sensors to predict equipment failures before they occur. When integrated with FSM, predictive maintenance allows companies to schedule maintenance proactively, reducing downtime and improving overall operational efficiency.
Benefits of Predictive Maintenance in FSM
- Reduced Downtime
- Proactive scheduling minimizes unexpected breakdowns
- Extended equipment lifespan
2. Cost Savings
- Preventive maintenance reduces repair costs
- Optimized resource allocation
3. Improved Customer Satisfaction
- Faster response times
- More reliable service delivery
4. Enhanced Operational Efficiency
- Better resource utilization
- Streamlined workflows
Implementing Predictive Maintenance in Field Service Management
Implementing predictive maintenance in FSM requires a multi-step approach:
Step 1: Data Collection
- Install IoT sensors on equipment
- Collect historical maintenance records
- Gather real-time operational data
Step 2: Data Analysis
- Use machine learning algorithms to analyze collected data
- Identify patterns indicative of potential failures
- Develop predictive models
Step 3: Integration with Existing Systems
- Integrate predictive analytics with FSM software
- Ensure seamless communication between systems
- Train staff on new processes and tools
Step 4: Training and Adoption
- Educate technicians on predictive maintenance techniques
- Provide ongoing support and training
- Encourage adoption of new practices
Best Practices for Field Service Managers
To maximize the benefits of Field Service Management with Predictive Maintenance, consider the following best practices:
- Invest in robust FSM software
- Look for solutions with built-in predictive analytics capabilities
- Ensure compatibility with existing systems
2. Foster a culture of continuous improvement
- Regularly review and refine processes
- Encourage employee feedback and suggestions
3. Prioritize customer satisfaction
- Implement transparent communication channels
- Offer flexible scheduling options
4. Stay updated with industry trends
- Attend conferences and workshops
- Subscribe to relevant publications and newsletters
5. Emphasize technician development
- Provide regular training sessions
- Encourage skill sharing among team members
6. Optimize resource allocation
- Utilize route optimization tools
- Implement efficient scheduling algorithms
7. Maintain accurate records
- Keep detailed logs of jobs and maintenance activities
- Analyze data regularly to identify areas for improvement
8. Consider environmental impact
- Implement eco-friendly practices where possible
- Reduce carbon footprint through optimized routes and schedules
Conclusion
Field Service Management with Predictive Maintenance represents a significant leap forward in operational efficiency and customer satisfaction. By leveraging advanced technologies and data-driven insights, companies can transform their field service operations from reactive to proactive, leading to improved bottom-line results and enhanced customer experiences.
As technology continues to evolve, field service managers must remain adaptable and open to new innovations. By embracing Predictive Maintenance and implementing best practices, businesses can position themselves at the forefront of the FSM industry, ready to meet the challenges of tomorrow’s service landscape.
Remember, the key to success lies not just in adopting new technologies, but in creating a culture of continuous improvement and innovation within your organization. As you embark on this journey towards predictive field service management, stay focused on delivering exceptional value to your customers while optimizing your operations for long-term success.