Optimizing Field Service Management in Oil Gas Field Operations Enhancing Efficiency and Safety
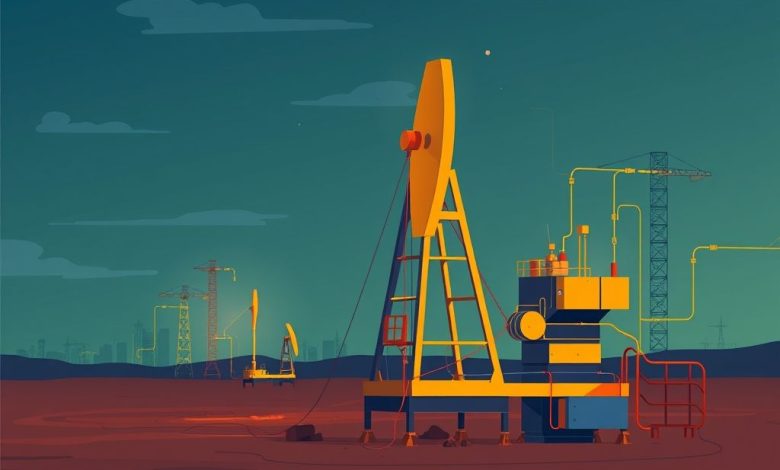
Introduction
Field Service Management (FSM) plays a crucial role in the oil and gas industry, particularly in field operations. It encompasses various aspects of managing and executing tasks related to equipment maintenance, repairs, and overall operational efficiency. In this article, we’ll explore the importance of FSM in oil and gas field operations, its key components, challenges, and best practices.
- The Importance of Field Service Management in Oil & Gas
- Key Components of Field Service Management
- 1. Scheduling and Dispatch
- 2. Work Order Management
- 3. Inventory Management
- 4. Mobile Technology Integration
- 5. Reporting and Analytics
- Challenges in Implementing Field Service Management
- Best Practices for Implementing Field Service Management
- Conclusion
The Importance of Field Service Management in Oil & Gas
Field Service Management is essential for maintaining the integrity and productivity of oil and gas operations. It ensures that equipment is properly maintained, reducing downtime and increasing overall efficiency. Effective FSM also helps in managing resources more efficiently, optimizing schedules, and improving communication between different teams involved in the operation.
Benefits of Implementing FSM
- Improved Operational Efficiency: By streamlining processes and automating routine tasks, FSM helps reduce response times and increase productivity.
- Enhanced Customer Satisfaction: Timely service delivery and better communication lead to higher customer satisfaction rates.
- Cost Reduction: Efficient scheduling and resource allocation help minimize unnecessary expenses.
- Data-driven Decision Making: FSM systems provide valuable insights into operational performance, enabling data-driven decisions.
Key Components of Field Service Management
A robust FSM system typically includes several critical components:
1. Scheduling and Dispatch
This module manages the allocation of technicians to jobs based on their availability, skillset, and location. Advanced scheduling algorithms ensure optimal utilization of resources while minimizing travel time and costs.
2. Work Order Management
This component handles the creation, assignment, and tracking of work orders from initiation to completion. It ensures that all necessary information is captured and that tasks are completed efficiently.
3. Inventory Management
Proper inventory management is crucial in oil and gas operations. This module tracks spare parts, equipment, and consumables, ensuring that technicians have the necessary materials to complete jobs effectively.
4. Mobile Technology Integration
Mobile apps allow technicians to access job details, update statuses, and capture signatures electronically. This real-time data collection improves visibility and reduces paperwork.
5. Reporting and Analytics
Advanced reporting capabilities provide insights into operational performance, including metrics such as first-time fix rates, average response times, and technician productivity.
Challenges in Implementing Field Service Management
Despite its numerous benefits, implementing FSM in oil and gas operations comes with several challenges:
- Complexity of Operations: Oil and gas field operations involve complex equipment and processes, making it challenging to standardize procedures across different sites.
- Remote Locations: Many oil and gas operations take place in remote areas with limited connectivity, posing difficulties in real-time data transmission and updates.
- Regulatory Compliance: Ensuring adherence to industry-specific regulations and safety standards adds complexity to FSM implementation.
- Technological Infrastructure: Some older equipment may not be compatible with modern FSM systems, requiring significant investments in upgrades.
Best Practices for Implementing Field Service Management
To overcome the challenges and maximize the benefits of FSM in oil and gas operations, consider the following best practices:
- Start Small: Begin with a pilot program in a single location before scaling up to larger operations.
- Customize Your Solution: Tailor the FSM system to meet the specific needs of your oil and gas operations, including industry-specific regulations and safety protocols.
- Invest in Training: Ensure that all technicians are properly trained on the new FSM system to maximize its effectiveness.
- Regular Updates: Keep the FSM system updated with the latest features and improvements to stay ahead of operational challenges.
- Continuous Monitoring: Regularly review performance metrics and gather feedback from technicians to identify areas for improvement.
Conclusion
Field Service Management is a critical component of successful oil and gas field operations. By implementing a comprehensive FSM solution, organizations can improve operational efficiency, reduce costs, and enhance customer satisfaction. While challenges exist, the benefits of FSM far outweigh the difficulties in implementation. As technology continues to evolve, FSM systems will become even more sophisticated, enabling oil and gas companies to maintain their competitive edge in an increasingly complex and demanding industry.
By embracing Field Service Management, oil and gas companies can ensure that their field operations run smoothly, efficiently, and safely, ultimately contributing to the success of their overall business strategy.