Field Service Management for Scheduled Inspection Audits
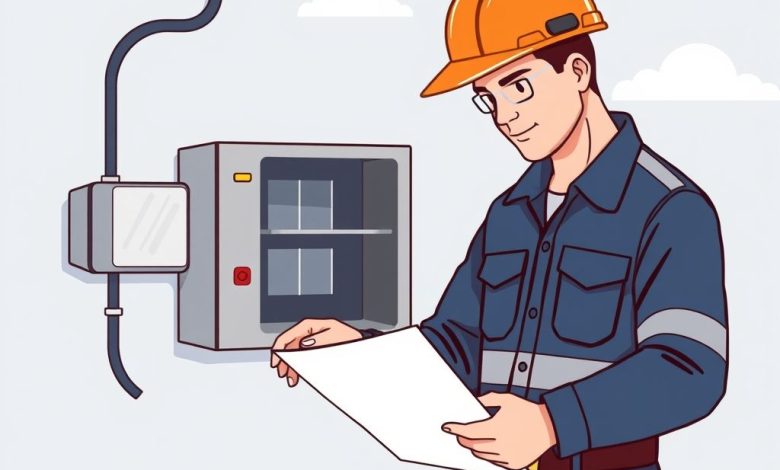
Field Service Management for Scheduled Inspection Audits
Introduction
Field service management (FSM) is a crucial aspect of modern business operations, particularly in industries such as construction, manufacturing, and facilities maintenance. One critical component of FSM is scheduled inspection audits, which play a vital role in ensuring quality control and maintaining high standards across various projects and services. In this article, we will explore the importance of FSM for scheduled inspection audits, discuss key strategies and tools used in this process, and examine best practices for implementing effective FSM systems.
The Importance of Field Service Management for Scheduled Inspection Audits
Scheduled inspection audits are essential for maintaining the integrity and quality of work performed in the field. These audits help ensure that:
- Work is completed according to specifications and industry standards
- Equipment is properly maintained and functioning correctly
- Safety protocols are being followed
- Customer satisfaction levels are consistently high
By incorporating scheduled inspection audits into their FSM processes, organizations can significantly reduce errors, improve efficiency, and enhance overall project outcomes.
Key Strategies and Tools Used in Field Service Management for Scheduled Inspection Audits
- Mobile Technology Integration
Modern FSM systems often incorporate mobile technology to streamline the inspection audit process. This may include:
- Mobile apps for technicians to capture real-time data during inspections
- GPS tracking to monitor technician locations and travel times
- Barcode scanning for quick identification of equipment and materials
These tools enable faster data collection, improved accuracy, and more efficient communication between field staff and back-office teams.
2. Automated Scheduling Systems
Automated scheduling systems are crucial for managing the complexities of FSM, including:
- Optimizing route planning based on geographic location and job requirements
- Ensuring proper allocation of resources and personnel
- Minimizing downtime and reducing travel costs
By leveraging advanced algorithms and machine learning techniques, these systems can significantly improve operational efficiency while reducing manual errors.
3. Data Analytics and Reporting
Effective FSM systems generate valuable insights through data analytics and reporting capabilities. These features allow organizations to:
- Track key performance indicators (KPIs) related to inspection audits
- Identify trends and patterns in inspection results
- Monitor compliance with regulatory requirements
- Optimize resource allocation based on historical data
By leveraging these insights, businesses can make informed decisions to continuously improve their FSM processes and inspection audit procedures.
4. Quality Control Measures
Implementing robust quality control measures is essential for successful FSM and scheduled inspection audits. Some best practices include:
- Establishing clear criteria for passing inspections
- Conducting regular training sessions for technicians on inspection procedures
- Implementing a system for addressing and resolving issues identified during audits
- Regularly reviewing and updating inspection checklists to reflect changing industry standards
Best Practices for Implementing Effective Field Service Management Systems
To maximize the benefits of FSM for scheduled inspection audits, consider the following best practices:
- Standardize Processes and Procedures
Develop and implement standardized operating procedures for all aspects of FSM, including inspection audits. This ensures consistency across all jobs and helps identify potential issues early in the process.
2. Invest in Employee Training
Provide ongoing training and development opportunities for field staff to ensure they have the necessary skills and knowledge to perform high-quality inspections effectively.
3. Foster Collaboration Between Field and Office Teams
Encourage open communication between field technicians and office-based staff to ensure seamless coordination of tasks, prompt issue resolution, and efficient data management.
4. Continuously Improve and Adapt
Regularly review and refine FSM processes based on feedback from both field staff and customers. Stay updated with the latest technologies and industry trends to maintain competitiveness.
5. Ensure Compliance with Regulations
Stay informed about relevant regulations and industry standards, and ensure that your FSM system includes features to support compliance with these requirements.
Conclusion
Field service management plays a critical role in ensuring the success of scheduled inspection audits. By integrating cutting-edge technologies, implementing robust quality control measures, and adhering to best practices, organizations can significantly enhance their ability to deliver high-quality services while maintaining operational efficiency.
As the field service industry continues to evolve, it is essential for companies to stay ahead of the curve by investing in innovative FSM solutions and continually refining their processes. By doing so, they can not only meet but exceed customer expectations, drive growth, and establish themselves as leaders in their respective fields.
Remember, effective FSM for scheduled inspection audits is not just about completing checks; it’s about building trust, ensuring quality, and driving long-term success in your organization.